Ultra Pure Water Treatment
Ultra-pure water (UPW) treatment is a sophisticated process designed to produce water with extremely low levels of impurities, making it suitable for the most sensitive industrial, scientific, and medical applications. UPW systems achieve unparalleled water purity by removing dissolved solids, organic compounds, microbes, and even trace ionic contaminants. Industries such as semiconductors, pharmaceuticals, and power generation rely on UPW to ensure operational excellence and meet stringent quality standards.
As the demand for higher precision and cleaner technologies grows, ultra-pure water treatment systems continue to evolve, integrating advanced purification techniques and automation. These systems not only meet but often exceed international standards for water purity, supporting innovation and efficiency in critical processes.
Applications of Ultra Pure Water Treatment
- Semiconductor Manufacturing: Ensures ultra-clean water for wafer washing, etching, and other precision processes.
- Pharmaceutical Industry: Provides sterile, contaminant-free water for drug formulation and injectable solutions.
- Power Generation: Produces high-purity water for boiler feed to minimize scaling and corrosion.
- Laboratories: Supplies water for analytical instruments and research experiments, ensuring accuracy and reliability.
- Medical Applications: Used in dialysis machines, sterilization processes, and medical device cleaning.
- Food and Beverage: Provides high-purity water for sensitive production processes, including bottled water and baby formula manufacturing.
Key Systems and Technologies Used in Ultra Pure Water Treatment
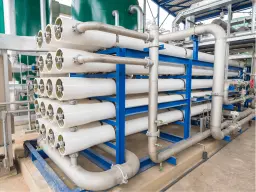
Reverse Osmosis
Removes dissolved salts, organic matter, and particulate contaminants as a core pre-treatment step.
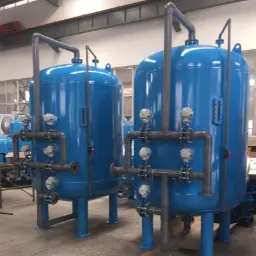
Deionization (DI)
Employs ion exchange resins to eliminate ionic impurities, achieving high conductivity standards.
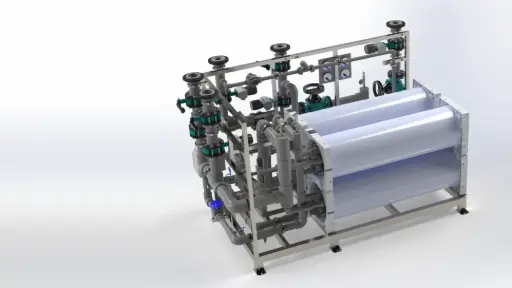
Electrodeionization (EDI)
Combines ion exchange with electrical current to continuously remove ions and regenerate resins.
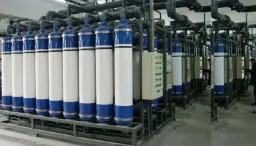
Ultrafiltration
Filters out particles, bacteria, and viruses for enhanced microbial control.
Advantages of Ultra Pure Water Treatment
- Unmatched Purity: Delivers water with conductivity levels as low as 0.055 µS/cm, meeting the strictest standards.
- Operational Reliability: Prevents scaling, corrosion, and contamination in sensitive systems.
- Compliance: Ensures adherence to international quality standards such as ASTM, ISO, and USP.
- Efficiency: Reduces downtime and enhances productivity in industrial and research environments.
- Environmental Responsibility: Advanced systems minimize water and energy wastage, supporting sustainable practices.
Technological Advancements in Ultra Pure Water Treatment
- Integrated Systems: Modular designs combine multiple treatment stages, optimizing performance and reducing footprint.
- Smart Monitoring: Real-time sensors and IoT integration track water quality and system performance.
- Energy-Efficient Technologies: Low-energy membranes and regenerative processes reduce operational costs.
- Automation and Control: Advanced control systems ensure consistent quality and simplify operations.
Challenges and Solutions in Ultra Pure Water Treatment
- Scaling and Fouling: Pre-treatment and regular maintenance prevent deposition issues in membranes and resins.
- Microbial Growth: UV disinfection and periodic cleaning mitigate biofilm risks.
- High Initial Costs: Modular and scalable systems reduce upfront investment for smaller facilities.
FAQs about Ultra Pure Water Treatment
What defines ultra-pure water?
Water with extremely low ionic, organic, and particulate contamination, often exceeding 18 MΩ-cm resistivity.
How is ultra-pure water used in semiconductors?
It cleans wafers and tools, ensuring no impurities interfere with precision manufacturing.
What maintenance is required for UPW systems?
Regular membrane cleaning, resin regeneration, and system inspections are essential to maintain performance.
Can ultra-pure water be recycled?
Yes, advanced recycling technologies enable the reuse of UPW, reducing water consumption and waste.
What are the standards for UPW quality?
UPW must meet standards like ASTM D5127, ISO 3696, and USP for specific industries.
About Ultra Pure Water Treatment
Ultrapure water (UPW) is water that is almost completely free of all impurities and theoretically contains only H+ and OH− ions in equilibrium with H2O molecules. For this reason, the electrical conductivity of ultrapure water at 25°C is approximately 0.055 µS/cm (resistance 18.2 MΩ cm). It contains no measurable levels of anions or cations, organic matter or microorganisms. Thanks to this extreme level of purity , ultrapure water is an indispensable component in many sensitive applications, from laboratory analysis to semiconductor production. However, for the same reason, since it contains no dissolved minerals, it is an extremely “hungry” solvent and actively dissolves ions from the surfaces it comes into contact with; it can even extract electrolytes from the human body, making it unsafe to consume as drinking water.
