Enjeksiyonluk Su (WFI) Uygulamaları
Enjeksiyonluk Su (WFI), enjekte edilebilir ilaçların üretimi ve çeşitli tıbbi uygulamalarda kullanılan son derece saf ve steril bir su türüdür. İlaç üretiminde en kritik bileşenlerden biri olan WFI, Amerika Birleşik Devletleri Farmakopesi (USP) ve Avrupa Farmakopesi (EP) gibi sıkı farmakopel standartlarına uygun olmalıdır. Bu standartlar, suyun mikrobiyal kontaminasyon, endotoksinler ve partikül maddelerden arındırılmasını sağlayarak güvenliğini ve tıbbi ürünlerle uyumluluğunu garanti eder.
WFI'nin üretimi ve kullanımı, ilaç formülasyonu, temizlik süreçleri ve sterilizasyon gibi kritik rolleri nedeniyle sıkı bir şekilde düzenlenir. WFI, parenteral çözeltilerin hazırlanması, aktif farmasötik bileşenlerin (API'ler) seyreltilmesi ve üretim ekipmanlarının temizlenmesi gibi birçok alanda kullanılır. Ters ozmoz, elektrodeiyonizasyon ve ultrafiltrasyon gibi su arıtma teknolojilerindeki ilerlemeler, WFI'nin en yüksek kalite standartlarını korurken verimli bir şekilde üretilmesini sağlamıştır.
WFI Üretiminde Kullanılan Ana Sistemler ve Teknolojiler
Ters Ozmoz (RO)
Çözünmüş tuzları, organik maddeleri ve partikülleri uzaklaştırarak temel bir ön arıtma adımı sağlar.
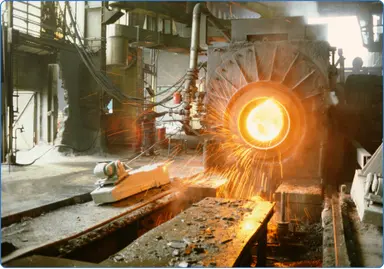
Ultrafiltrasyon (UF)
Endotoksinleri, bakterileri ve partikülleri ortadan kaldırarak mikrobiyal kontrol sağlar.
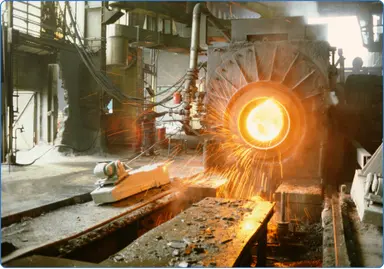
Distile Su Sistemleri
Buharlaşma ve yoğunlaşma yoluyla safsızlıkları uzaklaştırarak farmakopel standartlara uyumu garanti eder.
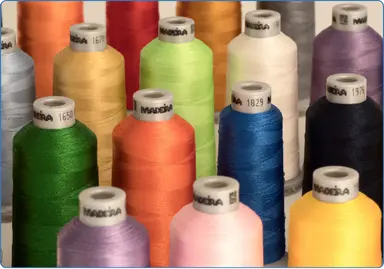
Elektrodeiyonizasyon
İyon değişimi ve elektrik akımını birleştirerek kimyasal yenileme gerektirmeden sürekli ultra saf su üretir.
Enjeksiyonluk Su (WFI) Uygulamaları
- Enjekte Edilebilir İlaç Üretimi: Aşılar, biyolojik ürünler ve intravenöz çözeltiler gibi parenteral formülasyonlar için çözücü görevi görür.
- Sterilizasyon ve Temizlik: İyi Üretim Uygulamaları'na (GMP) uygunluğu sağlamak için üretim ekipmanlarının temizliğinde ve sterilizasyonunda kullanılır.
- Farmasötik Formülasyonlar: Aktif farmasötik bileşenlerin (API) hazırlanmasında dilüent olarak kullanılır.
- Tıbbi Cihaz Üretimi: Kritik tıbbi cihazların üretiminde sterilliği sağlar.
Enjeksiyonluk Su (WFI) Avantajları
- Ultra Saflık: Mikrobiyal ve endotoksin seviyeleri için en sıkı gereklilikleri karşılayarak enjekte edilebilir ilaçlar için güvenlik sağlar.
- Regülasyonlara Uygunluk: USP, EP ve JP gibi uluslararası farmakopel standartlarına uygundur.
- Çok Yönlülük: İlaç formülasyonundan ekipman temizliğine kadar geniş bir farmasötik ve tıbbi uygulama yelpazesi için uygundur.
- Operasyonel Verimlilik: Modern WFI sistemleri sürekli üretim için tasarlanmıştır, kesinti süresini en aza indirir ve üretimi maksimize eder.
- Risk Azaltımı: Kontaminasyonu önler ve kritik üretim ortamlarında ürün güvenliğini sağlar.
WFI Üretiminde Karşılaşılan Zorluklar ve Çözümler
- Sıkı Kalite Gereklilikleri: Gelişmiş arıtma teknolojileri ve gerçek zamanlı izleme sistemleri, farmakopel standartlara uyumu garanti eder.
- Mikrobiyal Kontrol: Ultrafiltrasyon ve UV dezenfeksiyon gibi teknolojiler ve düzenli sistem doğrulaması mikrobiyal riskleri en aza indirir.
- Enerji Tüketimi: Gelişmiş distilasyon üniteleri ve düşük enerjili RO membranları gibi enerji verimli sistemler, operasyonel maliyetleri düşürür.
- Sistem Bakımı: Düzenli temizlik ve izleme, ölçeklenme, kirlenme ve kontaminasyonu önler ve tutarlı performansı garanti eder.
Enjeksiyonluk Su (WFI) Hakkında Sıkça Sorulan Sorular
- WFI için temel standartlar nelerdir? WFI, mikrobiyal limitler, endotoksin seviyeleri ve saflığa odaklanan USP, EP ve JP gibi farmakopel standartlara uygun olmalıdır.
- WFI (Enjeksiyonluk Su) nasıl üretilir? WFI genellikle ters ozmoz, elektrodeiyonizasyon ve distilasyon gibi teknolojilerle üretilir.
- WFI sistemleri sürekli çalışabilir mi? Evet, modern WFI sistemleri sürekli üretim için tasarlanmıştır ve üretim süreçleri için güvenilir bir tedarik sağlar.
- WFI ile saf su arasındaki fark nedir? WFI, mikrobiyal kontaminasyon ve endotoksinler gibi daha sıkı saflık gereksinimlerine sahiptir ve enjekte edilebilir ilaçlar için uygundur.
- WFI sistemlerinde mikrobiyal kontaminasyon nasıl önlenir? Ultrafiltrasyon, UV dezenfeksiyon ve sıkı sistem doğrulama kullanılarak mikrobiyal kontaminasyon önlenir.
Enjeksiyonluk Su (WFI) ve İlgili Prosesler
Enjeksiyonluk Su Nedir, Kullanım Alanları Nelerdir?
Enjeksiyonluk su (Water for Injection, WFI), enjekte edilebilir ürünlerin hazırlanmasında kullanılan son derece saf bir suyu ifade eder. WFI, mikroorganizma, organik madde ve iyon gibi safsızlıkların en aza indirildiği, çok yüksek saflıkta bir su kalitesidir. Çoğu zaman WFI, farmasötik üretimde bir bileşen veya çözücü olarak kullanılır ve parenteral (enjeksiyon yoluyla verilen) ürünlerin güvenliği için kritik öneme sahiptir. WFI’nin sterilize edilmemiş hali üretim süreçlerinde kullanılabilirken, doğrudan hastaya uygulanacak çözeltilerin hazırlanmasında genellikle sonradan sterilize edilmiş veya zaten steril haldeki WFI tercih edilir.
WFI, özellikle ilaç endüstrisi, biyoteknoloji ve tıbbi uygulamalarda vazgeçilmezdir. Farmasötik sektörde, intravenöz enjeksiyonluk solüsyonların hazırlanmasında zorunlu olarak WFI kullanılır. Örneğin, serumlar, aşılar, intravenöz infüzyon solüsyonları ve diğer parenteral ürünler hazırlanırken çözücü olarak WFI kullanılması yasal bir gerekliliktir. Biyoteknoloji sektöründe, hücre kültürü ortamlarının hazırlanmasında, biyolojik etkin maddelerin seyreltme işlemlerinde ve ürün saflaştırma adımlarında WFI kullanılabilir. Tıbbi cihaz üretiminde ise implant edilebilir tıbbi cihazların temizlenmesi, hemodiyaliz solüsyonları ve hemofiltrasyon sıvıları gibi uygulamalarda WFI tercih edilir. Ayrıca hastane ve klinik ortamlarında, ilaç tozlarının enjeksiyon öncesi çözünmesi ya da cerrahi irrigasyon solüsyonlarının hazırlanması gibi amaçlarla da WFI kullanımı yaygındır. WFI’nin bu denli yaygın ve zorunlu kullanımı, hasta güvenliği açısından suyun saflık standardının ne kadar önemli olduğunu gösterir.
