Water for Injection (WFI) Applications
Water for Injection (WFI) is a highly purified and sterile form of water used in the production of injectable drugs and various medical applications. As one of the most critical components in pharmaceutical manufacturing, WFI must adhere to stringent pharmacopeial standards, such as those outlined by the United States Pharmacopeia (USP) and European Pharmacopoeia (EP). These standards ensure that the water is free from microbial contamination, endotoxins, and particulate matter, guaranteeing its safety and compatibility with medical products.
The production and use of WFI are tightly regulated due to its critical role in drug formulation, cleaning processes, and sterilization. WFI is used for preparing parenteral solutions, diluting active pharmaceutical ingredients (APIs), and cleaning manufacturing equipment to maintain sterility and prevent cross-contamination. Advances in water purification technologies, such as reverse osmosis, electrodeionization, and ultrafiltration, have significantly enhanced the ability to produce WFI efficiently while maintaining the highest quality standards.
Key Systems and Technologies Used in WFI Production
Reverse Osmosis (RO)
Removes dissolved salts, organic matter, and particulates as a core pre-treatment step.
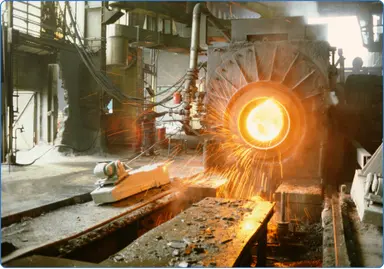
Ultrafiltration (UF)
Eliminates endotoxins, bacteria, and particulates, ensuring microbial control.
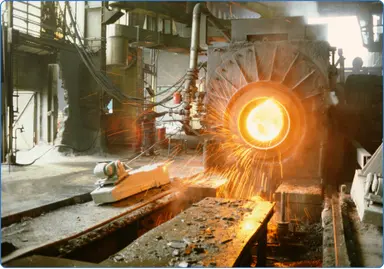
Distillation Systems
Ensure compliance with pharmacopeial standards by removing impurities through evaporation and condensation.
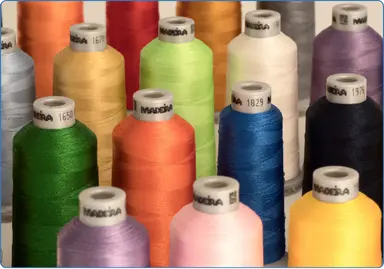
Electrodeionization
Combines ion exchange and electrical current to continuously produce ultrapure water without requiring chemical regeneration.
Applications of Water for Injection (WFI)
- Injectable Drug Production: Serves as a solvent for parenteral formulations, including vaccines, biologics, and intravenous solutions.
- Sterilization and Cleaning: Used for cleaning and sterilizing manufacturing equipment, ensuring compliance with Good Manufacturing Practices (GMP).
- Pharmaceutical Formulations: Acts as a diluent in the preparation of active pharmaceutical ingredients (APIs).
- Medical Device Manufacturing: Ensures sterility in the production of critical medical devices.
Advantages of Water for Injection (WFI)
- Ultra-Purity: Meets the strictest requirements for microbial and endotoxin levels, ensuring safety for injectable drugs.
- Regulatory Compliance: Adheres to international pharmacopeial standards, including USP, EP, and JP.
- Versatility: Suitable for a wide range of pharmaceutical and medical applications, from drug formulation to equipment cleaning.
- Operational Efficiency: Modern WFI systems are designed for continuous production, minimizing downtime and maximizing output.
- Reduced Risk: Prevents contamination and ensures product safety in critical manufacturing environments.
Challenges and Solutions in WFI Production
- Stringent Quality Requirements: Advanced purification technologies and real-time monitoring systems ensure compliance with pharmacopeial standards.
- Microbial Control: Regular system validation and the use of technologies like ultrafiltration and UV disinfection mitigate microbial risks.
- Energy Consumption: Energy-efficient systems, such as advanced distillation units and low-energy RO membranes, reduce operational costs.
- System Maintenance: Scheduled cleaning and monitoring prevent scaling, fouling, and contamination, ensuring consistent performance.
FAQs about Water for Injection (WFI)
- What are the key standards for WFI? WFI must meet pharmacopeial standards such as USP, EP, and JP, focusing on microbial limits, endotoxin levels, and purity.
- How is WFI produced? WFI is typically produced using technologies such as reverse osmosis, electrodeionization, and distillation.
- Can WFI systems operate continuously? Yes, modern WFI systems are designed for continuous production, ensuring a reliable supply for manufacturing processes.
- What is the difference between WFI and purified water? WFI has stricter purity requirements, including limits on microbial contamination and endotoxins, making it suitable for injectable drugs.
- How is microbial contamination controlled in WFI systems? Technologies like ultrafiltration, UV disinfection, and rigorous system validation are used to prevent microbial contamination.
Injection Water (WFI) and Related Processes
Definition and Areas of Application
Injection water (Water for Injection, WFI) refers to water of extremely high purity used in the preparation of injectable products. WFI is a water quality characterized by the minimal presence of impurities such as microorganisms, organic matter, and ions. In pharmaceutical manufacturing, WFI is most often used as a component or solvent and is critical for ensuring the safety of parenteral products. Although non-sterilized WFI may be used in certain production processes, solutions intended for direct patient administration are generally prepared with either subsequently sterilized or pre-sterilized WFI.
WFI is indispensable in the pharmaceutical, biotechnology, and medical applications. In the pharmaceutical industry, the use of WFI is mandatory in the preparation of intravenous injectable solutions. For example, when preparing sera, vaccines, intravenous infusion solutions, and other parenteral products, it is a legal requirement to use WFI as the solvent. In biotechnology, WFI may be used in the preparation of cell culture media, in dilution processes of biologically active substances, and during product purification steps. In medical device manufacturing, WFI is preferred for applications such as cleaning implantable medical devices, hemodialysis solutions, and hemofiltration fluids. Additionally, in hospital and clinical settings, WFI is commonly used for purposes such as reconstituting drug powders prior to injection or preparing surgical irrigation solutions. The extensive and mandatory use of WFI underscores how critical the purity standards of the water are for patient safety.