Ultrapure water has great industrial importance. Especially in the electronics/semiconductor industry , ultrapure water is dependent on it for the flawless operation of circuits in microchip production. Since even the smallest ion or particle contamination can cause malfunctions in electronic circuits, the rinse waters used in production processes must be ultrapure. In the pharmaceutical and biotechnology sectors, ultrapure water is also required for the preparation of injection solutions and cleaning of equipment, and must not contain pyrogens (endotoxins) and microorganisms. In power plants and the energy sector, it is essential that the water fed to high-pressure steam boilers is extremely pure to prevent corrosion and deposit formation. In addition , ultrapure water is used in areas such as food and beverage production and research laboratories to ensure product quality and analysis sensitivity. In this report, ultrapure water production processes and related quality control steps will be discussed in all aspects; measurement methods and ideal values of the parameters will be discussed, and applications in various sectors and future trends will be evaluated.
Ultrapure Water Production Process
Since it is not possible to obtain ultrapure water with a single purification technique, raw water is purified from all unwanted impurities by passing it through a series of consecutive purification steps. In general, source water is first subjected to pre-filtration and conditioning steps, then deionized with pressurized membrane filtration and deionization units. In the final stages, advanced processes are applied to remove organic and microbiological impurities. A typical ultrapure water system includes a multi-stage process such as filtration , reverse osmosis , ion exchange or electrodeionization , ultraviolet (UV) oxidation/disinfection , degassing , and ultrafiltration . The main steps in this process and the function of each are explained below:
Pre-treatment
Raw water (mains water or similar source) is first purified from suspended solids, sediment and free chlorine. For this purpose, particles in the water are usually retained using sand or multi-media filters . Then, chlorine, oxidizing disinfectants such as chloramine and organic matter precursors in the water are adsorbed by passing through an active carbon filter. Chlorine removal is critical in preventing subsequent membrane steps (especially reverse osmosis) from being damaged by chlorine. Depending on the hardness level of the raw water, softening (water softening with ion exchange resins) can also be added to the pretreatment stage to reduce the risk of scaling (limestone accumulation) in reverse osmosis membranes. Indeed, in the pretreatment section of a large-scale ultrapure water plant, water is usually passed through a double-layer (multimedia) filter, then through an active carbon filter and finally through a cationic softening unit; in this way, sediment and hardness that may clog reverse osmosis membranes are removed. Although pretreatment may include different steps depending on the quality of the source water, the main purpose is to reduce the load and extend the life of advanced treatment units.
Reverse Osmosis (RO)
Pretreated water is fed to the reverse osmosis membranes under high pressure . Reverse osmosis is a process that removes most of the dissolved salts, organic matter, and particles by passing water through a semipermeable membrane. During this stage, water molecules pass through the membrane while dissolved ions and other impurities are removed as a concentrated stream. While a single-stage reverse osmosis system typically removes 95–99% of dissolved ions, two-stage (double-pass) RO systems are often used to obtain ultrapure water. With the second-pass RO unit, almost all ions, organic carbon, and colloidal matter in the water can be removed from the water by 99–99.99%. For example, in one application, the conductivity of the water after double-stage RO can be reduced to less than 1 µS/cm, often even to 0.1 µS/cm. The RO effluent is typically taken to an intermediate tank where the water is stored to provide both a continuous feedstock and a balanced flow to downstream processes.
Deionization (Ion Exchange)
Although the conductivity of the water coming out of reverse osmosis is greatly reduced, in order to reach the levels defined as ultrapure water (18 MΩ cm), traces of ions in the water must also be removed. As a classical method , mixed-bed resin columns operating on the ion exchange principle are used. This process consists of columns where a strong acidic cation exchange resin and a strong basic anion exchange resin are located together. While the low-conductivity water coming from the RO unit is passed through the mixed -bed ion exchange column, the residual positive ions in the water (e.g. Na+, Ca2+) are retained by the cation resin and replaced with H+ ions; while negative ions (e.g. Cl-, SO42-) are retained by the anion resin and replaced with OH-. In this way, H+ and OH- combine to form water and the ionic impurities in the water remain in the resins. In order to achieve high purity, more than one mixed-bed column is usually used in series or full performance is achieved by periodic external regeneration. With the ion exchange method, conductivity very close to the theoretical conductivity limit of water, ~0.055 µS/cm, can be achieved. However, this method requires the resins to be regenerated with chemicals such as acid and caustic when their capacity is full. The chemical regeneration process is laborious and environmentally disadvantageous, as it requires both labor and waste neutralization. For this reason, today, classical ion exchange units are largely replaced by continuously operating electrodeionization units (or in some systems, both techniques are used together to provide maximum purity and operational flexibility).
Electrodeionization (EDI)
Electrodeionization , one of the advanced treatment steps , is a process that combines ion exchange and electrodialysis techniques to continuously remove ions from water with the help of an electric field. EDI units consist of cells filled with mixed-bed ion exchange resin and selective ion-permeable membranes adjacent to these cells. Direct current is applied to the water passing through the resin bed, drawing anions toward the anode and cations toward the cathode. As the ions leave the resin bed, they pass through the membrane to the adjacent concentrated flow chamber and are thus removed from the product water. Since the resin is continuously renewed with electricity in this process, no chemical regenerator is needed as in classical systems. EDI is usually integrated into the reverse osmosis outlet and produces water of equivalent quality to mixed-bed deionization. A well-designed EDI system can reduce ionic impurities to <0.1 µS/cm conductivity levels and even weakly ionized species such as silica are reduced to ppb levels. Another advantage of EDI units is that they can operate continuously and there is no fluctuation in water quality during stop-start or regeneration times. This ensures that continuously high purity water is provided, while eliminating repetitive chemical consumption and waste generation. EDI technology has been widespread in the production of high purity water since the 1980s and has replaced traditional ion exchangers in many applications today.