WFI’nin önemi uluslararası sağlık otoritelerince de vurgulanmaktadır. Örneğin Dünya Sağlık Örgütü (WHO), steril enjeksiyonluk suyu temel ilaçlar listesine dahil etmiştir. Bu, WFI’nin sağlık sistemi için kritik bir kaynak olduğunu gösterir. Sonuç olarak, WFI; farmasötik formülasyon hazırlama, ekipman-temas yüzeylerini yıkama, tıbbi cihazları durulama gibi çeşitli alanlarda kontaminasyon riskini en aza indirerek güvenli üretim ve uygulama imkânı sağlar.
Üretim Yöntemleri
WFI üretimi, suyun tüm kirleticilerden arındırılması amacıyla son derece sıkı kontrollere tabi ileri arıtma yöntemleriyle gerçekleştirilir. Geleneksel olarak en güvenilir yöntem, distilasyon (damıtma) işlemidir. Tarihsel olarak farmakopeler, WFI elde etmek için yalnızca distilasyonu kabul etmişlerdir. Nitekim yaklaşık bir asır boyunca WFI, çok kademeli distilasyon cihazları ile üretilmiştir. Distilasyon suyu kaynatıp buharlaştırarak ve ardından yoğunlaştırarak iyonları, mikropları ve piröjenleri etkin biçimde uzaklaştırır. Ancak son yıllarda ters ozmoz (RO), elektrodeiyonizasyon (EDI) ve ultrafiltrasyon (UF) gibi membran filtrasyon teknolojilerindeki gelişmeler, bu yöntemlerle de WFI kalitesinde su üretmeyi mümkün kılmıştır. 2017’de Avrupa Farmakopesi, ABD Farmakopesi’nin uzun zamandır izin verdiği şekilde, distilasyona eşdeğer saflıkta su üreten alternatif yöntemlere onay vermiştir. Böylece, uygun şekilde tasarlanıp valide edildiği takdirde membran tabanlı arıtma sistemleriyle de WFI üretilebilmektedir. Aşağıda, WFI üretiminde yaygın olarak kullanılan başlıca yöntemler ve süreç adımları açıklanmaktadır.
Distilasyon Yöntemi ile Üretim
Distilasyon, ham suyun saf buhara dönüştürülüp tekrar yoğunlaştırılması prensibine dayanır. WFI elde etmek için tasarlanmış distilasyon sistemleri genellikle çok kademeli yapıdadır (multi-effect distilasyon) veya buhar sıkıştırmalı distilasyon (vapor compression) kullanır. Multi-effect sistemlerde, birinci kolonun ürettiği buhar, ikinci kolonu ısıtmakta kullanılır ve bu süreç birden fazla kolon boyunca tekrarlanarak enerji verimliliği sağlanır. Buhar her kademede yeniden yoğunlaştırılarak yüksek saflıkta distilat elde edilir. Aşağıda çok kolonlu bir distilasyon sistemine ait bir örnek görülmektedir:
Şekil 1: Birden çok kolonlu distilasyon (multi-effect) sistemi. Paslanmaz çelik kolonlarda su art arda buharlaştırılıp yoğunlaştırılarak WFI elde edilir.
Distilasyon yoluyla WFI üretimindeki tipik adımlar aşağıdaki gibidir:
Ön Arıtma
Ham su (şebeke suyu gibi) distilasyona girmeden önce ön filtrasyon ve şartlandırmadan geçirilir. Bu aşamada su, kum veya kartuş filtrelerden geçerek partiküllerden arındırılır; aktif karbon filtre ile klor gibi organik olmayan oksidanlardan temizlenir ve gerekiyorsa yumuşatma işlemiyle sertlik giderilir. Ön arıtma, distilasyon ekipmanının kireçlenmesini ve aşırı yüklenmesini önlemek için kritik bir adımdır.
Distilasyon (Damıtma)
Ön arıtılmış su, distilasyon cihazının evaporatör kısmında kaynatılır. Elde edilen su buharı, uçucu olmayan tüm safsızlıkları geride bırakır. Multi-effect distilasyonda buhar ardışık kolonlara yönlendirilerek tekrar buharlaştırma-yoğunlaştırma döngüsüne girer. Her bir kolon tepesinde bulunan özel ayırıcılar, buhar içinde sürüklenmiş olabilecek damlacıkları ve kalan partikülleri ayırarak pirojensiz (endotoksinsiz) “kuru” buhar elde edilmesini sağlar. Bu saf buhar, kondenser bölümünde tekrar suya dönüştürüldüğünde WFI elde edilmiş olur. Eğer sistem vapor compression tipindeyse, üretilen buhar bir kompresör yardımıyla basıncı artırılarak tekrar yoğunlaştırma için kullanılır, bu sayede enerji tasarrufu sağlanır.
Depolama ve Dağıtım
Distilasyon cihazından çıkan sıcak distilat suyu genellikle doğrudan WFI tankına alınır. Distilasyon işlemi genellikle WFI’ı yaklaşık 70-80°C gibi yüksek sıcaklıkta üretir; bu sıcaklık, üründe mikrobiyal kontaminasyonu önlemeye yardımcı olur. Depolama tankı ve dağıtım hatları, tipik olarak 80°C civarında sıcaklığı koruyacak şekilde tasarlanır. Suyun sürekli sirkülasyonu sağlanarak hem homojen bir sıcaklık dağılımı elde edilir hem de ölü noktalarda durgunluk engellenir.
Damıtma Yönteminin Avantajları ve Dezavantajları
Distilasyon yönteminin avantajları ve dezavantajları şöyle özetlenebilir:
Distilasyon Sistemi Avantajları
Güvenilir Saflık: Distilasyon, suyu buharlaştırıp yoğunlaştırdığı için iyonları, mikroorganizmaları ve endotoksinleri etkin şekilde ayırır. Bu işlem, doğal bir bariyer görevi görerek piröjenik maddelerin ürün suya geçmesini engeller. Sonuçta elde edilen distilat, farmakope saflık kriterlerini rahatlıkla karşılar.
Mikrobiyal Kontrol: Distilasyon genellikle yüksek sıcaklıkta gerçekleştiğinden, süreç sırasında bakterilerin yaşama şansı yoktur. Ayrıca distilatın sıcak tutulması sayesinde sistem kendi kendini dezenfekte etme özelliğine sahip olur. Bu, özellikle sürekli sıcak (hot WFI) döngülerinde biyofilm oluşumunu minimize eder.
Regülasyon Uyumu: Distilasyon, uzun yıllardır dünya çapında düzenleyici otoritelerin tercih ettiği yöntem olmuştur. Hem ABD (USP) hem Avrupa (EP) gibi büyük farmakopelerde distilasyonla üretilen WFI için geniş bir tecrübe ve kılavuz bulunur, bu da denetimlerde güven yaratır.
Distilasyon Sistemi Dezavantajları
Yüksek Enerji ve Maliyet: Su kaynatma ve buhar kondansasyonu, ciddi miktarda enerji gerektirir. Distilasyon sistemleri, buhar üretmek için genellikle büyük miktarda buhar veya elektrik tüketir ve bu da işletme maliyetlerini artırır. Özellikle geleneksel çok kademeli distilasyon, sürekli ısıtma ve soğutma döngüleri nedeniyle enerji verimliliği düşük bir süreçtir. Membran sistemlere kıyasla distilasyonun işletme maliyeti %90’a varan oranda daha yüksek olabilmektedir.
Yatırım Maliyeti ve Altyapı: Distilasyon cihazlarının kurulumu, paslanmaz çelik kolonlar, buhar jeneratörü, kondansörler gibi kompleks ekipmanlar içerdiğinden yüksek başlangıç yatırım maliyeti gerektirir. Ayrıca bu sistemlerin barındığı alan, borulama ve izolasyon ihtiyaçları da fazladır. Membran tabanlı bir sisteme göre tesis içinde daha büyük bir alan kaplar ve daha karmaşık bir altyapı ister.
Bakım ve İşletim Zorlukları: Distilasyon üniteleri, düzenli bakım (örn. ısı değiştirici yüzeylerinin temizlenmesi, ölçek/kireç birikiminin giderilmesi) gerektirir. Besleme suyunda sertlik kontrolü iyi yapılmazsa taş (kireç) oluşumu kolonların ısı transfer verimini düşürebilir. Cihazın çalışması esnasında sürekli buhar ve soğutma suyu dengesi sağlanması gerektiğinden operasyonda uzmanlık ihtiyacı yüksektir.
Membran Filtrasyon Yöntemleri ile Üretim
Membran teknolojilerine dayalı üretim, suyun kaynatılmaksızın mekanik/elektriksel ayırma yöntemleriyle arıtılmasını içerir. Özellikle ters ozmoz (RO), elektrodeiyonizasyon (EDI) ve ultrafiltrasyon (UF) kombinasyonları kullanılarak WFI seviyesinde saf su elde etmek mümkündür. Membran yöntemlerinde amaç, uygun bir dizi arıtma adımı ile sudaki iyonları, organik maddeleri, partikülleri ve mikroorganizmaları yakalayıp uzaklaştırmaktır. Tipik bir membran tabanlı WFI üretim süreci aşağıdaki aşamalardan oluşur:
Ön Arıtma
Distilasyonda olduğu gibi, membran sistemlerinde de ham su önce ön işleme tabi tutulur. Filtrasyon (kartuş filtreler, kum filtreleri vb.) ile partiküller alınır, aktif karbon filtrelerle klor ve organik kirleticiler giderilir, su yumuşatma ile sertlik düşürülür. Bu adım, membranların tıkanmaması ve ömrünün uzun olması için önemlidir.
