Water Solutions for the Chemical and Petroleum Industry
The petroleum and chemical industry is a sector characterized by complex production processes and intensive water usage. The quality of water used in these sectors is critical for both the efficiency of production processes and the lifespan of equipment. Chemical substances, minerals, and organic pollutants in untreated water can lead to serious problems in production processes. Therefore, the implementation of appropriate water treatment technologies is a vital necessity for businesses.
Water treatment in the oil and chemical industry encompasses various processes such as raw water treatment, boiler feed water preparation, cooling water management, wastewater treatment, and recovery systems. Additionally, these solutions provide economic advantages that support sustainability, as well as ensuring compliance with environmental regulations.
Take a Look at Applications in the Chemical and Petroleum Industry!
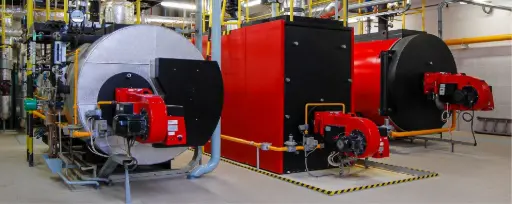
Boiler Feed Water Treatment
Provides high-purity water to prevent scaling and corrosion in boilers, ensuring reliable steam generation for chemical processes.
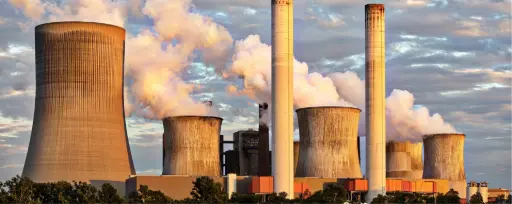
Cooling Water Treatment
Removes impurities and prevents fouling, scaling, and biological growth in cooling systems to maintain efficiency and protect equipment.
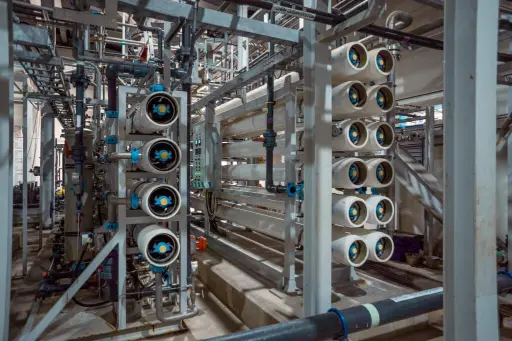
Process Water Treatment
Delivers water of specific quality for chemical reactions, solvent preparation, and material processing, ensuring consistent product quality.
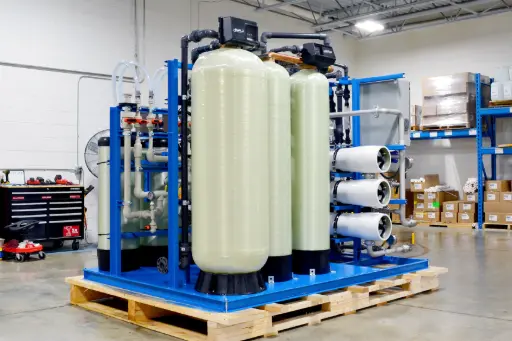
Deionized Water for Chemical Production
Produces ultrapure water required for sensitive chemical processes and to maintain purity in final products.
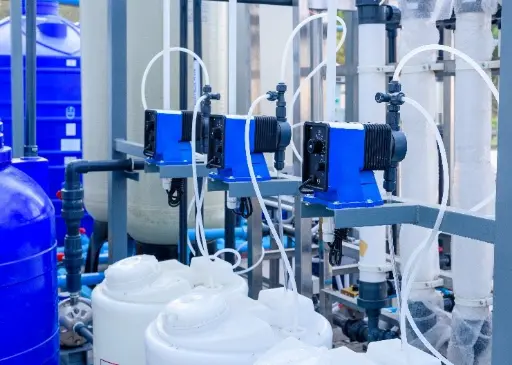
Chemical Dosing Systems
Introduces pH stabilizers, corrosion inhibitors, and antiscalants to optimize water chemistry for specific processes.
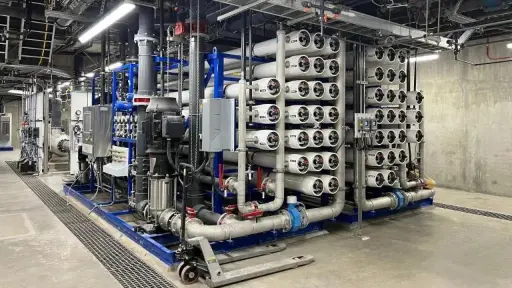
Water Reuse and Recycling
Reclaims water from industrial processes, reducing fresh water consumption and minimizing wastewater generation.
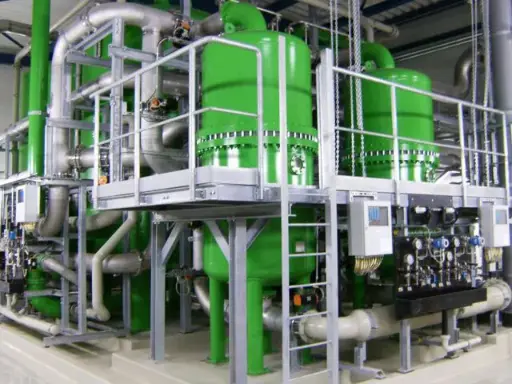
Steam Condensate Treatment
Cleans and reuses condensate in steam systems, reducing water and energy usage in petrochemical plants.