An integrated ultrapure water treatment system consisting of reverse osmosis and EDI units. RO membranes in stainless steel cylindrical bodies on the left, and continuous electrodeionization modules and control panel on the right. These types of compact systems can continuously produce water with a resistance of 18 MΩ cm by sequentially passing feedwater through RO and EDI without the need for chemical regeneration.
UV Oxidation and Disinfection
Ultraviolet (UV) rays are used to purify water from microorganisms and residual organic contaminants. UV lamps with a wavelength of 254 nm are generally used for disinfection purposes in ultrapure water systems; this UV light disrupts the DNA structures of bacteria and other microorganisms and prevents their reproduction. In addition, 185 nm UV lamps are also commonly used to reduce Total Organic Carbon (TOC) levels. The higher energy UV photons at a wavelength of 185 nm create ozone in water, produce hydroxyl radicals, oxidize organic molecules in water and convert them into CO2 and water. Thus, TOC content in water can be reduced to ppb levels. In many ultrapure water systems, water is subjected to ozonation or oxidation with 185 nm UV, followed by both disinfection and ozone removal with 254 nm UV. For example, by adding an ozonation and UV reaction tank after double-stage RO, a step can be applied where residual organic matter in the water is oxidized and microorganisms are killed. After such a step, the excess ozone in the water is broken down by a second UV and the excess ions are retained in the next resin/EDI stage. Thanks to these UV steps, the TOC value of ultrapure water is reduced to very low levels of 5–10 ppb and the risk of biological contamination is minimized.
Degasification
Dissolved gases in water can affect both the conductivity value in ultrapure water systems and are undesirable in terms of corrosion and microbiological growth. Carbon dioxide (CO2) and oxygen (O2) are two important gases in this respect. When CO2 dissolves in water, it forms carbonic acid, increasing the conductivity of the water and decreasing its pH; it can also consume the capacity of anion resins. O2 can accelerate biofilm formation in pure water systems and trigger corrosion in some high-temperature systems (e.g. in power plants). For this reason, a degassing unit is usually found after RO and EDI in ultrapure water production. The most common method is vacuum degasser: Water is flowed in a thin film under low pressure, while the gases above it are removed from the environment by vacuum. Alternatively, membrane degassers are used; in these hydrophobic membrane contactors, water flows on one side of a microporous fiber membrane while vacuum or sweep gas (inert gas such as nitrogen) is passed through the other side. While the membrane retains the water, dissolved gases pass to the vacuum side and are separated from the water. With this technique, CO2 and O2 levels in water can be reduced to very low ppb values. In fact, in an industrial ultrapure water plant, a vacuum deaerator can be used after RO to reduce CO2 and O2 concentrations to <10 ppb each. Then, in the distribution ring, the final trace gases are removed with membrane deaerators, ensuring that the water remains as gas-free as possible. Gas removal is a critical step in helping ultrapure water maintain high resistance and prevent corrosion in the system.
Ultrafiltration and Final Filtration
The final outlet of an ultrapure water system usually contains ultrafiltration (UF) units or similar final filters to capture the smallest particles and microorganisms that may be trapped in the water . Ultrafiltration typically consists of fiber membranes with a pore diameter of 0.01–0.1 µm and can trap colloidal silica, endotoxins (pyrogen) and bacteria that may be trapped in the water. Since removal of particles larger than 50 nm (0.05 µm) is critical, especially in the semiconductor industry, the particle count of the water is controlled by using ultrafilters with a 0.05 µm cutoff diameter prior to the final outlet. In a well-designed system, the water after UF will be free of particles with a size of >0.05 µm, with less than 1 per milliliter. Similarly, UF membranes can be used to remove endotoxins in pharmaceutical ultrapure water systems (such as water for injection). 0.2 µm absolute filters are also often used after the ultrafiltration unit and at the point of use. In this final stage, the water is continuously circulated in the distribution loop , thus preventing stagnant areas in the pipelines, maintaining water quality and preventing biofilm formation. In the final distribution loop, a small low-permeability mixed bed resin cartridge (non-regenerable polisher) and, if necessary, a final UV lamp can be positioned to maintain water quality. At the final outlet of the system, the residual water is continuously monitored for parameters such as resistivity (conductivity), TOC, particle count, silica concentration and is delivered to the points of use.
General view of electrodeionization (EDI) and related purification units in a large-scale ultrapure water plant. In these systems, EDI modules (foreground units) continuously deionize water that has undergone reverse osmosis. In the background, modular EDI units with piping and pumps are seen. EDI is widely used in fields such as the semiconductor and energy industries due to its continuous operation and the lack of chemical regenerators.
Parameters to be Measured
The main parameters that define the quality of ultrapure water and the methods of monitoring them are listed below. Continuous control of these parameters is critical to verify that the water remains at the desired purity and to provide rapid intervention in case of any contamination:
Conductivity (Resistance) : This is the most basic indicator of the level of ionic impurities in ultrapure water. Since pure water has very low conductivity (high electrical resistance), special high-sensitivity conductivity probes are used to measure. Conductivity meters are usually 2-electrode or inductive sensors that can measure 0.1 µS/cm and below. Since water temperature affects conductivity, the devices usually give temperature-compensated readings based on 25°C. The ideal ultrapure water conductivity is ~0.055 µS/cm (18.2 MΩ cm), which is the theoretical limit of pure water. Conductivity measurement is used continuously to monitor the quality of water entering and leaving the system in real time and to monitor resin/RO performance.