Birinci Pass Ters Ozmoz (RO)
Ön arıtmadan geçen su, yüksek basınçla ters ozmoz membranlarına beslenir. Ters ozmoz membranları, su moleküllerini geçirirken çözünmüş tuzların, büyük organik moleküllerin ve mikroorganizmaların büyük kısmını tutar. İlk pass RO’dan çıkan permeat (ürün suyu), toplam çözünmüş iyonların büyük ölçüde (~%98) giderildiği düşük iletkenlikte bir sudur.
İkinci Arıtma Adımı (RO veya EDI)
Tek kademeli RO genellikle WFI saflığı için yeterli olmadığından, ikinci bir arıtma adımı gerekir. İkinci adım olarak ya bir ikinci pass RO ünitesi ya da EDI (Elektrodeiyonizasyon) modülü kullanılır. İkinci pass RO, kalan iyonik kirleticilerin çoğunu da süzer; EDI ise iyon değiştirici reçineler ile membranları elektrik akımı altında birleştirerek suyu sürekli deiyonize eder. EDI modülü, suyu tamamen demineralize ederek iletkenliği ultra düşük seviyelere çeker ve aynı zamanda yüksek pH gradyanlarıyla organik maddelerin ve bakterilerin yok edilmesine katkı sağlar. Bu aşama sonunda su, iyonik olarak WFI kriterlerini karşılayacak saflığa ulaşır.
Ultrafiltrasyon (UF) (gerekirse)
WFI üretiminde en kritik konulardan biri endotoksinlerin giderilmesidir. RO membranları ve EDI, birçok bakteriyi ve endotoksini tutsa da, ek bir güvence olarak ultrafiltrasyon kullanılabilir. UF membranları tipik olarak 6.000 Dalton mertebesinde kesme değerine sahiptir ve bakteri, endotoksin gibi daha büyük molekülleri süzebilir. Bazı sistemlerde ikinci RO yerine UF kullanılarak son aşamada suyun endotoksin yönünden de arıtılması sağlanır. Ultrafiltrasyon modülleri de sıcak su veya kimyasallarla dezenfekte edilebilir yapıdadır.
Depolama ve Dağıtım
Membran sistemi çıkışındaki su, uygun kaliteyi sağlıyorsa WFI tankına alınır. Membran ile üretilen WFI genellikle ortam sıcaklığında çıkış yapar (soğuk WFI). Bu nedenle, mikrobiyal büyümeyi önlemek için depolama ve dağıtım sisteminin düzenli olarak dezenfekte edilmesi kritik önem taşır. Modern membran WFI sistemleri, sıcak su ile periyodik sanitizasyon (örneğin 80-85°C su sirkülasyonu) veya ozon/UV gibi dezenfeksiyon yöntemleriyle biyofilm oluşumunu engelleyecek şekilde tasarlanır. Soğuk WFI depolarken tankın havası 0,2 µm hydrophobic hava filtresi ile korunur ve gerekirse depo içinde ozonlama gibi yöntemlerle mikrop üremesi baskılanır.
Membran Filtrasyonunun Avantajları ve Dezavantajları
Membran Filtrasyonu Avantajları
Enerji ve Maliyet Tasarrufu: Membran prosesleri faz değiştirme (buharlaştırma) gerektirmediği için enerji tüketimi çok daha düşüktür. Distilasyonla kıyaslandığında membran sistemler, işletme giderlerinde %90’a varan tasarruf sağlayabilir ve yatırım maliyetlerini de %70’e varan oranda azaltabilir. Özellikle büyük hacimli su ihtiyacı olan tesislerde, distilasyon yerine RO/EDI kullanımı ekonomik açıdan çok avantajlıdır.
Daha Küçük Kurulum Alanı: Membran sistemleri genellikle kompakt, paket sistemler şeklinde tasarlanabilir. Bir skid üzerine monteli RO+EDI+UF sistemi, eşdeğer kapasiteli bir çok-etkili distilasyon ünitesine göre daha az yer kaplar ve tesis içi yerleşimde esneklik sağlar. Ayrıca bu sistemlerin devreye alınma süresi kısadır ve modüler yapı sayesinde kapasite artırımı veya taşıma daha kolaydır.
Anlık Kullanıma Uygunluk: Membran sistemler, aç-kapa operasyonlara ve değişken üretim hızlarına daha çabuk adapte olabilir. Distilasyon sisteminde olduğu gibi ısıtma için uzun süre bekleme gerekmediğinden, su üretimini ihtiyaca göre hızlı başlatıp durdurmak mümkündür. Bu da özellikle aralıklı üretim yapan tesislerde operasyonel verimlilik sağlar.
Daha Az Atık ve Su Kullanımı: İyi tasarlanmış membran sistemlerinde su geri kazanımı yüksek olabilir. Distilasyonda, kazan blowdown’u ve soğutma suyu gibi kayıplar olurken, çift kademeli RO/EDI sistemleri besleme suyunu büyük oranda ürüne çevirir ve daha az atık konsantre bırakır. Bu da sürdürülebilirlik açısından olumlu bir etkidir.
Membran Filtrasyonu Dezavantajları
Mikrobiyal Kontaminasyon Riski: Membran sistemlerinin en büyük zorluğu, mikroorganizma üremesine daha açık olmalarıdır. Oda sıcaklığında çalışan RO/EDI üniteleri, eğer düzenli sanitizasyon yapılmazsa biyofilm oluşumuna zemin hazırlayabilir. Ayrıca RO membranlarının iç yüzeyi genellikle “sanitary” (hijyenik tasarım) değildir ve girintili yapısı bakterilerin tutunup çoğalmasına imkan verebilir. Bu nedenle membran sistemlerinde mikrobiyal kontrol için UV lambaları, düzenli sıcak su/kimyasal sanitizasyon ve sıkı izleme şarttır.
Membran Arızaları ve Güvenlik: RO membranları ve EDI üniteleri, fiziksel hasar veya yıpranma sonucu sızıntı yapabilir. Özellikle RO’da, yüksek basınçlı ham su tarafı ile saf su tarafı arasında bir bariyer olduğundan, bir membran bütünlüğü bozulursa ham sudaki kirleticiler ürün suyuna geçebilir. Bu riskleri azaltmak için sistemde çift kademeli membranlar, bütünlük testleri (ör. UF modülleri için basınç tutma testleri) ve sürekli kalite izleme cihazları kullanılmalıdır.
Validasyon ve Regülasyon Süreci: Tarihsel olarak Avrupa otoriteleri, WFI için membran yöntemlerine temkinli yaklaşmış ve sadece distilasyona izin vermiştir. Günümüzde EP değişmiş olsa da, firmaların membran sistemleri kapsamlı bir şekilde valide etmeleri ve distilasyon kadar güvenli olduğunu kanıtlamaları beklenir. FDA/EMA gibi otoriteler özellikle mikrobiyal kontrol planlarına ve sürekli izleme verilerine büyük önem vermektedir. Bu da membran sistemlerinin işletilmesinde daha yoğun dokümantasyon ve denetim gereksinimi anlamına gelir.
Bakım ve Tüketim Kalemleri: Membranların periyodik olarak kimyasal temizliği (CIP) ve belli aralıklarla değiştirilmesi gerekir. Örneğin, klor geçişi olursa RO membranları zarar görebilir; bu yüzden ön arıtmadaki karbon filtrenin düzenli yenilenmesi şarttır. EDI üniteleri hassastır ve besleme suyu kalitesi dalgalanırsa performans düşebilir. Bu nedenle membran sistemlerinin bakım maliyeti distilasyonun buhar kazanı bakımına karşılık, membran/filtre değişimleri şeklinde ortaya çıkar.
Kontrol Edilmesi Gereken Parametreler
WFI üretimi ve kullanımı esnasında, suyun istenen kalite standartlarını koruyup korumadığını doğrulamak için çeşitli kalite kontrol parametreleri izlenir. Farmakope tanımlarında WFI için belirlenmiş olan bu parametreler ve kabul kriterleri, ürünün güvenliğini ve saflığını garanti altına almayı amaçlar. Başlıca kontrol edilen parametreler şunlardır:
İletkenlik (Conductivity)
Suyun elektrik iletkenliği, içerdiği iyonik safsızlıkların bir göstergesidir. Teorik olarak ultra saf su çok düşük iletkenliğe sahiptir (25°C’de ~0.055 µS/cm, tamamen saf H₂O için). Farmakope kriterlerine göre WFI’nın iletkenliği 25°C’de 1.3 µS/cm’yi geçmemelidir. Avrupa Farmakopesi biraz farklı bir ölçüm sıcaklığı kullanarak 20°C’de maksimum ~1.1 µS/cm değeri vermiş, ancak bu USP ile uyumlu bir eştir. İletkenlik ölçümü genellikle çevrimiçi (online) sensörlerle sürekli yapılır. Eğer iletkenlik değeri yükselmeye başlarsa, bu suya iyonik bir kontaminant karıştığını veya sistemde iyon değiştirici reçinelerin doygunluğa ulaştığını gösterebilir. Örneğin, bir membran sisteminde ani iletkenlik artışı, RO/EDI performansının düştüğünü veya bir valf kaçağı ile ham suyun karıştığını düşündürür. Böyle bir durumda ilgili ekipman kontrol edilir, gerekli ise sistem durdurularak bakım yapılır.