The importance of WFI is also emphasized by international health authorities. For example, the World Health Organization (WHO) has included sterile injection water in its list of essential medicines. This inclusion demonstrates that WFI is a critical resource for the healthcare system. In conclusion, WFI enables safe production and application in various areas—ranging from pharmaceutical formulation and equipment surface cleaning to the rinsing of medical devices—by minimizing contamination risks.
Production Methods
WFI production is carried out using advanced purification methods under extremely strict controls to remove all impurities from the water. Traditionally, distillation (or vaporization) is considered the most reliable method. Historically, pharmacopoeias have accepted only distillation for producing WFI. Indeed, for nearly a century, WFI has been produced using multi-stage distillation devices. The distillation process effectively removes ions, microbes, and pyrogens by boiling the water to produce vapor and then condensing it. However, in recent years, advances in membrane filtration technologies—such as reverse osmosis (RO), electrodeionization (EDI), and ultrafiltration (UF)—have made it possible to produce water of WFI quality by these methods as well. In 2017, the European Pharmacopoeia approved alternative methods capable of producing water of equivalent purity to distillation, similarly to the long-accepted practices of the United States Pharmacopoeia (USP). Thus, if properly designed and validated, WFI can also be produced by membrane-based purification systems. Below, the main methods and process steps commonly used in WFI production are explained.
Production by the Distillation Method
Distillation is based on converting raw water into pure vapor and then condensing it back to liquid form. Distillation systems designed for producing WFI are generally multi-stage (multi-effect distillation) or use vapor compression distillation. In multi-effect systems, the vapor produced in the first column is used to heat the second column, and this process is repeated through several columns, ensuring energy efficiency. In each stage, the vapor is re-condensed to produce a highly pure distillate. An example of a multi-column distillation system is shown below:
Figure 1: A multi-effect distillation system. In stainless steel columns, water is vaporized and condensed sequentially to produce WFI.
The typical steps in WFI production by distillation are as follows:
Pre-treatment
Before entering the distillation process, raw water (such as municipal water) undergoes pre-filtration and conditioning. In this stage, the water is cleared of particles through sand or cartridge filters; it is dechlorinated using activated carbon filters to remove oxidants such as chlorine, and, if necessary, softened to reduce hardness. Pre-treatment is critical to prevent scaling and excessive loading of the distillation equipment.
Distillation (Vaporization)
The pre-treated water is heated in the evaporator section of the distillation apparatus. The resulting steam leaves behind all non-volatile impurities. In multi-effect distillation, the steam is directed to successive columns where it undergoes repeated vaporization-condensation cycles. Special separators at the top of each column remove any entrained droplets or residual particles, ensuring that “dry” (endotoxin-free) vapor is obtained. When this pure vapor is re-condensed in the condenser section, WFI is produced. If the system is of the vapor compression type, the produced vapor is compressed to increase its pressure before being reused for condensation, thereby saving energy.
Storage and Distribution
The hot distillate from the distillation apparatus is usually transferred directly to a WFI storage tank. The distillation process typically produces WFI at relatively high temperatures (around 70–80°C); this high temperature helps prevent microbial contamination. The design of storage tanks and distribution lines is such that the temperature is maintained at approximately 80°C. Continuous circulation of the water ensures both a homogeneous temperature distribution and prevents stagnation in dead zones.
Advantages and Disadvantages of the Distillation Method
The advantages and disadvantages of the distillation method can be summarized as follows
Advantages of Distillation Systems
Reliable Purity: Because distillation vaporizes and re-condenses water, it effectively separates ions, microorganisms, and endotoxins. This process acts as a natural barrier that prevents pyrogenic substances from passing into the product water. The resulting distillate readily meets pharmacopeial purity criteria.
Microbial Control: Since distillation occurs at high temperatures, bacteria cannot survive during the process. Additionally, by maintaining the temperature of the distillate, the system can self-disinfect, which minimizes biofilm formation especially in continuous hot WFI cycles.
Regulatory Compliance: Distillation has long been the preferred method of regulatory authorities worldwide. Both the USP (United States) and EP (Europe) have extensive experience and guidelines for WFI produced by distillation, thereby fostering confidence during inspections.
Disadvantages of Distillation Systems
High Energy Consumption and Cost: Boiling the water and condensing the vapor require substantial energy. Distillation systems typically consume large amounts of steam or electricity, which increases operational costs. Traditional multi-effect distillation, due to its continuous heating and cooling cycles, may have significantly lower energy efficiency compared to membrane systems. In some cases, the operational cost of distillation can be up to 90% higher.
High Capital Investment and Infrastructure Requirements: The setup of a distillation system involves complex equipment such as stainless steel columns, steam generators, and condensers, necessitating a high initial investment. The associated requirements for space, piping, and insulation are also more demanding compared to membrane-based systems.
Maintenance and Operational Challenges: Distillation units require regular maintenance (for example, cleaning of heat exchanger surfaces and removal of scale deposits). Inadequate control of water hardness during pre-treatment can lead to scaling, reducing the efficiency of heat transfer in the columns. The process requires continuous balancing of steam and cooling water, demanding high operational expertise.
Production by Membrane Filtration Methods
Membrane-based production involves purifying water by mechanical/electrical separation methods without the need for boiling. By using combinations of reverse osmosis (RO), electrodeionization (EDI), and ultrafiltration (UF), it is possible to obtain water of WFI quality. The aim in membrane methods is to remove ions, organic substances, particles, and microorganisms through a series of appropriate purification steps. A typical membrane-based WFI production process consists of the following stages:
Pre-treatment
As with distillation, the raw water in membrane systems undergoes pre-treatment. Particulates are removed by filtration (using cartridge or sand filters); chlorine and organic contaminants are removed with activated carbon filters, and hardness is reduced through water softening. This step is important to prevent fouling of the membranes and to extend their lifespan.
