Water Conditioning & Treatment in the Electronics & Semiconductor Industry
Modern semiconductor fabs consume millions of liters of water every day, yet the quality demanded by integrated‑circuit manufacturing is among the strictest of any industry. From 3 nm logic to power electronics, even trace ions, organics, or particles can spoil yields and corrode multimillion‑dollar tools. Consequently, fabs invest in multilayered purification trains that convert municipal feed into ultrapure water (UPW), distribute it through high‑polish stainless loops, reclaim spent rinses, and neutralize complex waste streams before discharge. On the regulatory front, tightening discharge permits and corporate ESG targets are pushing plants toward near‑zero‑liquid‑discharge (ZLD) strategies, closed‑loop recycling, and real‑time monitoring of silica, TOC, ammonia, and heavy metals. With chip demand projected to double by 2030, scalable, energy‑efficient water solutions are now as strategic as lithography steppers or EUV masks—making water treatment an integral pillar of competitive, sustainable semiconductor production.
Key Processes Requiring Water Conditioning
Ultrapure Water (UPW) Production
UPW is the backbone of every fab, produced via multi‑stage reverse osmosis, EDI, UV‑TOC oxidation, sub‑micron filtration, and degasification to achieve resistivity > 18.2 MΩ‑cm, TOC < 1 ppb, and SiO₂ < 0.1 ppb. Constant polishing and non‑metallic distribution piping prevent re‑contamination.
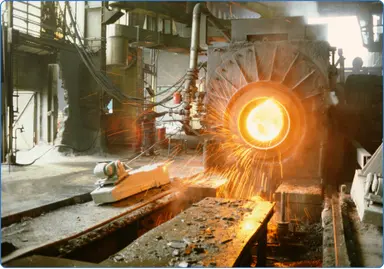
Photolithography Rinse & Develop
After photoresist exposure and development, wafers undergo multiple DI water rinses to remove residual chemicals. Any dissolved silica, particles, or metals can cause pattern collapse or bridging, so low‑silica UPW and point‑of‑use ultrafilters are essential.
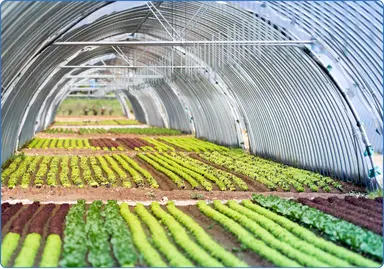
Chemical Mechanical Planarization (CMP)
CMP slurries are a mixture of abrasive particles and oxidizers. High‑flow polish steps require conditioned water for slurry prep and large‑volume post‑CMP cleaning to flush colloidal silica and metals; reclaim loops can recover up to 70 % of rinse water.
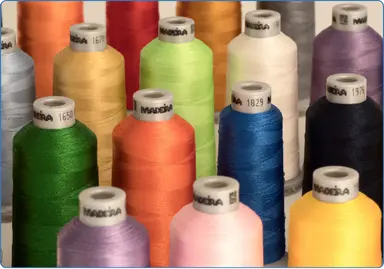
Wet Etching & Cleaning Baths
Acidic or alkaline baths remove oxides and contaminants. Bath makeup water must be ion‑free to maintain process chemistry, while spent baths generate fluoride‑, nitrate‑, and metal‑laden wastewater that needs pH adjustment, precipitation, and membrane filtration prior to reuse or discharge.
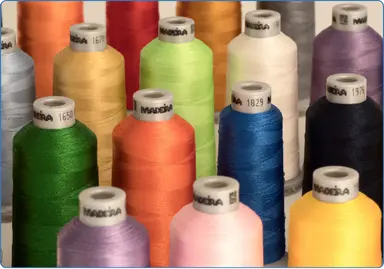
Diffusion Furnace Humidification
High‑temperature oxidation furnaces need ultrapure steam or humidified nitrogen. Any dissolved minerals precipitate as “snow,” creating micro‑defects; hence feed water is first distilled or atomized from UPW.
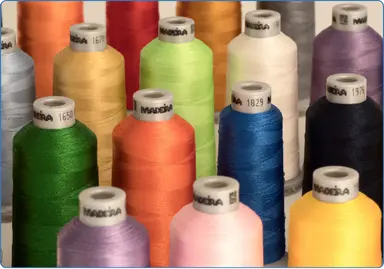
Electroplating & Metal Patterning
Copper and precious‑metal plating cells use conditioned rinse water to control ionic strength and minimize drag‑out. Closed‑loop electrodialysis or ion exchange recovers Cu ²⁺ and Au ³⁺ ions, cutting chemical costs and meeting stringent discharge limits.
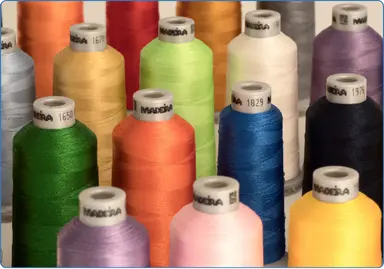
Cooling Towers & HVAC
Process chillers and clean‑room HVAC rely on closed‑loop soft water to avoid scale on heat exchangers. Side‑stream filtration, zinc‑phosphate dosing, and chlorine dioxide control biofouling without releasing corrosive chlorides into the fab environment.
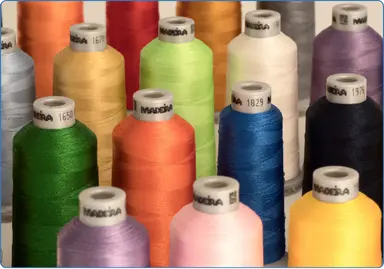
Wastewater Treatment & Reclaim
Blended fab waste combines high‑strength acids, solvents, slurries, and HF‑rich streams. Typical treatment trains include equalization, fluoride precipitation, advanced oxidation, biological TOC removal, membrane bioreactors, and secondary RO—often returning >80 % of effluent to the UPW feed tank.