Toplam Organik Karbon (TOC)
TOC, suda çözünmüş organik maddelerin toplam miktarını (karbon cinsinden) ifade eder. Organik kirleticiler (örneğin mikrobiyal metabolitler, biyofilm kaynaklı organikler veya kaynak sudan gelen organik kirlilik) WFI’da istenmez, çünkü mikroorganizma üremesini teşvik edebilir veya ürünün saflığını bozabilir. USP ve EP, WFI için TOC değerinin en fazla 0.5 mg/L (500 ppb) olmasını şart koşar. TOC ölçümü genellikle online analizörler ile sürekli veya periyodik yapılır; bu cihazlar sudaki organik içeriği oksidasyon ve spektrofotometrik yöntemlerle tespit eder. TOC seviyesinde bir artış gözlemlenirse, bu organik bir kontaminasyon belirtisidir. Örneğin, sistemde bir plastik aksam bozulup organik salınım yapıyor olabilir veya filtreler etkin çalışmıyordur. Böyle durumlarda suyun kullanımının durdurulup sebebin araştırılması, gerekirse tank ve hatların kimyasal temizliği gibi önlemler alınması gerekir.
Mikrobiyolojik Yük (Biyoburden)
WFI’ın mikrobiyolojik kalitesi, doğrudan hasta güvenliğini etkilediğinden kritik önemdedir. Farmakopelerde enjeksiyonluk sular için spesifik bir canlı mikroorganizma üst sınırı belirtilmiştir. Genel kabul, 100 mL WFI örneğinde toplam aerobik bakteri sayısının 10 koloni oluşturan birimden (CFU) az olması gerektiğidir. Yani 100 mL’lik bir numunede en fazla <10 CFU üreyebilir. İyi bir WFI sisteminde pratikte bu değer çoğunlukla 0 veya tespit edilemeyecek kadar düşük çıkar. Ayrıca farmakope testleri gereği E. coli, Salmonella, P. aeruginosa, S. aureus gibi patojen mikroorganizmalar WFI’da hiç bulunmamalıdır. Mikrobiyolojik kontrol, genellikle günlük veya belirli aralıklarla numune alınıp petri kaplarında kültür yapılarak gerçekleştirilir. Sonuçlar, inkübasyon sonrası koloni sayımı ile değerlendirilir. Eğer herhangi bir numunede CFU sayısı limitleri aşarsa veya patojen üremesi saptanırsa, bu alarm durumudur. Derhal ilgili su sistemi durdurulmalı, kök neden analizi yapılarak (örneğin bir valf kontaminasyonu mu, filtre arızası mı, depo havalandırma filtresi yetersiz mi vb.) sorun bulunmalıdır. Düzeltici olarak sistemin kapsamlı sanitizasyonu (sıcak suyla veya kimyasal dezenfeksiyonla) ve gerekli onarımlar yapılır, ardından ardışık testlerle su kalite normlarına dönene kadar üretim suyu kullanılmaz.
Bakteriyel Endotoksin (Pirojen) Seviyesi
Endotoksinler, Gram-negatif bakterilerin hücre duvarından salınan ve insanlarda ateş tepkisine yol açabilen toksik maddelerdir. WFI’nın endotoksin içeriği mililitre başına 0.25 Endotoksin Birimi’nden (EU/mL) düşük olmalıdır. Bu kriter, WFI’nın pratik olarak piröjenik olmaması gerektiğini ifade eder. Endotoksin testi, laboratuvarda LAL testi (Limulus Amebocyte Lysate) ile yapılır. Eğer endotoksin seviyesinde bir yükselme gözlenirse (örn. 0.25 EU/mL’nin üzerine çıkarsa), bu sistemde muhtemelen bakteriyel bir kontaminasyon olduğunun göstergesidir – zira canlı bakteriler olmasa bile ölü bakterilerin kalıntıları endotoksin olarak birikebilir. Böyle bir durumda yine su sistemi hemen gözden geçirilmeli, gerekirse tüm hatlar sıcak su buharıyla sterilize edilmeli ve tekrar testler yapılmalıdır. Endotoksin sorunu, özellikle soğuk çalışan WFI sistemlerinde durgun nokta kalmışsa veya filtreler uzun süre değiştirilmemişse ortaya çıkabilir, bu yüzden sürekli sirkülasyon ve periyodik filtre değişimi gibi uygulamalarla önlenmelidir.
Diğer Fiziksel-Kimyasal Parametreler
Yukarıdaki temel parametrelerin yanı sıra farmakope monograflarında WFI için bazı ek safiyet testleri de bulunur. Örneğin görünüm testi (renksiz, berrak ve partikülsüz olmalıdır), pH (genellikle 5.0–7.0 aralığında, ancak saf suda tamponlayıcı olmadığından bu test özel koşullarda yapılır) , ağır metaller (<0.1 ppm) ve belirli iyonların (klorür, amonyum, kalsiyum-magnezyum gibi) limit testleri farmakope gereklilikleri arasındadır. Bu testler, WFI üretiminde genellikle dönemsel analizlerle doğrulanır. Modern pratikte, iletkenlik ve TOC ölçümü aslında bu iyonik ve organik saflık testlerinin yerini büyük oranda almıştır; eğer bir WFI örneği düşük iletkenlik ve düşük TOC gösteriyorsa, ağır metal, klorür vb. safsızlıkların da zaten limitlerin altında olduğu kabul edilir. Yine de kalite güvence amaçlı, belirli periyotlarda bu ek parametreler laboratuvar analizleriyle teyit edilir.
Sonuçların Yorumlanması ve Aksiyonlar
WFI kalite kontrolünden elde edilen veriler, trend analizine tabi tutularak sürekli değerlendirilir. Örneğin iletkenlik veya TOC değerlerinde yavaş bir yükseliş trendi, sistemde bir bozulmanın yaklaştığını gösterebilir ve proaktif bakım planlamasını tetiklemelidir. Mikrobiyolojik sonuçlar ise “pas/fail” (uygun/uygun değil) şeklinde değerlendirilir ve en ufak bir uygunsuzlukta genellikle ürün güvenliği için su sistemi kullanım dışı bırakılarak devreye sokulmadan önce kapsamlı bir yeniden sanitizasyon ve validasyon süreci yürütülür. Her bir parametrenin kontrolü, birlikte ele alındığında suyun kimyasal ve mikrobiyolojik bütünlüğünü garanti eder. İyi bir WFI yönetiminde, alarmlı otomatik izleme sistemleri kullanılır; iletkenlik veya TOC gerçek zamanlı limit aşımında otomatik uyarı verir. Bu sayede operatörler hemen müdahale edebilir. Genel olarak, WFI sistemi operasyonunda “kontaminasyon girmesin, girerse tespit edilsin, edildiğinde de ürüne ulaşmadan engellensin” prensibi geçerlidir.
Endüstride Kullanım Amaçları
WFI, saflığı ve güvenilirliği sayesinde pek çok endüstride kritik süreçlerin temelini oluşturur. Başlıca kullanım alanları ve amaçları şöyledir:
Farmasötik Üretim
İlaç endüstrisinde WFI, özellikle parenteral (enjeksiyon yoluyla uygulanan) ürünlerin formülasyonunda çözücü olarak kullanılır. Enjeksiyonluk çözeltiler, serumlar, aşılar, intravenöz infüzyon sıvıları, göz damlası gibi steril preparatlar hazırlanırken etkin madde ve yardımcı maddeler WFI içinde çözünür. Örneğin bir antibiyotik tozunun enjeksiyon öncesi çözündürülmesinde veya bir kemoterapi ilacının serum fizyolojik içinde seyreltildiği durumda, kullanılan su WFI kalitesinde olmalıdır. WFI kullanımı, bu ürünlerin hasta vücuduna güvenle verilebilmesini sağlar. Ayrıca farmasötik ham madde üretiminde (API üretimi) son safhalarda kristallendirme, yıkama veya seyreltme adımlarında WFI tercih edilerek üründe istenmeyen iyon veya mikrop kalıntısı kalması önlenir.
Aseptik ve Biyoteknolojik Prosesler
Biyoteknoloji sektöründe üretilen birçok ürün (monoklonal antikorlar, protein biyofarmasötikler, aşılar vb.) parenteral olarak uygulanır. Bu nedenle biyoteknolojik üretim süreçlerinde de WFI hayati önemdedir. Hücre kültürü ortamlarının hazırlanmasında çoğunlukla saf su kullanılır; eğer nihai ürün insanlara enjekte edilecekse ortam hazırlığında bile WFI kullanılması tercih edilebilir. Downstream (aşağı akış) saflaştırma proseslerinde buffer (tampon) çözeltileri, kromatografi elüsyon sıvıları WFI ile hazırlanarak, süreç boyunca kontaminasyon riskinin artması engellenir. Ayrıca fermentör, biyoreaktör gibi ekipmanların temizliğinde WFI yıkaması yapılması, residual mikropların yok edilmesi ve endotoksin birikiminin önlenmesi açısından yaygın bir uygulamadır. Biyoteknolojik ilaç üretiminde WFI adeta bir “çığır açıcı” ham madde olup, ürün saflığını ve kararlılığını doğrudan etkiler.