First-Pass Reverse Osmosis (RO)
The water that has undergone pre-treatment is fed under high pressure to RO membranes. Reverse osmosis membranes allow water molecules to pass while retaining most dissolved salts, large organic molecules, and microorganisms. The permeate from the first pass RO is a low-conductivity water from which most of the total dissolved ions (approximately 98%) have been removed.
Second Purification Step (RO or EDI)
A single-pass RO is generally insufficient for achieving WFI purity; thus, a second purification step is necessary. This may involve either a second-pass RO unit or an EDI module. Second-pass RO further removes the remaining ionic contaminants, while EDI continuously deionizes the water by combining ion exchange resins with membranes under an electric current. The EDI module demineralizes the water to ultra-low conductivity levels and, through high pH gradients, helps to eliminate organic substances and bacteria. At the end of this stage, the water meets the ionic purity criteria for WFI.
Ultrafiltration (UF) (if necessary)
One of the most critical aspects of WFI production is the removal of endotoxins. Although RO membranes and EDI capture many bacteria and endotoxins, ultrafiltration may be employed as an additional safeguard. UF membranes typically have a cut-off value of around 6,000 Daltons and can filter out larger molecules such as bacteria and endotoxins. In some systems, UF is used in place of a second RO stage to provide an extra level of endotoxin removal. Ultrafiltration modules are designed to be disinfected with hot water or chemicals.
Storage and Distribution
If the water produced by the membrane system meets the required quality, it is transferred to a WFI storage tank. The WFI produced by membranes usually exits at ambient temperature (cold WFI). Therefore, regular disinfection of the storage and distribution system is critical to prevent microbial growth. Modern membrane WFI systems are designed to prevent biofilm formation by periodic hot water sanitization (for example, circulating water at 80–85°C) or using ozone/UV disinfection. When storing cold WFI, the tank air is protected with a 0.2 µm hydrophobic air filter and, if necessary, methods such as ozonation within the tank are applied to suppress microbial growth.
Advantages and Disadvantages of Membrane Filtration
Advantages of Membrane Filtration
Energy and Cost Savings: Since membrane processes do not require phase change (evaporation), they consume much less energy. Compared to distillation, membrane systems can provide up to 90% savings in operating costs and reduce capital investment by as much as 70%. This makes the use of RO/EDI systems economically attractive for facilities requiring large volumes of water.
Smaller Footprint: Membrane systems can often be designed as compact, packaged units. A skid-mounted RO+EDI+UF system occupies less space and offers more flexibility in plant layout compared to an equivalent multi-effect distillation unit. Additionally, these systems have a shorter commissioning time and, due to their modular design, capacity expansion or relocation is easier.
Suitability for On-Demand Use: Membrane systems can adapt more quickly to start-stop operations and variable production rates because they do not require extended heating periods. This allows for rapid start-up and shutdown of water production, enhancing operational efficiency, especially in facilities with intermittent production.
Less Waste and Water Consumption: Well-designed membrane systems may achieve high recovery rates. While distillation typically incurs losses through boiler blowdown and cooling water, dual-stage RO/EDI systems convert most of the feed water into product water, resulting in less concentrated waste. This is beneficial from a sustainability perspective.
Disadvantages of Membrane Filtration
Risk of Microbial Contamination: The greatest challenge for membrane systems is their susceptibility to microbial growth. RO/EDI units operating at ambient temperatures can foster biofilm formation if not regularly sanitized. Moreover, the inner surfaces of RO membranes are typically not of a “sanitary” design and their grooved structure may allow bacteria to adhere and multiply. Therefore, strict microbial control is necessary in membrane systems through the use of UV lamps, regular hot water/chemical sanitization, and continuous monitoring.
Membrane Failures and Safety: RO membranes and EDI units may develop leaks due to physical damage or wear. Particularly in RO systems, a compromise in membrane integrity can allow contaminants from the raw water side to pass into the product water. To mitigate these risks, systems are equipped with dual-stage membranes, integrity tests (e.g., pressure holding tests for UF modules), and continuous quality monitoring devices.
Validation and Regulatory Process: Historically, European authorities have been cautious with membrane methods for WFI production, traditionally permitting only distillation. Although the European Pharmacopoeia has been revised to include membrane systems, companies are required to thoroughly validate that these systems are as safe as distillation. Regulatory bodies such as the FDA/EMA place great emphasis on microbial control plans and continuous monitoring data, which leads to more extensive documentation and inspection requirements for membrane systems.
Maintenance and Consumable Costs: Membranes require periodic chemical cleaning (CIP) and regular replacement. For instance, if chlorine breakthrough occurs, RO membranes may be damaged; hence, the activated carbon filter in the pre-treatment step must be replaced regularly. EDI units are sensitive, and fluctuations in feed water quality may impair their performance. Consequently, the maintenance costs for membrane systems manifest as regular membrane/filter replacements, in contrast to the boiler maintenance required for distillation.
Parameters to be Monitored
During the production and use of WFI, various quality control parameters are monitored to ensure that the water maintains the required standards. The pharmacopeial definitions specify these parameters and acceptance criteria to guarantee the safety and purity of the product. The key parameters include:
Conductivity
The electrical conductivity of water indicates the level of ionic impurities present. Theoretically, ultra-pure water has extremely low conductivity (approximately 0.055 µS/cm at 25°C for completely pure H₂O). According to pharmacopeial criteria, the conductivity of WFI should not exceed 1.3 µS/cm at 25°C. The European Pharmacopoeia specifies a maximum value of around 1.1 µS/cm at 20°C, which is considered equivalent to the USP standard. Conductivity is usually measured continuously using online sensors. A rising conductivity value may indicate the intrusion of an ionic contaminant or saturation of the ion-exchange resins in the system. For example, a sudden increase in conductivity in a membrane system could suggest decreased RO/EDI performance or a leak mixing raw water with the product water. In such cases, the relevant equipment is inspected and, if necessary, the system is shut down for maintenance.