Total Dissolved Substance (TDS) : It expresses the total amount of ionic substance contained in water in mg/L (ppm). The TDS value in ultrapure water is negligibly low (usually <0.1 ppm). Although its direct measurement is made by the gravimetric drying method , in practice, TDS is obtained by calculating it from the conductivity value. For example, in laboratory devices, a conductivity of 0.055 µS/cm is shown as ~0 ppm TDS. The TDS value for ultrapure water should ideally be 0 ppm; an increase in the conductivity of the water indicates that the TDS is increasing. Therefore, TDS is not controlled as a separate parameter, but as a derivative of the conductivity.
pH : Although the pH value of ultrapure water is theoretically neutral at 7.0, it is one of the most difficult parameters to measure in practice. Since water has no buffer capacity, it immediately absorbs CO2 from the atmosphere, forming carbonic acid and lowering the pH. For this reason, the pH of freshly dispensed ultrapure water can show any value between 5 and 8. pH measuring devices can give unstable results in ultrapure water; therefore, pH is generally not considered a critical indicator for monitoring ultrapure water quality. However, when pH measurement is required, more stable values can be obtained by using a special pure water pH electrode (suitable for low ionic strength) and adding a neutral salt such as potassium chloride to the measuring cell. Since ultrapure water will drop to around ~5.6 when it comes into contact with air, measuring pH slightly acidic than neutral does not mean that the water is dirty; what is important are indicators such as conductivity and TOC.
Total Organic Carbon (TOC) : It is a total measure of organic matter pollution in water. The amount of organic carbon in ultrapure water should be very low (at ppb levels) because organic residues can cause problems, especially in the semiconductor and pharmaceutical industries, and can be a source of nutrients for bacteria. TOC measurement is performed with special analyzer devices: Usually, the organic carbon in the sample is converted to CO2 with the help of UV rays and/or chemical oxidants and calculated with the amount of CO2 released. For this purpose, NDIR (infrared) detectors or conductivity difference measurement methods are used. Ultrapure water TOC analyzers are sensitive enough to measure in very low ranges such as 1–5 ppb. For example, in pharmaceutical water systems, TOC should be below 500 ppb according to USP; in semiconductor production, TOC < 5–10 ppb is generally targeted. Continuous monitoring of TOC levels is important to keep organic contamination under control. Thanks to modern online TOC analyzers, these low levels are monitored in real time and the performance of components such as the UV oxidation unit is reviewed when any increase is detected.
Temperature : Water temperature is important for both the efficiency of purification processes and the measurement of other quality parameters. Since values such as conductivity and pH are sensitive to temperature, the temperature of the water is monitored with temperature sensors in ultrapure water systems and temperature correction is applied to the measurements. Ultrapure water is usually distributed at ~20–25°C; higher temperatures are not preferred because they can accelerate biological growth. Temperature sensors are also used to control UV reactors or heated sanitization processes. Although the ideal range may vary depending on the system design, it is common to keep the water temperature constant around room temperature.
Microbial Contamination (Bacteria count) : Since ultrapure water does not contain nutrients and is free of disinfectants, microorganisms can reproduce when they find suitable conditions. Therefore, the microbiological purity of water is a critical parameter. Traditionally, a sample is taken to measure the level of bacteria, incubated in the medium, and colony count (CFU/ml) is performed. In addition, rapid methods such as ATP bioluminescence tests or epifluorescence microscopy can be used. In modern ultrapure water facilities, the aim is to ensure that no colony-forming bacteria are detected in the water during routine operation thanks to system design and sanitization . For example, in pharmaceutical waters, the limit is usually <10 CFU/100 ml; in the semiconductor industry, much stricter targets such as <1 CFU/1000 ml are in question. UV disinfection, ozonization and regular hot water/chemical sanitization are applied to keep bacterial growth under control. The microbial quality of the water should be constantly monitored, and the system should be disinfected immediately if any increase is observed.
Silica (SiO₂) : Especially for the electronics and energy sectors, the silica level in water is an important parameter. Silica can be entrained with the steam in steam circuits and deposit on turbine blades or leave unwanted residues on semiconductor chip surfaces. Therefore, the dissolved silica concentration in ultrapure water is usually kept at <1–2 ppb. Silica measurement is done by sensitive colorimetric analysis (molybdate method) or instrumental techniques such as ICP-MS. EDI units are also effective in silica removal; they continuously remove silicate ions with the help of strong basic anion resins and electric fields, reducing the silica level in water to trace levels. In electronics-grade ultrapure water systems, this parameter is also controlled in real time by online measurement with silica sensors.
Particle Count and Size : Submicron particles in water are a critical factor, especially in semiconductor manufacturing, because even a nanoscopic particle settling on the wafer surface can cause a fault in the circuit. Therefore, ultrapure water must have a very low particle load. Laser particle counters are used to monitor particle levels; for example, online counters measure the number of particles per milliliter of water for particles 0.05 µm and above. In a typical semiconductor facility, the target particle count is <1 particle/mL for particles >0.05 µm . If the particle count starts to increase, the integrity of the filters or possible contamination in the system (e.g. resin breakage, biofilm breakdown) is checked. Thus, particle counts are used as a performance indicator of filtration units and verification of water cleanliness.
for all the above parameters are summarized in Table 1. In ultrapure water systems, these values are targeted and any deviation from them is immediately investigated as it may indicate a problem with the performance of the system.
Parameter |
Ideal Value |
Notes |
Conductivity (25°C) |
~0.055 µS/cm (18.2 MΩ cm) |
Theoretical pure water limit
|
Total Organic Carbon (TOC) |
< 5 ppb |
For semiconductor; pharmaceutical water: <500 ppb |
Number of bacteria |
< 1 CFU/100 mL (ideal 0) |
Continuous disinfection with UV and ozone is required |
Silica (SiO₂) |
< 1 ppb |
Critical for semiconductor and energy (turbine) |
Particle (>0.05 µm) |
< 1 unit/mL |
Typical target for semiconductor manufacturing
|
pH |
7.0 ± 1 (measured) |
Observable between 5–8 due to CO₂ absorption |
Heat |
~20–25 °C |
High temperature increases microbial growth |
TDS |
~0mg/L |
Calculated from conductivity (absence of ions) |
Table 1. Main quality parameters and typical ideal values for ultrapure water.