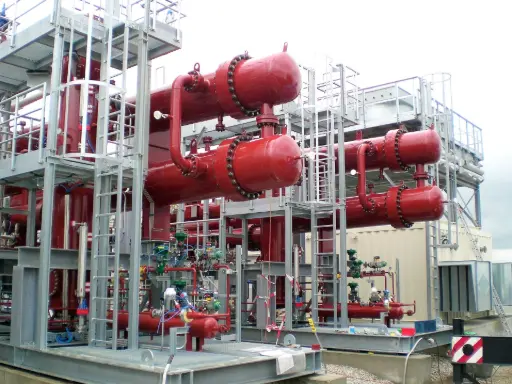
Hydrocarbon Washing and Separation
Uses treated water for cleaning and separating hydrocarbons during refining processes.
Water Treatment Insights for the Chemical & Oil Industry
Why water quality is mission‑critical
In chemical and petroleum plants, every liter of water interacts with catalysts, heat‑exchange surfaces, and separation media. Dissolved ions such as Ca²⁺, Mg²⁺ and SiO₂ promote scaling that throttles heat transfer, while chloride, sulfide and dissolved oxygen accelerate corrosion in piping, columns and boilers. Suspended solids foul membranes; trace hydrocarbons and surfactants destabilise biological steps. Unless raw water is conditioned to exact specifications, production downtime, product contamination and safety risks soar.
Target quality parameters
Typical make‑up or process water specs include:
- Conductivity < 5 µS cm⁻¹ for catalyst preparation and solvent make‑up.
- Silica < 50 ppb to prevent boiler carry‑over into turbines.
- Total Hardness < 0.1 ppm as CaCO₃ to avoid exchanger scale.
- Chloride < 0.5 ppm in high‑pressure steam circuits to limit stress‑corrosion cracking.
- TSS < 1 ppm entering reverse‑osmosis (RO) skids to maximise membrane life.
- Oil & Grease < 10 ppm before biological or advanced oxidation units.
Core treatment challenges
- Variable feed composition – refinery intakes mix surface, well and recycled water, demanding adaptable pre‑treatment.
- High temperatures & organics – condensate return may carry amines, phenols, and 90 °C heat; materials and resins must be resistant.
- Stringent discharge permits – many sites must now achieve < 10 ppm COD or move toward zero‑liquid‑discharge (ZLD).
- Footprint limits – brownfield revamps often require modular, skid‑mounted solutions.
Integrated treatment train
Process Stage |
Recommended Technologies | Purpose |
---|---|---|
Inlet pre‑treatment | Coarse screens ➜ micro‑sand ballasted clarifiers ➜ dual‑media or walnut‑shell filters | Remove grit, oils, suspended solids to <10 ppm TSS |
High‑purity make‑up | Reverse Osmosis ➜ Electrodeionization / Mixed‑bed polish | Produce <0.1 µS cm⁻¹ water for catalysts & blending |
Boiler feed conditioning | Hot lime softening, sodium cycle softeners, oxygen scavenger dosing, deaerators | Control hardness, silica & dissolved O₂ to stop scale/corrosion |
Cooling tower loop | Side‑stream filters, automatic self‑cleaning strainers, hypochlorite or monochloramine dosing, anti‑scalants | Limit fouling, biofilm and Legionella risk while safely extending cycles of concentration |
Wastewater & reuse | Dissolved‑air‑flotation (DAF) ➜ Membrane Bioreactor (MBR) ➜ RO ➜ Evaporator / Crystallizer | Cut COD, recover 70–90 % water, minimise brine volume |
Hydrocarbon separation | Induced gas flotation, corrugated plate interceptors, API separators | Reduce free oil to <5 ppm before downstream polishing |
Condensate polishing | ANSI‑rated pre‑filters ➜ hydrogen cation exchangers ➜ resin traps | Strip iron, copper and return 95 % condensate to the boiler |
Sustainable wastewater management
Advanced oxidation processes (AOP)—e.g., UV/H₂O₂ or Fenton—destroy color and trace BTEX compounds that elude conventional biology. Where freshwater abstraction costs rise, MBR‑RO‑UV reuse loops supply up to 50 % of cooling and wash‑down demand. For remote upstream sites, modular membrane distillation plus crystalliser skids achieve ZLD with minimal operator intervention, generating solids fit for secure landfill. Sludge can be dewatered with plate‑presses and blended into refinery fuel to offset disposal costs.
Key benefits for operators
- 3–7 % energy savings from cleaner heat‑exchange surfaces.
- Up to 30 % chemical spend reduction via real‑time dosing control and on‑line silica/hardness monitoring.
- Regulatory peace of mind by meeting ISO 14001 and IFC effluent limits, vital for global lenders.
- Longer asset life thanks to lower corrosion rates (≤0.05 mm yr⁻¹ in carbon steel).
- Enhanced ESG performance through water‑recycling KPIs reported to CDP and GRI.
Actionable next steps
Audit current water balance, model quality pinch‑points with a cloud‑based simulator, and pilot the most critical unit—often RO‑EDI for high‑purity or MBR for reuse—before full‑scale rollout. Partnering with a vendor offering 24/7 digital twin monitoring further safeguards uptime.