Total Organic Carbon (TOC)
TOC represents the total amount of dissolved organic substances in the water, expressed in terms of carbon content. Organic contaminants (for example, microbial metabolites, organics from biofilm, or organic impurities from the source water) are not desired in WFI because they may promote microbial growth or compromise the purity of the product. Both the USP and EP require that the TOC level in WFI should not exceed 0.5 mg/L (500 ppb). TOC is typically measured either continuously or periodically using online analyzers that detect the organic content of the water through oxidation and spectrophotometric methods. An increase in TOC is an indication of organic contamination. For instance, if a plastic component in the system begins to degrade, it may leach organics, or ineffective filters may fail to remove them. In such cases, the water production is halted, the cause is investigated, and measures such as chemical cleaning of tanks and pipelines are implemented.
Microbial Load (Bioburden)
The microbiological quality of WFI is critical as it directly impacts patient safety. Pharmacopoeias specify limits for viable microorganisms in injection water. Generally, it is accepted that the total aerobic bacterial count in a 100 mL sample of WFI should be less than 10 colony forming units (CFU). In a 100 mL sample, a maximum of <10 CFU may be present. In a well-operated WFI system, this value is typically 0 or undetectable. Furthermore, pharmacopeial tests require that pathogenic microorganisms such as E. coli, Salmonella, Pseudomonas aeruginosa, and Staphylococcus aureus must be absent in WFI. Microbiological control is usually performed daily or at specified intervals by taking samples and culturing them on petri dishes. The results are then evaluated by counting the colonies after incubation. If any sample exceeds the limits or if pathogens are detected, it constitutes an alarm situation. In such cases, the water system is immediately shut down, a root cause analysis is performed (to determine whether the issue is due to a valve contamination, a filter malfunction, insufficient ventilation of the storage tank, etc.), corrective measures such as comprehensive sanitization (using hot water or chemical disinfection) are implemented, and production water is not used until subsequent tests confirm compliance with the water quality standards.
Bacterial Endotoxin (Pyrogen) Levels
Endotoxins are toxic substances released from the cell walls of Gram-negative bacteria that can cause febrile reactions in humans. The endotoxin content of WFI must be below 0.25 Endotoxin Units (EU/mL). This criterion implies that WFI should practically be non-pyrogenic. Endotoxin testing is conducted in the laboratory using the LAL (Limulus Amebocyte Lysate) test. If endotoxin levels exceed the limit (for example, rising above 0.25 EU/mL), it indicates a probable bacterial contamination in the system—even if live bacteria are not present, the remnants of dead bacteria can accumulate as endotoxins. In such cases, the water system is immediately reviewed, and if necessary, the entire system is sterilized with hot water steam followed by retesting.
Other Physico-Chemical Parameters
In addition to the above key parameters, pharmacopeial monographs include other purity tests for WFI. For example, appearance tests (the water should be colorless, clear, and free of particulates), pH (typically between 5.0 and 7.0, though this test is carried out under specific conditions since pure water is non-buffered), heavy metals (<0.1 ppm), and limits for specific ions (such as chloride, ammonium, calcium, and magnesium) are among the acceptance criteria. These tests are usually verified by periodic laboratory analyses. In modern practice, measurements of conductivity and TOC largely substitute for these ionic and organic purity tests; if a WFI sample shows low conductivity and low TOC, it is assumed that heavy metals, chloride, etc., are already below the specified limits. Nevertheless, for quality assurance purposes, these additional parameters are confirmed periodically through laboratory analyses.
Interpretation of Results and Actions
Data obtained from WFI quality control are continuously evaluated using trend analysis. For example, a gradual increase in conductivity or TOC may indicate an impending system malfunction and trigger proactive maintenance. Microbiological test results are typically evaluated as a “pass/fail” criterion, and even the slightest non-compliance generally leads to shutting down the water system and initiating a comprehensive re-sanitization and validation process before the production water can be used again. The monitoring of each parameter together guarantees the chemical and microbiological integrity of the water. A well-managed WFI system employs alarmed automated monitoring systems; if conductivity or TOC exceed preset limits, an automatic alert is generated so that operators can intervene immediately. In general, the guiding principle in operating a WFI system is “prevent contamination from entering, detect it if it does, and block it from reaching the product.”
Industrial Applications
WFI, thanks to its purity and reliability, forms the basis for critical processes in many industries. The primary applications and purposes are as follows:
Pharmaceutical Production
In the pharmaceutical industry, WFI is used as a solvent particularly in the formulation of parenteral products (those administered via injection). During the preparation of sterile preparations such as injectable solutions, sera, vaccines, intravenous infusion fluids, and eye drops, active and auxiliary substances are dissolved in WFI. For instance, when reconstituting an antibiotic powder prior to injection or diluting a chemotherapy drug in a saline solution, the water used must be of WFI quality. The use of WFI ensures that these products can be safely administered to patients. Additionally, in the production of pharmaceutical raw materials (API production), WFI is preferred in final stages such as crystallization, washing, or dilution to prevent unwanted ionic or microbial residues in the product.
Aseptic and Biotechnological Processes
Many products produced in the biotechnology sector (monoclonal antibodies, protein biopharmaceuticals, vaccines, etc.) are administered parenterally. Consequently, WFI is vital in biotechnological production processes as well. Pure water is commonly used in the preparation of cell culture media; when the final product is intended for injection into humans, even the preparation of the medium may favor the use of WFI. In downstream purification processes, buffers and chromatography elution fluids are prepared with WFI to prevent an increase in contamination risk during the process. Moreover, in the cleaning of equipment such as fermenters or bioreactors, WFI is used to wash away residual microorganisms and to prevent endotoxin buildup. In the production of lyophilized products (freeze-dried products), the water added to the product must be WFI because any residual ions post-drying could affect product stability.