Quality Control Processes
Ultrapure water systems have a comprehensive quality control and monitoring infrastructure to ensure continuity of water quality and to intervene in case of any deviation. Many of the above-mentioned parameters of the produced water are monitored in real time with online sensors and integrated into the process control system. The main quality control methods applied in these systems are explained below:
Continuous Monitoring and Sensors: Instruments such as conductivity, temperature, pH, pressure, flow and tank level sensors are placed at various points in ultrapure water systems. In particular, there is a conductivity sensor at the outlet of each critical treatment step: For example, conductivity is measured at the RO outlet and EDI/ion exchange outlet to monitor the performance of these units. Similarly, UV lamp light intensity monitors may be placed to monitor the effectiveness of the UV disinfection unit or sample points may be placed immediately after the water for microbial counting. TOC analyzers usually measure continuously at the final stage or in distribution lines to check organic matter levels. Particle counters are also integrated into the distribution line in semiconductor plants to continuously count particles of 50 nm and larger in the water. Online analyzers can also be used for specific parameters such as silica and dissolved oxygen. Data from all these sensors is transmitted to a central SCADA/DCS control system.
Data Analysis and Feedback: The real-time data collected is constantly compared with the specified limit values. If any of the quality parameters start to fall outside the target range, the system will give an alarm and automatic/manual intervention mechanisms will be activated. For example, if the conductivity at the EDI output starts to increase, this may indicate that the resin is saturated or that there is a problem with the membrane; the system will notify the operator of the alarm and, if necessary, this part of the water will be returned to the system and not delivered to the point of use. Similarly, if the TOC or particle count is on an increasing trend, the control system will warn the operator about possible organic contamination or filter failure. In advanced systems, this data is examined as a trend in daily and weekly reports and proactive maintenance planning is made. For example, if the differential pressure sensor in a pre-filter shows an increasing blockage over time, it is understood that the filter element is close to replacement time. In this way, the preventive maintenance approach is supported.
Automatic Control and Feedback Mechanisms: Ultrapure water systems generally operate with full automation. PLC/DCS control units adjust pump and valve actuators according to water quality and tank levels. For example, if the level in the storage tank is low, the RO and EDI units automatically start and produce, and if the level is high, they stop. In case of quality deviations, the system can take certain feedback actions: If the conductivity increases at the RO outlet (in case of membrane integrity failure or feed quality deterioration), the second pass RO unit is activated or that water is directed to the waste line. If any bacterial contamination is detected in the distribution line (for example, during ozone measurement or periodic sample analysis), the system can automatically start the ozone generator and circulate the water, starting a sanitization cycle. Thanks to such closed-loop control mechanisms, water quality is kept within the desired range.
Continuous Circulation and Stagnation Control: An important element of maintaining quality in ultrapure water distribution systems is the continuous circulation of water. Water is continuously circulated in a ring-shaped pipeline from the storage tank to the points of use and then returned to the tank. This recirculation ensures that there are no dead spots or stagnant water in the line. In a system where the flow is continuous, the ability of bacteria to adhere to the surface and multiply and the accumulation of particles are minimized. Pipelines are designed so that there are no dead ends called “dead legs”; valves and connections are arranged so that water cannot stagnate and form biofilm. Uninterrupted operation is extremely important in high-purity water systems – since fluctuations in water quality and microbial growth can be observed when the system is stopped and restarted, 24/7 flow is provided whenever possible. For this purpose, redundant installations are made in critical equipment (such as pumps, membranes, EDI modules); while one unit is under maintenance, the other remains in operation and water production continues.
Record Keeping and Quality Assurance: Since ultrapure water is often used in highly regulated applications, it is important to record and regularly report quality data. In a pharmaceutical water system, for example, hourly conductivity and TOC data are recorded electronically to provide traceability. Deviations and actions taken are documented. These records are necessary for both process improvement and compliance audits (e.g. FDA audits). In addition, samples are taken from the system at regular intervals and laboratory analyses (microbiology, endotoxin, trace metal analysis with ICP-MS, etc.) are performed to verify online sensor readings and confirm water compliance with standards.
Thanks to the above quality control practices, ultrapure water systems can be operated with high reliability. Consequently, the better the measurement, monitoring and feedback loop is designed, the better the continuity of water quality will be ensured.
Application Areas and Industrial Use
Ultrapure water is used for critical processes in different industries. The main application areas and their intended uses are summarized below:
Electronics and Semiconductor Industry: One of the most common and critical uses of ultrapure water is in semiconductor chip (wafer) manufacturing. Silicon wafers must be repeatedly rinsed with pure water during photolithography, etching, and cleaning steps. Since even the smallest metal ion or particle in the water can cause defects in integrated circuits, it is imperative that the water used in this process is of ultrapure quality. A modern semiconductor plant can consume thousands of cubic meters of ultrapure water per day; for example, a medium-sized plant processing 200 mm diameter wafers uses ~3000 m3 of ultrapure water per day, which is equivalent to the daily water needs of a city of 20,000 people. For this reason, water treatment facilities are installed in the semiconductor industry and are constantly monitored. Ultrapure water is used in a wide variety of stages, including wafer surface cleaning, preparation of chemical baths, preparation of etching solutions in CMP (Chemical Mechanical Planarization) processes, and final rinsing. As a result, ultrapure water quality in microelectronics production has a direct impact on product yield and device reliability.