Ekipman Temizliği ve Sterilizasyon
Hem klasik farmasötik üretimde hem de biyoteknolojide, üretim ekipmanlarının temizliği kritik bir adımdır. Biyoreaktörler, karıştırma tankları, boru hatları, dolum makineleri gibi ürünle temas eden ekipman yüzeyleri, işlem sonlarında veya ürün değişimlerinde WFI ile durulanır. WFI’nin iyon ve mikroorganizma içermemesi, temizlik sonrasında ekipman yüzeyinde hiçbir kalıntı veya biyolojik yük bırakmamasını sağlar. Özellikle CIP (Clean-in-Place) sistemlerinde son durulama aşamasında WFI kullanımı yaygındır. Yine, sterilizasyon öncesi otoklava konulacak malzemelerin (şişe, kapak, araç-gereç) üzerindeki kimyasal kalıntıları arındırmak için WFI ile durulama yapılır. Bu sayede sterilizasyon sırasında kalıntıların pirolize olup ürünlere bulaşması önlenir. Lyofilizat (dondurarak kurutma) üretiminde de ürüne eklenecek su WFI olmak zorundadır, çünkü kurutma sonrası bile geride kalabilecek iyonlar ürün stabilitesini bozabilir.
Tıbbi Cihaz ve Sağlık Hizmetleri
WFI, yalnızca ilaç değil, tıbbi cihaz ve hastane uygulamalarında da kullanılmaktadır. Örneğin, implantasyon öncesi tıbbi implantlar veya cerrahi aletler WFI ile durulanarak üzerlerinde hiçbir pirojenik kalıntı kalmaması sağlanır. Diyaliz solüsyonlarının hazırlanmasında veya hemofiltrasyon sıvılarının üretiminde WFI kullanımı esastır. Hastanelerde, steril sulandırma gerektiren ilaç tozları (enjektabl antibiyotik flakonları gibi) kullanıma sunulan steril WFI ampulleri ile çözülür. Göz ve doku irrigasyon solüsyonları WFI’dan hazırlanır. Tüm bu örneklerde, WFI’nın yüksek saflığı hastaya uygulanacak son üründe toksik veya enfeksiyöz reaksiyon riskini sıfıra indirmeyi hedefler.
Analitik ve Araştırma Amaçları
WFI, aynı zamanda laboratuvar ortamlarında hassas analizler veya araştırma amaçlı deneyler için de tercih edilen bir çözücüdür. Örneğin, ilaç kalite kontrol laboratuvarlarında referans çözeltilerin ve reaktiflerin hazırlanmasında WFI kullanmak, analiz sonuçlarının güvenilirliğini artırır. Biyolojik araştırmalarda, özellikle endotoksine duyarlı in vitro deneylerde (örneğin primer hücre kültürleri, LAL testi için reaktif hazırlığı vb.) WFI kullanımı, spurious (yanıltıcı) sonuçların önüne geçer. Bununla birlikte, WFI üretimi maliyetli olduğundan, laboratuvarlarda çoğu zaman yüksek saf su sistemlerinden elde edilen “ultrapure” su da kullanılır; ancak en kritik biyolojik testlerde WFI tercih edildiği olur.
Özetle, WFI farmasötikten biyoteknolojiye, tıbbi cihazdan klinik uygulamalara kadar birçok alanda “güvenli su” rolünü üstlenir. Onun varlığı, ürün ve tedavilerin güvenilir olmasını, yokluğu ise ciddi risklerin ortaya çıkmasını sağlar. Bu yüzden endüstride WFI, sadece bir ham madde değil, aynı zamanda bir kalite standardı olarak değerlendirilir.
Tasarım ve Uygulama Kriterleri
WFI sistemlerinin tasarımı, ürün kalitesini koruyacak şekilde hijyenik mühendislik prensiplerine uygun olmalıdır. Uygulamada bir WFI üretim, depolama ve dağıtım sistemini planlarken dikkate alınması gereken başlıca kriterler şunlardır:
Malzeme Seçimi ve Yüzey Özellikleri
WFI ile temas eden tüm yüzeyler, yüksek derecede korozyon dirençli ve inert malzemeden olmalıdır. Genellikle tercih AISI 316L paslanmaz çeliktir. 316L, düşük karbon içeriğiyle kaynak sonrası duyarsızlaşmaya karşı direnç gösterir ve klorür korozyonuna karşı dayanıklıdır. Yüzey finişi çok önemlidir: İç yüzeylerin pürüzsüzlüğü bakterilerin tutunmasını zorlaştırır. Bu nedenle WFI boru ve tanklarının iç yüzeyleri elektropolisajla parlatılarak genellikle Ra ≤ 0.5 mikron yüzey pürüzlülüğü sağlanır. Yüksek kaliteli paslanmaz çelik malzeme aynı zamanda rouging adı verilen oksitlenme probleminin de minimize edilmesini sağlar. Borularda kullanılan conta, gasket gibi elemanlar teflon veya silikondan yapılmış, USP Class VI uyumlu gıda-tıp sınıfı malzemeler olmalıdır ki suya herhangi bir çözünür madde salmasın.
Depolama Tankı Tasarımı
WFI genelde sürekli üretilip bir denge tankında depolanır. Bu tankların tasarımında öne çıkan husus, steril bariyerlerin sağlanması ve suyun durağan kalmamasıdır. Tank genellikle atmosferik basınçta çalışır ancak tepesinde 0.22 µm hydrophobic hava filtresi bulunur; böylece tank içine giren hava sterilize edilir ve dış ortamdan mikroorganizma bulaşması önlenir. WFI tankları çoğu zaman çift cidarlı veya ısı ceketi ile donatılır, çünkü suyun istenen sıcaklıkta tutulması gerekir. Sıcak WFI sistemlerinde tank suyu devamlı ~80°C’de tutulur. Bu, biyofilm oluşumunu önleyen önemli bir faktördür. Tank içi sıcaklık kontrolü için buhar ceketine bağlı bir PID kontrol sistemi kullanılır. Ayrıca tank içinde karanlık/ölü köşe kalmaması için spray-ball (püskürtme topu) bulunur; geri dönen sıcak WFI, bu spray-ball aracılığıyla tankın iç yüzeylerine püskürtülerek sürekli ıslak ve sıcak kalmaları sağlanır. Bu tasarım, tank içinde herhangi bir noktada mikrobiyal üreme olmaması için kritik bir özelliktir. Tankın alt kısmı konik yapıda ve dip noktası çıkış nozuluna yönlendirilmiş olmalıdır ki tamamen drenaj sağlanabilsin.
Distribüsyon (Dağıtım) Sistemi
WFI üretim tankından kullanım noktalarına suyu ileten dağıtım hattı, genellikle halka (loop) şeklinde kapalı devre tasarlanır. Bir sirkülasyon pompası yardımıyla su bu halka içinde sürekli dolaştırılır. Böylece su bayatlamaz ve her an istenen kalitede kalır. Dağıtım boruları mümkün olduğunca kısa ve kesintisiz olmalı, kaynaklı birleştirmeler oransal kaynak (orbital welding) ile yapılmalı ve iç yüzeyde çapak, girinti bırakılmamalıdır. Boru güzergahı tasarlanırken eğim verilerek (genellikle %1 eğim, yani 1:100 kuralı) düşük noktalardan tam drenaj imkanı yaratılır. Bu, temizleme veya bakım için sistemi boşaltırken su birikintilerinin kalmamasını sağlar. Ayrıca sirkülasyon yönü ve vanaların konumları ayarlanarak her kullanım noktasının düzenli akış aldığı bir hidrolik denge sağlanır. Akış hızı kritik parametrelerden biridir: Tipik olarak borularda ~1.5 m/sn (5 ft/sn) civarı bir lineer hız hedeflenir. Bu hız, boru içinde türbülans yaratarak biyofilm birikimini zorlaştırır ve homojen sıcaklık dağılımını destekler. Dönüş hattındaki akış hızı da en az 1 m/sn civarında tutulur ki su her noktada hareketli olsun.
Ölü Hacimlerin ve Ölü Bacakların Önlenmesi
WFI loop tasarımında “dead leg” denilen, akışın durgun kaldığı boru çıkıntılarından kaçınmak hayati önemdedir. Genel endüstri standardı, bir kullanım vanası veya ölçüm probu için ana hattan çıkan herhangi bir boru parçasının uzunluğunun iç çapının 6 katından (6D kuralı) fazla olmamasıdır. Örneğin ana hattın çapı 2 cm ise, bu hattan çıkan durgun kol uzunluğu 12 cm’yi geçmemelidir. Bu kural, suyun akmadığı kör uçlarda bakteri üreme riskini minimize etmek içindir. Kullanım noktası vanaları için sıfır ölü hacimli valfler (zero-dead-leg diaphragm valve) tercih edilir; bu özel vanaların tasarımı, kapalı konumda bile suyun vana girişinde durgun cep bırakmamasını sağlar. Ayrıca sensör portları, numune alma noktaları gibi tüm eklentiler akış yönünü bozmadan minimal ölü hacim yaratacak şekilde konumlandırılır. Sistem durdurulduğunda veya uzun süre kullanılmadığında, tüm hatların komple drenajı ve kuruması sağlanabilmelidir; bu yüzden düşük noktalarda drenaj vanaları bulunur.