Equipment Cleaning and Sterilization
In both traditional pharmaceutical manufacturing and biotechnology, cleaning production equipment is a critical step. Equipment surfaces that come into contact with the product—such as bioreactors, mixing tanks, pipelines, and filling machines—are rinsed with WFI after processing or product changeover. The absence of ions and microorganisms in WFI ensures that no residues or biological loads remain on equipment surfaces after cleaning. The use of WFI is common during the final rinsing step in Clean-In-Place (CIP) systems. Similarly, materials to be autoclaved (bottles, caps, utensils) are rinsed with WFI to remove any chemical residues before sterilization, preventing the residues from decomposing and contaminating the products during sterilization.
Medical Devices and Healthcare
WFI is not only used in pharmaceuticals but also in medical devices and hospital applications. For example, before implantation, medical devices or surgical instruments are rinsed with WFI to ensure that no pyrogenic residues remain. In the preparation of dialysis solutions or the production of hemofiltration fluids, the use of WFI is essential. In hospitals, sterile WFI ampoules are used to reconstitute drug powders (such as injectable antibiotic vials) immediately prior to use. Eye and tissue irrigation solutions are also prepared with WFI. In all these examples, the high purity of WFI aims to eliminate the risk of toxic or infectious reactions in the final product administered to the patient.
Analytical and Research Purposes
WFI is also the preferred solvent for sensitive analyses or experiments in laboratory settings. For instance, in pharmaceutical quality control laboratories, preparing reference solutions and reagents with WFI increases the reliability of analytical results. In biological research, particularly in in vitro experiments sensitive to endotoxins (such as primary cell cultures or preparations for LAL tests), the use of WFI prevents misleading results. Although the high cost of WFI production sometimes leads laboratories to use “ultrapure” water from high-purity water systems, WFI is still preferred for the most critical biological tests.
In summary, WFI plays a “safety water” role in many fields ranging from pharmaceuticals to biotechnology, from medical devices to clinical applications. Its presence ensures the reliability of products and treatments, while its absence may pose serious risks. For this reason, in industry WFI is not only considered a raw material but also a quality standard.
Design and Application Criteria
The design of WFI systems must adhere to hygienic engineering principles that safeguard product quality. When planning a WFI production, storage, and distribution system, the primary criteria to consider include:
Material Selection and Surface Characteristics
All surfaces in contact with WFI must be made of highly corrosion-resistant and inert materials. AISI 316L stainless steel is typically preferred. Due to its low carbon content, 316L is resistant to sensitization after welding and is durable against chloride-induced corrosion. Surface finish is crucial: smooth interior surfaces hinder bacterial adhesion. For this reason, the inner surfaces of WFI pipes and tanks are typically electropolished to achieve a surface roughness of Ra ≤ 0.5 microns. High-quality stainless steel also minimizes oxidation issues known as “rouging.” Seals, gaskets, and similar components used in piping should be made of Teflon or silicone and conform to USP Class VI food/medical standards to ensure that no soluble substances leach into the water.
Design of the Storage Tank
WFI is generally produced continuously and stored in a buffer tank. In the design of these tanks, ensuring sterile barriers and preventing water stagnation are key factors. Although the tank typically operates at atmospheric pressure, it is fitted with a 0.22 µm hydrophobic air filter at the top to sterilize the incoming air and prevent microbial ingress from the external environment. WFI tanks are often double-walled or equipped with a heating jacket to maintain the required water temperature. In hot WFI systems, the tank water is continuously kept at around 80°C, which is crucial for preventing biofilm formation. Temperature control inside the tank is achieved using a PID control system connected to the steam jacket. Additionally, to avoid dead zones inside the tank, a spray-ball is installed so that the returning hot WFI continuously wets the inner surfaces. This design is critical to ensuring that no point inside the tank allows microbial growth. The bottom of the tank should be conical with a drain outlet to ensure complete drainage.
Distribution (Circulation) System
The distribution line that transfers water from the WFI production tank to the points of use is generally designed as a closed-loop system. A circulation pump continuously circulates the water in this loop, ensuring that the water does not become stale and maintains the desired quality at all times. Distribution pipes should be as short and uninterrupted as possible, with welded joints made using orbital welding to prevent the formation of burrs or crevices. When designing the piping route, a slope (typically around 1:100, meaning a 1% gradient) is provided to allow complete drainage from low points. This facilitates the removal of water during cleaning or maintenance. In addition, by adjusting the flow direction and the position of valves, hydraulic balance is maintained so that every point of use receives a consistent flow. Flow velocity is one of the critical parameters: a target linear velocity of approximately 1.5 m/s (5 ft/s) is typically maintained in the pipes. This velocity creates turbulence that discourages biofilm formation and supports uniform temperature distribution. The flow velocity in the return line is maintained at least at around 1 m/s so that the water is always in motion.
Prevention of Dead Volumes and Dead Legs
In loop designs for WFI, it is vital to avoid “dead legs” or protruding sections of pipe where the flow is stagnant. The general industry standard is that any pipe section branching from the main line (such as for a sample port or measurement probe) should not exceed 6 times the inner diameter (6D rule). For example, if the main line has a diameter of 2 cm, the dead leg should not exceed 12 cm. This rule minimizes the risk of bacterial proliferation in stagnant areas. Zero-dead-volume valves (zero-dead-leg diaphragm valves) are preferred for points of use because their design prevents any stagnant pocket from forming at the valve inlet, even when closed. Additionally, all accessories such as sensor ports and sampling points are positioned to create minimal dead volume without disturbing the flow. When the system is shut down or not in use for extended periods, it should be possible to completely drain and dry the entire circuit; therefore, drain valves are installed at the lowest points.