Pharmaceutical and Biotechnology Sector: Ultra-high purity water is needed in the pharmaceutical industry in categories such as Water for Injection (WFI) and purified water . In pharmaceutical manufacturing processes, water is used both as a component in the formulation of products and for cleaning production equipment. Pharmacopoeias require that the water used in these areas does not contain pyrogens (endotoxins), has a very low microbial load and is below certain conductivity/TOC limits. For example, there are TOC < 500 ppb and conductivity <1.3 µS/cm (at 25°C) limits for WFI. Ultra-pure water is also critical in biotechnological fermentation processes; when preparing cell culture media, the water must not contain any inhibitory substances. Ultra-pure water is also used in medical device manufacturing and analysis laboratories for error-free results. In the pharmaceutical sector, water systems are usually subjected to regular sterilization cycles with ozone or hot water and continuous quality monitoring (e.g. online TOC analyzers) is performed. In this way, the quality of pure water is kept under control at all times in pharmaceutical production and product safety is ensured.
Food and Beverage Industry: Although the use of ultrapure water in the food sector is more limited compared to others, pure water is preferred at critical points. Especially in beverage production (e.g. beer, soft drinks, dairy products), the taste and purity of water directly affect product quality. Ultrapure water can be used for control purposes in formulations since it is free from foreign substances that can cause taste and odor. For example, in a soft drink production, water is first purified by reverse osmosis and ion exchange and then remineralized in a controlled manner to provide the desired mineral profile. In this way, microbiologically stable and neutral water is obtained and the taste of the product is standardized. Steam boilers and heat exchangers may also require pure water in food facilities; using ultrapure or deionized water as boiler feed water prevents limestone accumulation in the equipment and increases energy efficiency. Highly pure water can also be used in steps such as product washing and bottle rinsing, thus extending shelf life. In the food industry, water systems are regularly cleaned and monitored for hygiene; the use of ultrapure water provides added value especially in refined product groups (e.g. baby food production, distilled beverages).
Energy and Power Plants: Boiler feed water and water used in turbines in thermal power plants, nuclear power plants and other energy production facilities must be ultrapure. The lower the conductivity of water in high-pressure steam circuits, the lower the risk of corrosion and deposits in the system. For this reason, in power plants, raw water is passed through powerful demineralization systems to prepare feed water with very low conductivity . In a typical power plant, RO + mixed bed resin or RO + EDI combination is used to obtain water with <0.1 µS/cm conductivity and <20 ppb silica. This water does not cause silica accumulation on steam turbine blades in the steam circuit and does not leave corrosive ions in the pipelines. As a result, the life of the boilers is extended and their efficiency is maintained. In addition, ultrapure water can be used in generator cooling systems and safety injection systems in power plants (ultrapure water is preferred especially in nuclear reactors in order to avoid neutron-absorbing impurities that will react). Water quality in power plants is continuously monitored by conductivity and pH measurements; If any increase is observed, corrective actions such as regeneration or feed water chemical dosage are immediately implemented.
Research and Analysis Laboratories: Ultrapure water is a basic tool for reliable analytical methods in university and industrial laboratories. The solvent and reagent water used in analytical devices such as HPLC, GC-MS, ICP-MS, AAS should be at the purest level possible so that unwanted peaks or noise do not occur in the measurements. For example, the water used in HPLC mobile phase preparation should have a TOC < 10 ppb and a conductivity of ~0.06 µS/cm to improve detection limits. In molecular biology laboratories, in order to prevent RNase/DNase enzyme activities in DNA and RNA studies, the water should be ultrapure and free of these enzymes. In cell culture studies, the culture mediums are prepared with ultrapure water to eliminate metal ions and organics that may be toxic to cells. Laboratory-type ultrapure water systems (e.g. ASTM Type I water devices) usually include small-scale reverse osmosis, ion exchange, UV and ultrafiltration stages in a compact unit and produce water of the desired purity on the bench. The water provided by these devices is critical to the repeatability and accuracy of experiments. As a result, ultrapure water is used as a reference material in research laboratories and is one of the key elements of experimental success.
Challenges and Future Developments
There are several technical challenges to overcome in the production and distribution of ultrapure water. At the same time, new technologies are being developed in line with the increasing needs and sustainability goals. This section will first address the current challenges and then address future developments.
Technical Challenges and Limitations:
Microbial Contamination: One of the most persistent problems in ultrapure water systems is the growth of microorganisms. Although the lack of nutrients in the water slows down the growth of microbes, if bacteria adhere at any point in the system (for example, in dead volumes), they can rapidly form colonies. This not only deteriorates water quality, but also reduces equipment performance by forming biofilm on membrane and resin surfaces. Periodic chemical cleaning or sanitization with hot water and steam is required to keep microorganisms under control. While biofilm cleaning is carried out regularly with hot (~80–90°C) circulation in pharmaceutical water systems, continuous disinfection with ozonization and UV is preferred in the semiconductor sector. Nevertheless, it is difficult to maintain completely sterile conditions, and this balance is delicate. In modern systems, thanks to the uninterrupted flow of distribution lines and 0.2 µm filters, bacteria are generally undetectable at the points of use, but achieving this result requires serious design and operational discipline.
