Boiler Feed Water Treatment
Boiler feed water treatment is essential for maintaining safe, efficient, and long-lasting boiler operations across various industries. The quality of water used in boilers directly affects equipment performance, energy consumption, and overall operational costs. Without proper treatment, impurities such as dissolved solids, gases, and suspended particles can accumulate within the boiler system, leading to issues like scaling, corrosion, and decreased thermal efficiency. As a result, facilities may experience frequent breakdowns, higher maintenance expenses, and reduced production output.
In order to mitigate these problems, specialized processes are employed to remove or reduce harmful contaminants. Common methods include reverse osmosis (RO), ultrafiltration (UF), ion exchange softening, and chemical dosing to balance pH levels and control dissolved oxygen content. Each solution is tailored to the specific water source and the operational requirements of the facility. By incorporating a robust boiler feed water treatment strategy, businesses can achieve consistent steam production, prolong equipment lifespan, and improve cost-effectiveness. In this section, we will explore the key aspects and benefits of reliable boiler feed water treatment solutions.
Related Products for Boiler Feed Water Treatment
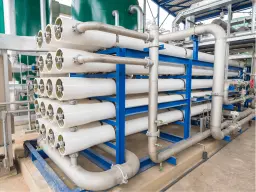
Reverse Osmosis
Uses semipermeable membranes to remove dissolved impurities, ensuring high-purity water for boiler feed.
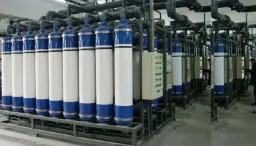
Ultrafiltration
Removes suspended solids and colloids as a pretreatment step, enhancing downstream performance.
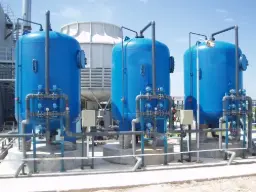
Water Softener
Exchanges calcium and magnesium with sodium, significantly reducing scale buildup in boilers.
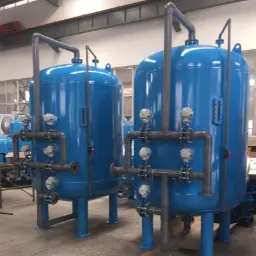
Deionization
Employs ion exchange resins to produce nearly pure water, minimizing damaging contaminants.
The Importance of Boiler Feed Water Quality
Boiler systems rely on high-quality feed water to operate effectively, minimize operational costs, and ensure extended equipment life. When impurities such as hardness minerals, dissolved gases, and suspended solids enter the boiler, they cause issues like corrosion and scale buildup, leading to energy inefficiency and frequent maintenance. Implementing a robust water treatment regimen not only safeguards against these problems but also maximizes productivity by reducing downtime. In this section, we explore the key reasons boiler feed water quality matters and the main parameters that warrant close monitoring.
Why Water Quality Matters
Proper boiler feed water quality is crucial for maintaining system performance, extending equipment lifespan, and reducing energy consumption. Contaminants such as hardness minerals, dissolved gases, and suspended solids can compromise efficiency, leading to increased operational expenses and unplanned maintenance.
Key Parameters to Monitor
Operators should regularly check water hardness, pH level, alkalinity, conductivity, and dissolved oxygen. These parameters directly influence corrosion potential and scale formation, impacting steam production quality. Keeping them within recommended ranges helps ensure reliable, uninterrupted operation.
Corrosion and Scale Formation
Insufficiently treated water promotes corrosion, eroding internal boiler surfaces and shortening equipment life. Furthermore, scale buildup acts as an insulator, raising energy demands and lowering heat transfer rates. Effective treatment strategies remove or neutralize these harmful elements before they reach the boiler.
Ensuring Long-Term Efficiency
Adopting advanced treatment technologies—such as reverse osmosis, ultrafiltration, and chemical dosing—keeps critical water parameters in check. As a result, boilers run more efficiently, experience fewer shutdowns, and comply with industry standards. By investing in high-quality feed water management, facilities can maintain consistent steam production, enhance overall safety, and reduce operating costs in the long run.
Which Parameters Are Controlled?
Monitoring and managing key water parameters is crucial for preventing corrosion, scaling, and other issues that compromise boiler system efficiency. By controlling these values, operators can maintain consistent steam production, lower energy consumption, and extend equipment lifespan.
Hardness and pH
Excessive calcium and magnesium (hardness) lead to scale formation, while improper pH levels accelerate corrosion. Maintaining an optimal balance ensures that boiler surfaces remain free from deposits and that metal components are protected against acidic or highly alkaline conditions.
Conductivity and Total Dissolved Solids (TDS)
High conductivity readings indicate a high concentration of dissolved solids, which can reduce heat transfer efficiency and cause scaling. TDS levels must be monitored and controlled, often through blowdown or specialized filtration, to keep the system operating at peak performance.
Dissolved Gases (Oxygen, Carbon Dioxide)
Oxygen and carbon dioxide can rapidly corrode internal boiler surfaces. Deaerators and chemical treatments help remove or neutralize these gases, preventing damage and boosting system reliability.
Selection Criteria
Choosing the right boiler feed water treatment solution depends on multiple factors, from the source and quality of the incoming water to the specific operational needs of the facility. Weighing these criteria carefully ensures both cost-effectiveness and robust system performance.
Water Source
The nature of the water supply—municipal, well, or surface water—dictates the presence of contaminants and influences the required treatment technologies, such as reverse osmosis or ion exchange.
Flow Rate & Pressure Requirements
High-volume operations may require more advanced or modular systems to accommodate larger flows without compromising treatment efficiency. Pressure needs also impact equipment selection and overall system design.
Budget & Lifecycle Costs
Initial investment, maintenance expenses, and chemical usage should all factor into the total cost of ownership. Opting for durable, efficient technology can minimize long-term expenditures and support continual productivity.
System Installation & Maintenance
A well-planned installation and diligent maintenance regimen are vital for sustaining optimal boiler feed water treatment results. Properly trained personnel, automated monitoring tools, and standardized procedures contribute to consistent performance.
Pre-Installation Considerations
Before deploying a treatment system, assess site conditions, available space, and any potential plumbing or electrical requirements. Conducting a pilot test can help fine-tune the setup and validate performance.
Routine Maintenance & Cleaning
Regular membrane cleaning, resin regeneration, and filter replacements prevent buildup of impurities that reduce throughput. Scheduled inspections and proper record-keeping also aid in detecting issues early on.
Monitoring & Automation
Real-time sensors and control systems offer immediate feedback on parameters like conductivity, pH, and temperature. Automated adjustments and alarms enable operators to address deviations before they escalate into costly downtime.
Economic and Environmental Gains
Investing in effective boiler feed water treatment yields significant long-term benefits. By improving energy efficiency and reducing waste, facilities can enjoy financial savings while supporting sustainable operations.
Lower Energy Consumption
Clean, impurity-free water transfers heat more efficiently, cutting fuel costs and easing the burden on boiler components. This decrease in energy usage also helps reduce a facility’s carbon footprint.
Reduced Operational Costs
Minimized scale and corrosion lead to fewer repairs, lower chemical consumption, and extended equipment service life. Combined, these factors can substantially cut day-to-day operational expenses.
Compliance and Sustainability
Strict environmental regulations often mandate wastewater treatment and safe discharge standards. Adhering to these guidelines not only avoids legal penalties but also demonstrates a commitment to responsible resource management.