Pompa ve Vana Seçimi
Sirkülasyon pompası, paslanmaz çelikten imal, hijyenik tasarımlı santrifüj pompa olmalıdır. Pompa sızdırmazlık elemanları (mechanical seal) suya kontaminant eklemeyecek şekilde seçilir; bazı sistemlerde manyetik kaplinli pompa kullanılarak, salmastradan gres vb. bulaşma riski ortadan kaldırılır. Kullanım noktalarındaki vanalar genellikle diyaframlı hijyenik vanalar olup, ürünle temas eden aksamları PTFE/teflon diyafram ve çelik gövdeden oluşur. Bu vanaların temizliği CIP ile kolaydır ve ölü hacim bırakmaz. Tüm vanalar ve bağlantı elemanları, sterilizasyona dayanıklı olmalıdır; zira periyodik olarak 80°C su veya buhar verildiğinde contalar erimemelidir. Gerektiğinde otomatik (pnömatik veya elektromotorlu) vanalar kullanılarak sistem CIP/SIP süreçlerinde uzaktan kumanda edilebilir.
Isıtma/Soğutma ve Sıcaklık Kontrolü
Eğer sistem sıcak WFI olarak tasarlandıysa, hem depo tankında hem de dağıtım loopunda suyun sıcaklığını ~80°C’de tutmak için ısıtma düzeni olmalıdır. Tank ceketine buhar verilirken, loop içinde suyun soğumaması için borular gerekirse ısı izlemeli (heat-traced) ve yalıtımlı yapılır. Alternatif olarak, depo tankından çıkan su bir eşanjörden geçirilerek 80°C civarında dolaştırılır. Kullanım noktasında WFI gerektiğinde, eğer su çok sıcak ise anında soğutmak için point-of-use öncesi küçük bir eşanjör (genellikle çift borulu veya plakalı ve steril) kullanılabilir. Soğuk WFI sistemlerinde ise, suyu sürekli sıcak tutmak yerine periyodik sanitizasyon yapılır; örneğin günde bir defa loop suyu 80-85°C’ye kadar ısıtılarak 1 saat sirküle edilir ve sonra tekrar soğutulur. Bu da bir tasarım tercihi olup, sistemin ekipmanları (ör. membranlar, contalar) sıcaklığa dayanıklı seçilerek uygulanır. İster sıcak ister soğuk olsun, tüm WFI dağıtım hatlarında sıcaklık sensörleri, iletkenlik sensörleri, akış ölçerler stratejik noktalara yerleştirilir ve merkezi bir PLC/SCADA sistemine bağlanır. Bu sayede suyun parametreleri anlık izlenir ve kontrol altında tutulur.
Otomasyon ve İzleme
Modern WFI sistemleri tam otomasyonla çalışır. Depo seviye kontrolü, pompa hız kontrolü, sıcaklık ve basınç kontrolü PLC üzerinden programlanmıştır. Örneğin tank seviyesi düşünce sistem otomatik üretim moduna geçer, seviye dolunca distilasyon veya arıtma durur. Loop basıncı ve akışı sürekli ölçülür; bir kullanım vanası açıldığında düşen basıncı telafi için pompa frekansı artar vb. Ayrıca iletkenlik ve TOC analizörleri online olarak su kalitesini izler ve eğer herhangi bir değer eşik değeri aşarsa alarm üretilir. Bu tip otomasyon, insan hatasını en aza indirir ve tutarlı kaliteyi sağlar. Tüm kritik veriler kayıt altına alınarak kalite güvencesi için saklanır (21 CFR Part 11 uyumlu veri bütünlüğü esas alınarak).
Temizlik ve Sterilizasyon Dizaynı
Bir WFI sistemi, kullanımda değilken veya rutin aralıklarla sterilize edilebilmelidir. Bu amaçla tasarımda SIP (Steam-in-Place) noktaları bırakılır. Saf buhar üreteci (clean steam generator) vasıtasıyla depoya ve dağıtım hattına doymuş buhar verilip tüm sistem 121°C’de sterilize edilebilir. Alternatif olarak, 80-90°C sıcak suyla pasteürizasyon da yaygın bir yöntemdir. Hatta bazı sistemler kimyasal sanitizasyon (ör. ozonlama veya perasetik asit dolaştırma) ile de temizlenebilir. Önemli olan, sistem tasarlanırken bu işlemlerin kolaylıkla yapılabilmesi (örneğin tüm elemanların bu sıcaklıklara dayanıklı olması, uygun bağlantı noktalarının bulunması) ve sonrasında sistemin kolayca durulanıp servise alınabilmesidir. Depo tanklarında ve uzun hatlarda hava cepleri kalabileceğinden, buhar sterilizasyonunda havalandırma ventleri ve kondens drenaj noktaları uygun yerlere konulur.
Sonuç olarak, WFI sistem tasarımı, hijyenik tasarım prensiplerinin mühendislik ile buluştuğu bir alandır. İyi tasarlanmış bir sistem; ölü hacimleri minimize edilmiş, uygun malzemeler kullanılmış, otomasyonu sağlam, temizlenebilir ve sürekli güvenilir su sağlayan bir sistemdir. Bu sayede WFI, üretim proseslerinde bir risk unsuru değil, güven unsuru olarak işlev görür.
Olası Problemler ve Çözüm Önerileri
En iyi tasarlanmış ve işletilen sistemlerde bile zaman zaman sorunlar yaşanabilir. WFI sistemlerinde karşılaşılan olası problemler ve bunlara yönelik çözüm stratejileri şu şekilde özetlenebilir:
Mikrobiyal Kontaminasyon Riski
WFI sistemlerinin en büyük düşmanı, istenmeyen mikroorganizma üremesidir. Özellikle durgun su bölgeleri veya yetersiz sanitizasyon, bakteri kolonilerinin oluşmasına yol açabilir. Bu durum sadece suyun mikrobiyolojik yükünü artırmakla kalmaz, aynı zamanda bakterilerin ölmesiyle ortaya çıkan endotoksin seviyesini de yükseltir. Çözüm olarak, tasarım aşamasında ölü hacimleri minimize etmek ilk adımdır (6D kuralının uygulanması vb.). İşletme aşamasında ise düzenli sıcak su sanitizasyonu veya buhar sterilizasyonu yapılmalıdır. Örneğin her hafta sonu sistemin 80°C’de 2 saat sirküle edilmesi, çoğu biyofilm oluşumunu engeller. Soğuk çalışan sistemlerde ozon ile suyun sürekli düşük doz dezenfeksiyonu uygulanabilir; ozon kalıntısı da ürün kullanılmadan önce UV ışık ile nötralize edilebilir. Ayrıca periyodik olarak tüm vanaların ve uç noktaların açılıp bir miktar suyun drenaj edilmesi (“flush”) önerilir, bu sayede buralarda birikme olmaz. Mikrobiyal kontaminasyon riskini tamamen ortadan kaldırmak mümkün olmasa da, sürekli izleme (rutin numune alıp ekim yapma, hızlı mikrobiyolojik testler) ile en erken safhada tespit edilip müdahale edilebilir. Eğer bir kontaminasyon olayı tespit edilirse, ilk yapılacaklar: Sistemde kapsamlı bir SIP (buharla sterilizasyon) uygulamak, ilgili filtreleri değiştirmek, kontaminasyon kaynağını (örneğin arızalı bir contayı veya açık unutulmuş bir vanayı) belirleyip düzeltmektir. Ardından, su tekrar spesifikasyonlara dönene kadar üretim amaçlı kullanılmamalıdır.
Endotoksin Birikimi
Yukarıdaki maddeyle bağlantılı olarak, bazı durumlarda suyun mikrobiyolojik testleri temiz çıkmasına rağmen endotoksin seviyeleri yükselebilir. Bu genellikle geçmişte oluşmuş bir biyofilm veya ölmüş bakterilerin kalıntılarının sisteme yerleşmiş olmasından kaynaklanır. Örneğin, bir dönemde yetersiz sanitizasyon yapılmışsa, boru iç yüzeylerinde bakteriyel biyofilm oluşup sonra ölebilir; geride LPS (lipopolisakkarit) endotoksinleri kalır. Bu endotoksinler normal kültür testlerinde görünmez ama LAL testinde ortaya çıkar. Endotoksin problemi yaşanmaması için en iyi yöntem, mikrobiyal üremeyi baştan önlemektir. Ayrıca, belirli aralıklarla sistemde “derin temizlik” yapmak yararlıdır: Yüksek pH’lı sıcak deterjan sirkülasyonu ve ardından düşük pH’lı asit sirkülasyonu yaparak biyofilm ve endotoksinler kimyasal olarak parçalanabilir. Bazı tesisler, yılda bir kez WFI sistemini devreden çıkarıp bu tür kimyasal temizleme ve sonrasında saf su ile yıkama işlemi uygularlar. Eğer endotoksin limiti aşılmışsa, kısa vadede çözüm suyu aktif karbon+ultrafiltrasyon gibi ekstra bir hattan geçirerek endotoksini süzmektir; ancak esas çözüm, sistemin kökten sterilizasyonu ve gerekiyorsa etkilenen komponentlerin (örneğin biyofilm tutmuş bir boru parçası) yenilenmesidir.