Particle and Colloidal Contaminants: Nano-sized particles that may be present in ultrapure water can be a critical source of defects, especially in semiconductor manufacturing. Every surface through which water passes (tank, pipe, valve, etc.) can release particles, albeit very low, from the surface of the material. In addition, cell residues resulting from the death of microorganisms in the system also contribute to the particle load. For this reason, it is aimed to have almost no particles larger than 0.05 µm in water. To achieve this, graded barriers such as multimedia filtration, cartridge filters, and ultrafiltration are used. However, due to the limitations of particle measurement technology, it may not be possible to detect colloids, for example, below 10 nm, and particles of this size may not be completely prevented even with developing technology. In addition, factors such as the quality of welding processes performed on in-plant pipes (smooth, particle-free weld seams) and good cleaning of the system during assembly are factors that increase or reduce the risk of particle contamination. It is expected that this problem will be further minimized in the future with more sensitive particle counters and advanced filtration techniques.
Organic Matter and TOC Control: Organic impurities present a dual problem in ultrapure water systems: While they feed bacteria, they can also cause undesirable reactions in semiconductor processes. Keeping organic content in water at incredibly low levels of 1–5 ppb is challenging even with current technology. While RO membranes remove many organics, some low molecular weight carbon compounds (e.g. methane, carbon in acetone) can cross the membrane. Ion exchange resins can also sometimes release organic matter from their own structures (e.g. TOC leakage from new resins during the first water intake). Although organics are oxidized with 185 nm UV and ozonation, reaction byproducts (e.g. formaldehyde, acetate) can be formed and must be captured. TOC analyzers also have a detection limit of only ~0.5 ppb, meaning that even if the TOC value of the water is below the measurement sensitivity, organic molecules may not be completely eliminated. The challenge is to keep the organic content of the water stable at levels that are undetectable by current measurement technologies. Studies on advanced UV-LED technologies, photocatalytic processes or new adsorbent materials are ongoing for more effective organic removal in the future.
Ionic Impurities and Measurement Limits: The ion concentrations of ultrapure water are so low that special methods may be required even for the measurement of some critical ions (e.g. boron, sodium, potassium). The purity standards set for water in the semiconductor industry sometimes exceed the detection limits of existing analyzers. For example, there are metal impurity targets in the ppq (parts per trillion) range, but there is no technology that can routinely measure this. This creates uncertainty in quality assurance: water is theoretically considered clean, but since it cannot be measured, it cannot be definitively verified whether it is really that pure. In addition, it is difficult to measure water with low conductivity accurately; even the slightest CO2 admixture or parasitic effect from the environment in the conductivity sensor can disrupt the measurement. Therefore, utmost care is required in issues such as calibration of measuring devices and sampling techniques. In the future, the development of detection limits of techniques such as ion chromatography and ICP-MS and the provision of online monitoring capabilities will reduce this problem.
Equipment Life and Maintenance: In the operation of ultrapure water systems, the wear and tear of membranes and resins over time and the decrease in efficiency are significant difficulties. RO membranes experience fouling (clogging) problems over time due to hardness and colloidal contaminants in the feed water; if the membranes are not cleaned with periodic chemical cleaning (CIP) processes, the output conductivity increases and the flow rate decreases. Ion exchange resins, even if renewed with regenerations, have a limited life and must be replaced after a certain number of cycles. If scaling or organic accumulation occurs in EDI units, unit performance may deteriorate and the quality of the produced water may decrease. UV lamps lose their effectiveness after a certain number of hours of use and must be replaced. All these maintenance needs should be planned well in order not to disrupt water production. Large facilities usually maintain water quality during maintenance by keeping a spare from each critical unit. Equipment failures or human errors are also situations that put quality at risk; for example, a valve left in the wrong position may cause water to bypass. For this reason, key points in the system are protected with double-check valves and operators receive regular training.
Future Developments and Trends:
Next Generation Purification Technologies: Innovative technologies continue to be developed in ultrapure water treatment. One of these is advanced membrane processes , which have emerged as an alternative or complement to reverse osmosis . For example, methods such as * forward osmosis * and membrane distillation offer the potential for higher purity and energy efficiency than classic RO. However, these technologies are not yet fully established in industrial-scale ultrapure water production. Continuous improvements are also being made in the field of electrodeionization: Higher-efficiency EDI modules and pharmaceutical EDI systems resistant to hot sanitization (up to 80°C) have come onto the market. Electrical water treatment methods such as capacitive deionization (CDI) are also being developed and investigated to obtain water of a quality close to ultrapure water. In the future, systems that can separate salts and organics in a single step with graphene-based membranes may be designed. Another trend in water treatment is to use advanced oxidation processes (AOP) to destroy organic pollutants more effectively, not only with UV but also with combinations such as UV/H2O2, ozone/H2O2, etc. Thus, it will be possible to achieve currently challenging targets such as TOC values <1 ppb.
Better Materials and Designs: The material technology of ultrapure water system components is also evolving. In addition to stainless steel, high-purity PVDF and PFA Teflon derivatives have begun to be used as piping and tank materials. These materials minimize metal ion release and increase resistance to biofilm formation. In addition, modular and compact system design is an important trend: Instead of field assembly, manufacturers offer factory-packaged and tested water treatment skids in modular form. This both shortens commissioning times and allows for easy expansion when capacity increases are needed in the future. Modular design also allows each module to be easily isolated, cleaned, and replaced if necessary. Surface modifications are also being developed for longer life and less fouling tendency in membrane and filter designs (e.g. hydrophilic coatings, antimicrobial surfaces). In the future, it is also expected that water treatment equipment will monitor and report its own status with smart sensors (predictive maintenance).
