Zero Liquid Discharge (ZLD) Systems
Zero Liquid Discharge (ZLD) systems are advanced water treatment solutions designed to recover and reuse all water within industrial and manufacturing processes, leaving no liquid waste for discharge. By eliminating wastewater, ZLD systems help industries maximize resource efficiency, comply with strict environmental regulations, and support sustainable water management practices. These systems are particularly valuable in water-scarce regions and highly regulated industries where water conservation and pollution control are critical priorities.
The ZLD process involves a combination of water treatment technologies that separate contaminants from wastewater, reclaim usable water, and convert the remaining waste into solid form for safe disposal. With advancements in membrane filtration, evaporation, and crystallization technologies, ZLD systems have become more energy-efficient and cost-effective, making them a practical solution for industries aiming to achieve sustainability goals.
Key Systems and Technologies Used in Zero Liquid Discharge
Reverse Osmosis (RO)
Removes dissolved solids and recovers high-quality water, serving as a key pre-treatment step.
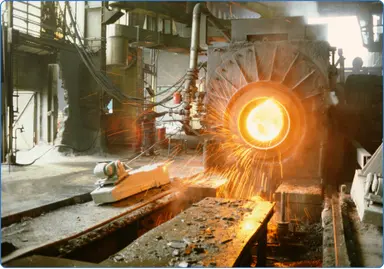
Ultrafiltration (UF)
Includes ultrafiltration and nanofiltration to remove suspended solids and reduce contaminant loads.
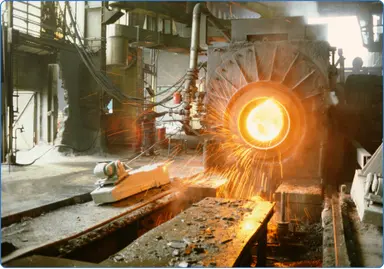
Evaporation Systems
Concentrate wastewater by evaporating water, leaving behind solid residues for disposal.
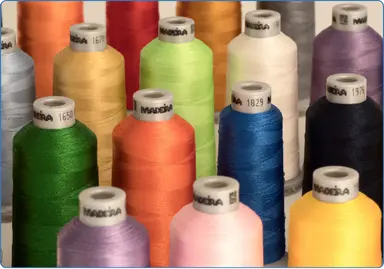
Crystallizers
Convert concentrated brine into solid crystals, ensuring zero liquid discharge.
Applications of ZLD Systems
- Power Plants: Treat cooling tower blowdown and other wastewater streams to recover water and reduce environmental impact.
- Textile Industry: Reuse water from dyeing and finishing processes, minimizing freshwater usage and meeting discharge standards.
- Chemical and Pharmaceutical Manufacturing: Manage complex wastewater streams by recovering water and safely disposing of concentrated residues.
- Petrochemical Industry: Treat refinery wastewater and reuse water in production processes, ensuring regulatory compliance.
- Mining Operations: Handle mine effluents, separating contaminants and recovering water for reuse in ore processing.
Advantages of ZLD Systems
- Complete Water Recovery: Maximizes water reuse by treating and recycling all wastewater.
- Environmental Compliance: Meets stringent discharge regulations by eliminating liquid waste.
- Resource Efficiency: Reduces freshwater consumption, making it ideal for water-scarce regions.
- Sustainability: Supports long-term environmental goals by minimizing pollution and conserving natural resources.
- Economic Benefits: Lowers wastewater disposal costs and improves overall operational efficiency.
Challenges and Solutions in ZLD Implementation
- High Energy Consumption: Advanced energy recovery technologies and hybrid systems help reduce energy usage.
- Scaling and Fouling: Regular maintenance and anti-scaling agents prevent system blockages and ensure reliable performance.
- Initial Investment Costs: Modular and scalable ZLD designs allow gradual implementation, reducing upfront expenses.
FAQs about ZLD Systems
- What industries benefit the most from ZLD systems? Industries such as power generation, textiles, chemicals, mining, and petrochemicals benefit significantly from ZLD systems.
- How does ZLD ensure compliance with regulations? By eliminating liquid discharge, ZLD systems meet strict environmental standards and reduce the risk of regulatory penalties.
- Is ZLD technology suitable for all wastewater streams? ZLD is most effective for wastewater with high concentrations of contaminants and limited discharge options.
- What is the lifespan of a ZLD system? With proper maintenance, ZLD systems typically last 15-20 years.
- How can energy consumption be optimized in ZLD systems? Energy-efficient components such as brine concentrators and heat recovery systems minimize operational costs.