Ekipman Arızaları ve Sızıntılar
WFI sistemleri, pompalar, ısı eşanjörleri, sensörler, vanalar gibi çeşitli ekipman içerir. Zamanla bu ekipmanlarda arızalar olabilir. Örneğin, bir sirkülasyon pompasının salmastrası aşınırsa yağ sızıntısı suya karışabilir veya bir ısı eşanjöründe çatlak oluşursa ısıtma tarafındaki buhar/kızgın su ürüne karışabilir. Bu tip arızalar suyun kalitesini bozacak yabancı madde karışımlarına yol açabilir. Bu nedenle periyodik bakım şarttır: Pompa salmastraları belli saat çalışma sonunda yenilenir, eşanjörler düzenli basınç testine tabi tutulur, sensör kalibrasyonları altı ayda bir yapılır. Ayrıca proaktif olarak bazı parçalar ömürleri dolmadan değiştirilir (örneğin diyaframlı vanaların elastomerik diyaframları yılda bir yenilenir). Yedekli kritik ekipman kullanmak da güvenilirliği arttırır; örneğin tek pompa yerine ikiz pompa (biri yedek) konulması, arıza anında sistemin durmasını engeller. Sızıntı riski olan yerlere drip pan (damla tepsisi) ve algılama sensörleri konularak olası bir sızıntıda sistemin alarm vermesi sağlanır.
Kontrol Sistemi ve İzleme Problemleri
Otomasyon her ne kadar faydalı olsa da, hatalı sensör okumaları veya PLC arızaları yanıltıcı olabilir. Örneğin iletkenlik probu kirlendiğinde gerçekte saf olan suyu iletken göstermeye başlayabilir. Bu durumda operatör gereksiz yere panik yapabilir veya tam tersi, arızalı sensör düşük gösterirse kontaminasyonu fark etmeyebilir. Bu yüzden sensör kalibrasyonu düzenli yapılmalı, kritik parametrelerde birden fazla sensörle çapraz kontrol sağlanmalıdır (örneğin depoda ve loop dönüşünde iki iletkenlik sensörü gibi). PLC/SCADA sisteminde oluşabilecek bir yazılım hatasına karşı, kritik valf ve pompalar manuel modda da işletilebilir şekilde tasarlanmalıdır. Veri kayıt sistemlerinde kesinti olmaması için UPS ve veri yedeklemesi uygulanır. Operatörler de olası alarm durumlarında ne yapacakları konusunda eğitilmiş olmalıdır; mesela iletkenlik alarmı alındığında hemen bir numune alıp laboratuvarda test ederek sensörü doğrulama yoluna gitmek gibi prosedürler oluşturulmalıdır.
Korozyon ve Materyal Sorunları
WFI saf olduğundan paradoksal biçimde paslanmaz çelik üzerinde koruyucu oksit tabakasını çözebilir, bu olaya “rouge” denir. Rouge, sisteme hafif bir pas kızıllığı verebilir ve uzun vadede endotoksin kadar olmasa da partiküler kontaminasyona neden olabilir. Bunu önlemek için paslanmaz yüzeyler iyi pasifleştirilmelidir (asit ile pasifleştirme işlemi imalat ve bakım sonrası yapılır). Eğer rouge oluşumu gözlenirse (filtrelerde turuncu kalıntı vs.), sistem planlı bir şekilde durdurulup sitrik asit gibi kimyasallarla temizlenerek yeniden pasifleştirilir. Öte yandan, farklı metal veya alaşımların bir arada kullanımı (galvanik korozyon riski) kaçınılması gereken bir durumdur; tasarımda mümkün mertebe tek tip malzeme (316L SS) kullanılır. Yine de contalar veya bazı ölçüm cihazları gibi parçalarda farklı malzemeler varsa, bunların suya ekstraksiyon yapmadığı testlerle doğrulanmalıdır.
Depolama ve Taşıma Sırasında Bozulma
WFI çoğunlukla üretildiği yerde tüketilir, ancak bazı durumlarda tankerlere doldurularak başka bir tesise taşınması gerekebilir veya ambalajlanarak (ampul, şişe formunda steril WFI) dağıtılabilir. Dökme halde WFI taşıma sırasında büyük risk altındadır çünkü tanker içinde sirkülasyon ve ısı kontrolü sınırlıdır. Tankerle taşıma gerekiyorsa, tanker mutlaka önceden temizlenip sterilize edilmiş olmalı, mümkünse 70-80°C’de yalıtımlı tutulmalı ve varışta hemen boşaltılmalıdır. Taşıma süresi mümkün olduğunca kısa olmalıdır. Tankerin hava boşluğu da 0.2 µm filtreli olmalı, hatta bazı durumlarda inert gaz (azot) basılması pratik edilir. Ambalajlı steril WFI ise üretildikten sonra genellikle otoklavlanır veya aseptik olarak doldurulur. Bu ürünler açıldıktan sonra hızla kullanılmalıdır; zira açılan ampul/flakon çevreyle temas ettiği anda sterilitesini yitirir ve kısa sürede mikrop üreyebilir. Depolama konusunda, eğer WFI üretildikten sonra uzun süre tankta bekletilecekse, sıcak tutmak ve sürekli devridaim ettirmek dışında, ozonlama gibi yöntemler de kullanılır. Bazı tesisler, gece saatlerinde WFI döngüsüne düşük konsantrasyonlu ozon gazı enjekte eder ve sabah UV ile ozonu parçalarak suyu tekrar ozonsuz hale getirir. Bu şekilde su kullanılmazken bile mikropsuz kalır.
Bakım ve Validasyon Süreçleri
WFI sistemleri, GMP (İyi İmalat Uygulamaları) kapsamında kritik tesis ekipmanı olarak kabul edilir ve düzenli olarak kalifiye/valide edilmelidir. Bu, hem başlangıçta kurulum aşamasında (IQ, OQ, PQ – Kurulum/İşletme/Performans Kalifikasyonları) yapılır, hem de yılda en az bir kez yeniden validasyon şeklinde sürdürülür. Validasyon kapsamında, sistemden ardışık günlerde örnekler alınarak tüm kritik parametrelerin (iletkenlik, TOC, mikrop, endotoksin) spesifikasyonlara uyduğu teyit edilir. Ayrıca çeşitli challenge testleri yapılır: Örneğin en uzak kullanım noktasından numune alıp mikrobiyal üremeye bakmak, veya sistem durduktan 24 saat sonra suyu örnekleyip bozulma olmadığını göstermek gibi. Bu testler başarılı oldukça sistem onaylı kalır. Bakım tarafında ise her bakım aktivitesi sonrası (mesela bir membran değişimi veya bir conta değişimi sonrası) küçük bir re-kalifikasyon yapılır; su kalitesinin etkilenmediği gösterilir. Eğitimli personel tarafından prosedürlere uygun bakım yapılması sağlanmalıdır, çünkü steril sistemlerde küçük bir hata (örneğin bir contanın yanlış takılması) büyük kontaminasyonlara yol açabilir. Yedek parça stokları kritik öğeler için bulundurulur, böylece arıza halinde sistem uzun süre kapalı kalmaz. Son olarak, her problem bir deviasyon olarak ele alınıp kök neden analizi ve düzeltici/önleyici faaliyet (CAPA) sürecine dahil edilmelidir. Bu yaklaşım, aynı sorunun tekrarlanmaması ve sistemin sürekli iyileştirilmesi için gereklidir.
Özetle, WFI sistemlerinde sorunları tamamen sıfıra indirmek pratikte zordur, ancak proaktif bakım, sıkı izleme ve doğru mühendislik uygulamaları ile riskler yönetilebilir düzeyde tutulur. Bu sistemler canlı bir organizma gibi düşünülmeli; düzenli ilgi ve bakım ile sağlıklı kalmaları sağlanmalıdır. Beklenmedik bir sorun çıktığında da hızlı teşhis ve doğru müdahale ile ürün kalitesine zarar gelmeden süreçler devam ettirilir.
Uluslararası Standartlar ve Regülasyonlar
Enjeksiyonluk suyun üretimi ve kalitesi, uluslararası farmakopeler ve düzenleyici kurumlar tarafından sıkı standartlara bağlanmıştır. Başlıca referans alınan standartlar Amerika Birleşik Devletleri Farmakopesi (USP), Avrupa Farmakopesi (EP), Japon Farmakopesi (JP) gibi belgeler ile FDA ve EMA gibi otoritelerin kılavuzları, ayrıca WHO (Dünya Sağlık Örgütü) gibi kuruluşların önerileridir. Bu standartların genel amaçı, hangi koşullarda üretilirse üretilsin, dünyanın her yerinde WFI kalitesinin belli bir minimum güvenlik eşiğinin üzerinde olmasını sağlamaktır.