Pump and Valve Selection
The circulation pump should be a hygienically designed centrifugal pump made of stainless steel. Its mechanical seals must be chosen so as not to introduce contaminants into the water; in some systems, magnetically coupled pumps are used to eliminate the risk of contamination from seal lubricants such as grease. Valves at the points of use are typically hygienic diaphragm valves, consisting of a PTFE/Teflon diaphragm and a stainless steel body. These valves are easy to clean using CIP and do not create dead volumes. All valves and connection components must be resistant to sterilization, as gaskets should not melt when exposed to periodic hot water or steam. When necessary, automatic (pneumatic or electric) valves may be used so that the system can be controlled remotely during CIP/SIP processes.
Heating/Cooling and Temperature Control
If the system is designed as a hot WFI system, a heating arrangement must be in place to maintain the water at around 80°C in both the storage tank and the distribution loop. While steam is supplied to the tank jacket, pipes in the loop are insulated or heat-traced to prevent cooling. Alternatively, the water from the storage tank may be circulated through a heat exchanger to maintain a temperature of around 80°C. At the point of use, if the water is too hot, a small point-of-use heat exchanger (usually double-pipe or plate type and sterile) can be employed to cool it immediately. In cold WFI systems, instead of keeping the water continuously hot, periodic sanitization is performed; for example, the loop water may be heated to 80–85°C for 1 hour once a day and then cooled down. This is a design choice, and the equipment (such as membranes and seals) is selected to withstand the required temperatures. Whether the system is hot or cold, temperature sensors, conductivity sensors, and flow meters are strategically placed along the WFI distribution lines and connected to a central PLC/SCADA system. This enables real-time monitoring and control of the water’s parameters.
Automation and Monitoring
Modern WFI systems operate fully automatically. Tank level control, pump speed control, and temperature and pressure regulation are programmed through a PLC. For instance, the system may switch to production mode when the tank level is low and stop distillation or purification once it is full. Loop pressure and flow are continuously measured; if a point-of-use valve is opened, the pump frequency is increased to compensate for the pressure drop, and so on. Furthermore, online conductivity and TOC analyzers continuously monitor water quality, generating alarms if any parameter exceeds its threshold. Such automation minimizes human error and ensures consistent quality. All critical data are recorded and archived in compliance with data integrity requirements (such as 21 CFR Part 11).
Design for Cleaning and Sterilization
A WFI system must be capable of being sterilized when not in use or at routine intervals. For this purpose, the design incorporates SIP (Steam-in-Place) points. Saturated steam from a clean steam generator is supplied to the storage tank and distribution line to sterilize the entire system at 121°C. Alternatively, pasteurization with hot water at 80–90°C is a common method. Some systems are even designed to be cleaned with chemical sanitization (for example, by circulating ozone or peracetic acid). The important aspect is that the system is designed so that these cleaning procedures can be easily performed (for example, all components must withstand the required temperatures and appropriate connection points must be provided), and that the system can be easily rinsed and returned to service afterward. As air pockets may be present in storage tanks and long pipelines, appropriate venting and condensate drainage points are provided in the design.
In summary, the design of a WFI system represents the intersection of hygienic design principles and engineering. A well-designed system minimizes dead volumes, employs appropriate materials, ensures robust automation, and is capable of being cleaned and reliably providing water. This way, WFI functions not as a risk factor in production processes but rather as a guarantee of safety.
Possible Problems and Proposed Solutions
Even the best-designed and operated systems may encounter issues from time to time. The potential problems encountered in WFI systems and the corresponding solution strategies can be summarized as follows:
Risk of Microbial Contamination
The greatest enemy of WFI systems is unwanted microbial growth. Stagnant water regions or insufficient sanitization can lead to the formation of bacterial colonies. This not only increases the microbiological load of the water but also raises endotoxin levels as bacteria die and release endotoxins. As a solution, minimizing dead volumes during the design phase (for example, by applying the 6D rule) is the first step. In the operational phase, regular hot water sanitization or steam sterilization should be carried out. For example, circulating the system at 80°C for 2 hours every weekend prevents most biofilm formation. In cold systems, continuous low-dose ozonation may be applied with subsequent neutralization of residual ozone using UV light before the water is used. In addition, it is recommended to open all valves and drain stagnant water (“flush”) periodically to prevent accumulation. Although it is impossible to completely eliminate the risk of microbial contamination, continuous monitoring (routine sampling and rapid microbiological tests) enables early detection and intervention. If a contamination event is detected, the first actions should be a comprehensive SIP (steam sterilization) of the system, replacement of the relevant filters, identification and correction of the contamination source (for example, a faulty seal or an accidentally left open valve). Production water must not be used until the water returns to specification.
Endotoxin Accumulation
Closely related to the previous point, there are situations where endotoxin levels may be elevated even though microbiological tests indicate clean water. This is typically due to biofilm formation or remnants of dead bacteria that have adhered to the system. For example, if sanitization was inadequate for a period, bacterial biofilm may have formed inside pipes and, after the bacteria die, lipopolysaccharide (LPS) endotoxins remain. These endotoxins may not be detected by standard culture tests but are revealed by the LAL test. The best approach to preventing endotoxin issues is to prevent microbial growth from the outset. Additionally, periodic “deep cleaning” of the system using high pH hot detergents followed by low pH acid circulation can chemically break down biofilm and endotoxins. Some facilities take the WFI system offline once a year for such chemical cleaning and then rinse with pure water. If the endotoxin limit is exceeded, a short-term solution may be to pass the water through an additional line with activated carbon and ultrafiltration to remove endotoxins; however, the fundamental solution is complete system sterilization and, if necessary, replacement of affected components (such as a pipe section with entrenched biofilm).