Sustainability and Environmental Impacts: In the production of ultrapure water, a large amount of wastewater (concentrate) is usually generated and energy is consumed for the sake of high purity. New trends aim for higher recovery rates and lower energy consumption . For example, while a classic RO system operates at 75% efficiency, new multi-stage or feedback RO designs can provide up to 90% water recovery. The focus is on re-evaluating the concentrated water that is released as waste (e.g., using it for the cooling water needs of the facility). Reducing chemical consumption is also critical for the environment: EDI usage is becoming widespread, eliminating regeneration with acid/alkali, and also minimizing chemical waste output thanks to self-degrading disinfectants such as ozone. For energy efficiency, methods such as variable speed pumps, energy recovery devices (especially in RO high pressure lines), and the contribution of waste pressure to electricity generation with turbines are applied. In order to reduce the carbon footprint, projects such as the use of renewable energy for ultrapure water systems (e.g., solar-powered RO pumps) are also being evaluated. In summary, making ultrapure water production greener and more efficient in the future is an important goal.
Increasing Standards and Digital Traceability: As device sizes in the semiconductor industry shrink, water quality standards are constantly tightening. When the concept of “ultrapure water” was first introduced in the 1980s, there were limits to what was compatible with existing technologies, but today, in chip production with 3 nm transistors, water is expected to be almost theoretically pure. This trend will continue: in the future , new definitions such as “ultrapure water” and appropriate methods may come to the fore. In addition, within the scope of Industry 4.0, system optimization and autonomous control are made possible by creating digital twins of water treatment processes. Artificial intelligence-supported control systems can analyze sensor data instantly and carry out processes such as dosing and washing without the need for human intervention. This can eliminate fluctuations in water quality caused by human error.
In summary, R&D studies in the field of ultrapure water focus on both pushing the limits of purity and reducing costs and environmental impacts. With the integration of new technologies into the industry, we will see even more reliable, efficient and sustainable ultrapure water systems in the future.
Conclusion and Recommendations
Ultrapure water production is a complex task that combines complementary multi-stage purification processes, precise measurement and control systems. As detailed in this report, the process of getting water from its source to the ultrapure end product requires a series of steps such as prefiltration, reverse osmosis, deionization, electrodeionization, UV oxidation, degassing and ultrafiltration. Each process targets a specific group of impurities in the water and all these steps must work in perfect sequence to finally obtain pure H2O. The continuity of the quality of the obtained water is possible with the instant monitoring of parameters such as conductivity, TOC, particle count and automatic control of the system.
Ultrapure water plays a critical role in many areas, from high-tech manufacturing to the healthcare sector. Therefore, process optimization and quality assurance are of great importance in terms of both economic efficiency and product quality. In the design of systems, solutions that will ensure that target values are achieved with the least possible waste and lowest energy consumption should be adopted. For example, feed water preconditioning should be done well to extend the life of membrane and resin; the amount of waste water should be minimized with recovery units.
In addition, regular maintenance and trained personnel are indispensable for ultrapure water facilities. As part of preventive maintenance plans, CIP cleaning of membranes, resin changes, and UV lamp checks should not be neglected; sensor calibrations should be verified at certain intervals. The operator and engineering team should be trained to interpret even the slightest change in water quality and to safely operate the system. Procedures for emergency scenarios (such as sudden contamination detection) should be determined in advance, and backup water sources or bypass lines should be planned.
of process optimization , continuous improvement cycles can be carried out by analyzing data collected from existing systems. For example, trend data can be used to determine the ideal periods of chemical cleaning frequency by revealing the membrane fouling rate. Similarly, recycling opportunities (e.g. recovery of some wastewater) can be identified by analyzing water consumption points. Such approaches both provide cost savings and contribute to environmental sustainability.
As a result, the success of ultrapure water systems depends on their design and operation with a holistic engineering perspective. When the right technologies are combined with effective automation and control, it is possible to obtain water with a reliable quality of 18 MΩ cm for a long time. Since even higher purity requirements and efficiency targets will emerge in the future, it is recommended that existing systems be adaptable and scalable. New purification technologies and sensor solutions should be closely monitored, and systems should be kept up to date by integrating suitable ones into existing infrastructures.
As a recommendation , the following principles should be taken into consideration in the installation and operation of ultrapure water facilities:
Correct Design and Integration: A pretreatment sequence appropriate to the raw water characteristics should be selected; solid and organic removal should be ensured in a way that components such as membranes and resins are not overloaded. The output of each process step should be of a quality that will meet the input conditions of the next step. All units should be connected to each other with an integrated automation system to ensure uninterrupted operation.
Redundancy and Uninterrupted Operation: Redundant installations should be made in critical equipment (pump, RO train, EDI module, UV lamp, etc.) to ensure that water production is not interrupted in case of planned maintenance or failure. The system should be kept in continuous flow for 24 hours as much as possible and stoppages should be minimized.
Regular Sanitization: The entire system or sections (tank, distribution line, etc.) should be disinfected at regular intervals to prevent biological growth. Biofilm formation should be prevented proactively by choosing the appropriate method such as ozonization, hot water-steam or chemical (e.g. peracetic acid).
Calibration and Verification: Calibration of online instruments (conductivity meter, TOC analyzer, pH meter, etc.) should be done according to the manufacturer's recommendations, and deviations should be adjusted immediately. In addition, water quality should be checked periodically with independent laboratory analysis to verify the reliability of online measurements.
Data Management and Traceability: Data from the system should be collected in a central database and kept for at least critical parameters. Thanks to these records, long-term trends can be monitored, used for process improvements and retrospective analysis can be performed in case of a possible quality problem.
Sustainability: Water recovery and energy efficiency opportunities should be continuously evaluated and implemented with appropriate investments. For example, integrated approaches such as using waste RO concentrate for a process requiring second-quality water or utilizing waste heat should be considered.
Implementation of these recommendations will optimize both the technical and economic performance of ultrapure water production processes. As a result, maintaining the superior qualities of ultrapure water is possible with a disciplined engineering approach and meticulous operational practices. In this way, the highest purity water required in both industrial production and laboratory environments can be supplied reliably.