Water Treatment for Aluminum Anodizing and Coating Processes
Aluminum anodizing, also referred to as "anotic oxidation coating" in certain technical contexts, is a widely adopted electrochemical process used to enhance the natural oxide layer on aluminum surfaces. This technique not only amplifies corrosion resistance but also provides a durable, decorative finish suitable for numerous applications, including aerospace, automotive, construction, and consumer goods. To achieve consistent, high-quality aluminum anodizing coatings, the water employed at various stages (pre-treatment, rinsing, and post-treatment) must be meticulously purified.
Water purity influences multiple critical factors in aluminum anodizing. For example, impurities such as dissolved minerals, organic matter, or unwanted ions can trigger surface defects like pitting, discoloration, or streaking. Excessive contaminants also increase the likelihood of chemical imbalances within anodizing baths, causing irregular oxide layer formation. Moreover, suboptimal water quality can diminish the effectiveness of sealing operations, reduce product durability, and escalate operational expenses due to frequent bath replacements. In short, water quality is a foundational element of the entire anodizing sequence, making robust water treatment solutions indispensable for modern anodizing facilities.
In this comprehensive guide, we will explore the key reasons why advanced water treatment is vital for aluminum anodizing, the primary technologies implemented, the benefits in terms of regulatory compliance and sustainability, and actionable best practices that ensure stable, efficient anodizing processes. By focusing on both technical accuracy and practical relevance, this content aims to serve process engineers, plant managers, and decision-makers in anodizing operations who seek to optimize their water management strategies.
Key Water Treatment Technologies for Aluminum Anodizing
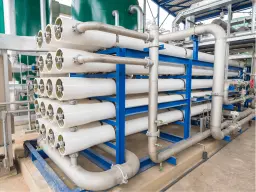
Reverse Osmosis (RO)
RO is frequently the backbone of water treatment systems for anodizing. Equipped with semipermeable membranes, RO units efficiently remove dissolved salts, metals, and organic contaminants, yielding high-purity feedwater. By regulating membrane pore size, modern RO systems can handle wide-ranging feedwater sources, thus guaranteeing consistent water chemistry.
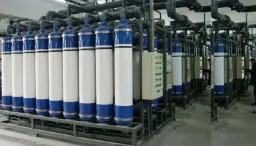
Ultrafiltration (UF)
UF technologies target suspended solids, colloids, and microbiological contaminants. Implemented as a pre-treatment or final polishing step, ultrafiltration membranes help maintain particulate-free water, which is essential for preventing surface blemishes. UF modules also improve the performance and lifespan of downstream systems like RO or DI by reducing fouling potential.
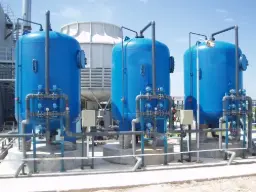
Activated Carbon Filters
Carbon filters eliminate chlorine, chloramines, and a variety of organic compounds that can adversely affect anodizing chemistry. By removing residual disinfectants, activated carbon prevents oxidation of metal surfaces and ensures chemical additives perform as intended.
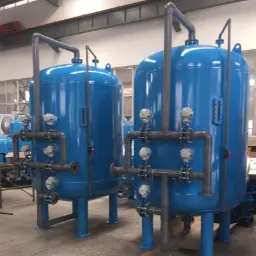
Deionization (DI)
In situations where ultra-low conductivity is required, DI systems are employed either as a stand-alone solution or post-RO polishing stage. Ion exchange resins selectively remove cations and anions, ensuring near-zero conductivity. DI is especially relevant for processes demanding precise chemical conditions, such as specialized anodizing lines used in the aerospace or medical device sectors.
Importance of Water Quality in Aluminum Anodizing and Coating
Aluminum anodizing relies on carefully managed chemical baths and rinses to produce consistent oxide layers. Water carrying contaminants or excessive hardness can compromise these chemical balances. For instance, hardness minerals like calcium and magnesium can precipitate as scale in process tanks or form unwanted deposits on aluminum parts. Dissolved silica, chlorides, or sulfates can interfere with the anodizing chemistry, leading to blotchy or uneven coatings.
Another aspect to consider is microbial contamination. Bacterial growth in rinse tanks can cause biofilm accumulation, which disrupts rinsing efficiency and can even contaminate subsequent stages. High bacterial loads in water can also negatively interact with certain additives or brighteners in the anodizing bath. Consequently, ensuring microbial control is just as critical as removing dissolved solids.
Benefits of Advanced Water Treatment
- Enhanced Coating Quality: By maintaining stable water parameters, anodizers minimize surface imperfections, achieve uniform color consistency, and maximize corrosion resistance.
- Extended Bath Life: Cleaner feedwater reduces bath contamination rates, lowering the frequency of bath maintenance or disposal. This directly translates into cost savings.
- Regulatory Compliance: Many regions impose strict guidelines on industrial effluent discharges, particularly metals and chemicals. With advanced treatment, anodizing facilities stay compliant and avoid potential fines.
- Sustainability Gains: Reduced water consumption and minimized chemical usage help anodizers meet environmental objectives, thereby strengthening corporate social responsibility efforts.
- Operational Efficiency: Fewer production stoppages due to equipment fouling or bath contamination, thus improving throughput and process stability.
Best Practices and Recommendations
- Conduct Regular Water Testing: Periodic testing for hardness, TDS (total dissolved solids), microbial content, and specific ions helps in adjusting treatment systems proactively.
- Implement Real-Time Monitoring: Automated sensors and control loops for pH, conductivity, and oxidation-reduction potential (ORP) can promptly detect anomalies, preventing larger issues.
- Optimize Membrane Maintenance: Scheduled cleaning of RO and UF membranes ensures consistent flux rates and extended membrane life.
- Engage Qualified Suppliers: Collaborate with water treatment specialists who have experience in aluminum anodizing to tailor solutions to your facility’s needs.
- Prioritize Staff Training: Equip operators with knowledge on system operations, basic troubleshooting, and the significance of water quality in anodizing.
Frequently Asked Questions
- Why is water treatment important in aluminum anodizing? Water purity directly impacts oxide layer formation, preventing defects like pitting, discoloration, and scaling.
- What contaminants are commonly removed in anodizing water treatment? Typical contaminants include dissolved minerals (calcium, magnesium), chlorides, sulfates, organic matter, and bacteria.
- Can treated water be recycled in anodizing processes? Yes, implementing wastewater treatment and recycling loops reduces fresh water usage and lowers operational costs.
- How often should anodizing water treatment systems be maintained? Regular inspections, membrane cleaning, and filter replacements are generally recommended every 6-12 months.
- Does microbial control matter in anodizing water? Absolutely. High bacterial loads can cause biofilm accumulation and chemical imbalances in the anodizing bath.