Equipment Failures and Leaks
WFI systems consist of various equipment such as pumps, heat exchangers, sensors, and valves. Over time, these components may experience failures. For instance, if the pump’s mechanical seal wears out, lubricant leakage may contaminate the water, or if a crack develops in a heat exchanger, steam or hot water from the heating side may mix with the product water. Such failures can lead to the introduction of foreign substances into the water. Therefore, periodic maintenance is essential: pump seals should be replaced after a specified period of operation, heat exchangers should undergo routine pressure testing, and sensor calibrations should be performed every six months. Moreover, some components are proactively replaced before reaching the end of their life (for example, the elastomeric diaphragms in diaphragm valves may be replaced annually). Employing redundant critical equipment, such as having twin pumps (one as a backup), enhances system reliability; in the event of a failure, the system can continue to operate without interruption. Drip pans and leak-detection sensors are installed at locations prone to leakage, ensuring that any leakage triggers an alarm.
Control System and Monitoring Issues
While automation is beneficial, faulty sensor readings or PLC malfunctions can lead to misleading information. For example, if a conductivity probe becomes fouled, it might falsely indicate high conductivity in otherwise pure water. In such cases, operators might unnecessarily panic or, conversely, a faulty sensor reading low might mask actual contamination. Therefore, regular calibration of sensors is essential, and critical parameters should be cross-checked with multiple sensors (for example, using two conductivity sensors in both the storage and return loops). In case of a software error in the PLC/SCADA system, critical valves and pumps should be operable in manual mode as a backup. Additionally, an uninterruptible power supply (UPS) and data backup systems should be implemented to ensure continuous data recording. Operators should also be trained on the appropriate procedures in case of alarm situations; for instance, if a conductivity alarm occurs, a sample should be taken immediately for laboratory testing to verify the sensor reading.
Corrosion and Material Issues
Paradoxically, because WFI is so pure, it can dissolve the protective oxide layer on stainless steel, an effect known as “rouging.” Rouging can result in a slight reddish discoloration on the system and, in the long term, may cause particulate contamination, albeit less severe than endotoxins. To prevent this, stainless steel surfaces must be properly passivated (using acid passivation after manufacturing and maintenance). If rouging is observed (for example, orange deposits on filters), the system should be shut down as planned and cleaned with chemicals such as citric acid before being passivated again. Furthermore, the use of different metals or alloys together (which could lead to galvanic corrosion) must be avoided; the design should favor the use of a single material type (316L SS) as much as possible. In cases where components such as seals or certain measurement devices are made from different materials, tests must be conducted to ensure that no extractables leach into the water.
Degradation during Storage and Transport
WFI is typically consumed at the production site, but in some cases it may need to be transported by tanker to another facility or packaged (as sterile ampoules or vials) for distribution. Bulk WFI is at high risk during transport because circulation and temperature control within a tanker are limited. If tanker transport is necessary, the tanker must be pre-cleaned and sterilized, maintained at 70–80°C if possible, and unloaded immediately upon arrival. The transport duration should be kept as short as possible. The tanker’s air space should also be filtered with a 0.2 µm filter, and in some cases, the application of an inert gas (such as nitrogen) is practiced. Packaged sterile WFI, on the other hand, is usually autoclaved or aseptically filled after production. These products should be used quickly after opening because once opened, exposure to the environment can lead to rapid microbial growth. In terms of storage, if WFI is held in a tank for an extended period after production, methods such as keeping it hot and continuously circulating it—or even ozonation—are applied. Some facilities inject low concentrations of ozone into the WFI loop during off-peak hours and then neutralize the ozone with UV light in the morning so that the water remains free of microbes even when not in use.
Maintenance and Validation Processes
WFI systems are considered critical equipment under GMP (Good Manufacturing Practice) and must be qualified/validated regularly. This is performed both during the initial setup (IQ, OQ, PQ – Installation/Operational/Performance Qualification) and as part of an annual re-validation process. Validation involves taking samples on consecutive days to confirm that all critical parameters (conductivity, TOC, microbial load, endotoxins) meet the specifications. Additionally, various challenge tests are performed—for example, taking samples from the most remote point of use to check for microbial growth or sampling the water 24 hours after system shutdown to ensure no degradation occurs. If these tests are successful, the system remains approved. In terms of maintenance, after every maintenance activity (such as a membrane or seal replacement), a brief re-qualification is conducted to demonstrate that water quality has not been affected. Maintenance should be performed by trained personnel in accordance with the procedures because even a minor error in a sterile system (for example, an improperly installed seal) can lead to significant contamination. Critical spare parts should be stocked so that the system does not remain offline for an extended period in case of failure. Finally, every problem should be treated as a deviation and subjected to a root cause analysis and corrective/preventive action (CAPA) process. This approach is essential for preventing recurrence and continuously improving the system.
In summary, it is practically impossible to reduce the problems in WFI systems to zero; however, through proactive maintenance, stringent monitoring, and appropriate engineering practices, risks can be managed at acceptable levels. WFI systems should be regarded as living organisms that require regular attention and maintenance. In the event of an unexpected issue, rapid diagnosis and proper intervention ensure that product quality is not compromised and that processes continue smoothly.
International Standards and Regulations
The production and quality of injection water are strictly bound by international pharmacopoeias and regulatory bodies. The primary references include the United States Pharmacopoeia (USP), the European Pharmacopoeia (EP), the Japanese Pharmacopoeia (JP), as well as guidelines from authorities such as the FDA, EMA, and recommendations from organizations like the WHO. The overall objective of these standards is to ensure that regardless of the production method, WFI always meets a minimum safety threshold globally.
Harmonization among Pharmacopoeias
The major pharmacopoeias—USP, EP, and JP—have largely harmonized their WFI standards. All three specify identical chemical purity criteria (conductivity ≤1.3 µS/cm @25°C, TOC ≤0.5 mg/L) and microbiological criteria (≤10 CFU/100 mL, endotoxins <0.25 EU/mL) for WFI. For example, the USP’s <1231> section and the relevant monograph indicate that WFI is subject to stricter microbiological limits than purified water and specify the endotoxin limit. The EP, in its “Aqua ad iniectabilia” monograph, similarly requires that WFI must pass the endotoxin test. In the past, the primary difference pertained to production methods: while the USP has long accepted methods “equivalent to distillation” for WFI production, the EP traditionally mandated distillation only. As of 2017, however, the EP monograph was revised to state that alternative methods producing water of equivalent purity to distillation via membrane technologies may also be used for WFI. This change marked an important step toward global harmonization, and other pharmacopoeias such as the Japanese Pharmacopoeia have followed suit. However, some regional standards—such as the Chinese Pharmacopoeia (as of 2017)—may still permit only distillation. Consequently, multinational companies must also consider the specific requirements of the markets to which they intend to sell their products.
USP (United States Pharmacopoeia)
The USP defines WFI as a subclass of purified water and stipulates that it need not be sterile but must exhibit very low bioburden. The USP details online conductivity test limits and laboratory TOC test procedures for WFI. Furthermore, the USP <1231> Water for Pharmaceutical Purposes guide document outlines good practices for the design, operation, and validation of WFI systems. The USP also acknowledges alternative production methods (equivalent or superior to distillation, such as dual-pass RO+UF) under certain conditions. In the United States, inspections are generally conducted by the FDA, which also references pharmaceutical water in sections such as 21 CFR 211.67, 211.84, and 211.94 (for instance, regarding the appropriate use of water in equipment cleaning). The FDA has also published guidance documents like the "Guide to Inspections of High Purity Water Systems" that share their perspective on WFI systems. In summary, compliance with USP standards and FDA expectations is essential for the US market.
EP (European Pharmacopoeia) and EMA
The EP defines WFI similarly; it previously also defined an intermediate category known as “Highly Purified Water (HPW).” HPW referred to water produced by non-distillation methods that were chemically of WFI quality but slightly more lenient in terms of endotoxin levels. With the 2017 revision incorporating membrane methods into the WFI monograph, the need for an HPW definition has diminished, effectively uniting the quality parameters of USP and EP under a single WFI standard. Following the EP revision, the European Medicines Agency (EMA) published a Q&A document explaining the new situation. The EMA emphasized the risk of microbial proliferation in membrane systems and expects companies to manage these risks with robust measures. The European Union GMP guidelines (EudraLex Volume 4, Annex 1 and 2) require that water used in sterile products be WFI and also indicate the necessity of using WFI in equipment cleaning validation. In Europe, national regulatory authorities (such as BfArM in Germany or ANSM in France) conduct inspections in line with EP and EMA guidelines. Companies planning to set up WFI production facilities must evaluate both the local water quality (for example, municipal water characteristics) and EP requirements to choose an appropriate system.
JP (Japanese Pharmacopoeia)
The JP is fully harmonized with the USP/EP standards on WFI. In fact, following the changes in the EP in 2017, the Japanese Ministry of Health permitted membrane methods for WFI production. The JP even provides specific application examples, such as water used as a solvent in diabetic injections. Microbiological limits and the endotoxin limit are identical to those of the USP. The Japanese inspection system requires manufacturers to continuously monitor and document water quality before each use. Moreover, Japan—being an early adopter of electronic record-keeping—closely scrutinizes the automation data of WFI systems during inspections.
WHO and Other Standards
The World Health Organization, in its International Pharmacopoeia, provides similar definitions for WFI. The WHO also publishes guidance documents for developing countries. For example, the WHO Technical Report Series 970, Annex 2, includes guidelines for “Pharmaceutical Water.” This document states that WFI should preferably be produced by distillation, but alternative methods may be acceptable if properly validated. The WHO emphasizes that even in resource-limited settings, the WFI standard for parenteral production is non-negotiable. Additionally, the FDA, EMA, and PIC/S (Pharmaceutical Inspection Co-operation Scheme) members share a common approach in inspecting water systems. PIC/S guidelines, widely recognized internationally, serve as a reference for the validation and operation of WFI systems.
Regulatory Compliance and Requirements
Facilities that produce and use WFI must comply with the GMP requirements of the relevant market. In practice, this entails the following:
Documentation: Complete quality records related to the WFI system (design approval, IQ/OQ/PQ protocols, daily monitoring logs, deviation reports, trend analyses) must be maintained.
Continuity: Compliance must be maintained not only during installation but throughout daily operations, which requires continuous monitoring and regular testing programs.
Qualification/Validation: In addition to the IQ/OQ/PQ processes, any changes to the WFI system (equipment changes, procedural modifications, etc.) must be subjected to a risk analysis and re-qualification process via change control.
Personnel Training and Awareness: Operators and maintenance personnel working with WFI must be fully aware of both the criticality of the water and the workings of the system. In GMP training, the specific role of WFI systems is emphasized since even a minor error (for example, leaving a valve open by mistake or improper sampling) can compromise water quality.
Staying Up-to-Date: Pharmacopoeial monographs may be revised periodically. For instance, the USP might update methodologies for TOC and conductivity tests, or the EP may introduce new limits. Companies must track these changes and update their internal procedures accordingly. Similarly, as technology advances (for example, with online microbiological monitoring systems), companies should adopt these innovations as opportunities permit.
Preparation for Inspections: When the FDA or local authorities inspect the facility, the WFI system is typically scrutinized. Inspectors examine validation reports, daily trend data, alarm histories, and maintenance records in detail. Therefore, it is essential to always maintain a well-organized system and records that are inspection-ready.
In conclusion, international standards provide a common safety margin for WFI: regardless of the production method, WFI must meet the specified chemical and microbiological criteria and be produced in accordance with GMP principles. These standards set the minimum requirements aimed at protecting patient safety worldwide, and it is the responsibility of industry professionals to implement and sustain these requirements in their operations.