Farmakopeler Arası Uyumluluk
USP, EP ve JP gibi büyük farmakopeler günümüzde WFI konusunda büyük ölçüde harmonize olmuştur. Üç farmakope de WFI’nın kimyasal saflık kriterleri (iletkenlik ≤1.3 µS/cm @25°C, TOC ≤0.5 mg/L) ve mikrobiyolojik kriterleri (≤10 CFU/100 mL, endotoksin <0.25 EU/mL) konusunda aynıdır. Örneğin USP <1231> bölümünde ve ilgili monografında, WFI’nın saflaştırılmış sudan daha sıkı mikrobiyal sınırlara tabi olduğu belirtilir ve endotoksin limiti verilir. EP de "Aqua ad iniectabilia" monografisinde benzer şekilde WFI’nın endotoksin testini geçmesini şart koşar. Geçmişte farklılık gösteren en önemli husus, üretim yöntemiyle ilgili gerekliliklerdi: USP uzun süredir WFI’nın “distilasyon veya eşdeğeri bir yöntemle” üretilmesini kabul ederken EP sadece distilasyonu şart koşuyordu. 2017 itibariyle EP monografı revize edilerek, “distilasyona eşdeğer saflıkta su üreten membran teknolojilerinin” de WFI için kullanılabileceği ifade edildi. Bu değişiklik, global harmonizasyon adına atılmış önemli bir adımdı ve Japon Farmakopesi gibi diğer birçok farmakope de bu çizgiyi izlemektedir. Ancak Çin Farmakopesi gibi bazı bölgesel standartlar hala yalnızca distilasyona izin verebilmektedir (2017 itibariyle durum böyleydi). Bu nedenle, çok uluslu üretim yapan firmalar, ürünlerini hangi pazara sunacaklarsa o pazarın spesifik gerekliliklerini de göz önünde bulundurmalıdır.
USP (Amerikan Farmakopesi)
USP, WFI’yı saf suyun özel bir alt sınıfı olarak tanımlar ve steril olmaksızın fakat çok düşük biyobiyükte olması gerektiğini belirtir. USP’de WFI için çevrimiçi iletkenlik test limitleri ve laboratuvar TOC test prosedürleri detaylandırılmıştır. Ayrıca USP <1231> Water for Pharmaceutical Purposes rehber dokümanında, WFI sistemlerinin tasarım, operasyon ve validasyonuna dair iyi pratikler anlatılır. USP, üretim yöntemi olarak distilasyonun yanı sıra diğer yöntemleri de şarta bağlı kabul ettiğinden bahseder (eşdeğer veya üstün saflık sağlayan yöntemler, örneğin çift pass RO+UF gibi). ABD’de denetimler genellikle FDA tarafından yürütülür ve FDA’nın 21 CFR 211.67, 211.84, 211.94 gibi maddelerinde farmasötik sulara dolaylı referanslar yapılır (örn. ekipman temizliğinde uygun su kullanımı). FDA ayrıca "Guide to Inspections of High Purity Water Systems" gibi kılavuzlarda, WFI sistemlerine dair denetim bakış açısını paylaşmıştır. Özetle, USP standartlarına uyum ve FDA beklentilerinin karşılanması, ABD piyasası için elzemdir.
EP (Avrupa Farmakopesi) ve EMA
EP, WFI tanımını benzer şekilde yapar; ek olarak geçmişte “Highly Purified Water (HPW)” adıyla bir ara kategori tanımlamıştı. HPW, distilasyon dışı yöntemlerle üretilen ve kimyasal olarak WFI saflığında fakat endotoksin açısından WFI’dan biraz daha esnek bir sudur. 2017’de EP, WFI monografisine membran yöntemlerini dahil edince HPW tanımının gerekliliği azaldı ve pratikte EP de USP ile aynı kalite parametrelerini tek bir WFI standardında birleştirmiş oldu. Avrupa İlaç Ajansı (EMA), EP’deki değişiklik sonrası bir Soru-Cevap dokümanı yayımlayarak bu yeni durumu açıklamıştır. EMA, özellikle membran sistemlerinde mikrobiyal proliferasyon riskine dikkat çekmiş ve firmaların robust bir risk yönetimi ile durumu ele almasını beklediğini vurgulamıştır. Avrupa Birliği GMP kılavuzu (EudraLex Volume 4, Annex 1 ve 2), steril ürünlerde kullanılacak suyun WFI olması gerektiğini şart koşar. Ayrıca ekipman temizlik validasyonunda da WFI kullanımının gerekliliğine işaret eder. AB’de farklı ülkelerin denetim otoriteleri (örneğin Almanya’da BfArM, Fransa’da ANSM vb.) EP ve EMA çizgisinde denetimler yapar. Birlik genelinde WFI üretim tesisi kuracak firmaların, yerel su kalitesi (örneğin belediye suyu özellikleri) ve EP gerekliliklerini birlikte değerlendirerek uygun sistemi seçmeleri beklenir.
JP (Japon Farmakopesi)
JP, WFI konusunda USP/EP ile tam uyumludur. Hatta Japonya Sağlık Bakanlığı, EP’deki değişikliği takip ederek 2017 sonrasında membran yöntemlerine izin vermiştir. JP’de WFI için “Şeker hastalığı enjeksiyonlarında çözücü olarak kullanılan su” şeklinde spesifik uygulama örnekleri dahi verilir. Mikrobiyal limitler ve endotoksin limiti USP ile aynıdır. Japon denetim sistemi, üreticilerin su kalitesini her kullanım öncesi veya sürekli izleme ile kontrol altında tutmasını ve kayıtlamasını ister. Ayrıca Japonya, elektronik kayıt konusunda erken adapte olan bir ülke olduğundan, WFI sistemlerinin otomasyon verilerinin izlenebilirliği müfettişlerce yakından incelenir.
WHO ve Diğer Standartlar
Dünya Sağlık Örgütü, kendi yayınladığı Uluslararası Farmakopede (International Pharmacopoeia) WFI için benzer tanımlar getirir. WHO ayrıca gelişmekte olan ülkeler için rehber dokümanlar hazırlar. Örneğin WHO Technical Report Series 970, Eki 2’de “Pharmaceutical Water” kılavuzu yer alır. Bu kılavuz, WFI’nın tercihen distilasyonla üretilmesini, ancak uygun şekilde valide edilirse alternatif teknolojilere de açık olunabileceğini belirtir. WHO, özellikle kaynakların kısıtlı olduğu bölgelerde bile parenteral üretim için WFI standardının taviz verilmez bir gereklilik olduğunu vurgular. Ayrıca ABD FDA, AB EMA ve PIC/S (Pharmaceutical Inspection Co-operation Scheme) üyeleri, su sistemi denetimlerinde ortak bir yaklaşım benimserler. PIC/S kılavuzları, çok uluslu kabul gördüğünden, WFI sistemlerinin validasyonu ve işletilmesinde yol göstericidir.
Regülasyonlara Uyum ve Uygunluk Şartları
WFI üreten ve kullanan tesislerin, bağlı bulundukları pazarın GMP gerekliliklerine uyumu zorunludur. Bu da pratikte şunları gerektirir:
Dokümantasyon: WFI sistemine dair tüm kalite kayıtlarının (tasarım onayı, IQ/OQ/PQ protokolleri, günlük izleme formları, deviasyon kayıtları, trend analizleri) eksiksiz tutulması.
Süreklilik: Belirlenen standartlara uygunluk yalnız kurulumda değil, işletmenin her gününde sağlanmalıdır. Bu da sürekli izleme ve periyodik test programlarının aksatılmadan uygulanması demektir.
Kalifikasyon/Validasyon: Yukarıda bahsedilen IQ/OQ/PQ süreçlerinin yanında, değişiklik kontrolü sistemi ile, WFI sisteminde yapılacak herhangi bir değişikliğin (ekipman değişimi, prosedür değişimi vs.) önce risk analizi, sonra yeniden kalifikasyon adımlarına tabi tutulması gerekir.
Personel Eğitim ve Farkındalık: WFI ile çalışan operatörlerin ve bakım ekiplerinin, hem suyun kritik bir ürün olduğunu hem de sistemin nasıl çalıştığını çok iyi anlamış olmaları gerekir. GMP eğitimlerinde WFI sistemlerinin özel yeri vardır; yanlışlıkla açık bırakılan bir vana veya uygunsuz bir numune alma işlemi bile suyun kalitesini bozabileceğinden, personel yaptığı işin önemini bilmelidir.
Güncel Kalma: Farmakope monografları zaman zaman revize olabilir. Örneğin USP, TOC ve iletkenlik testlerinin metodolojisinde değişiklik yapabilir veya EP yeni bir limit getirebilir. Firma olarak bu değişiklikleri takip edip kendi iç prosedürlerini güncellemek şarttır. Aynı şekilde, teknoloji ilerledikçe (örneğin çevrimiçi mikrobiyolojik izleme sistemleri gibi yenilikler çıktığında) firma imkanları elverdiğince bunları değerlendirmelidir.
Denetimlere Hazırlık: FDA veya yerel otoriteler tesis denetimine geldiğinde, WFI sistemi genellikle mercek altına alınır. Denetçiler, su sisteminin validasyon raporlarını, günlük sonuç trendlerini, alarm geçmişini, bakım kayıtlarını ayrıntılı inceler. Dolayısıyla, her zaman denetime hazır bir sistem ve kayıt düzeni bulundurmak gerekir.
Sonuç olarak, uluslararası standartlar WFI için ortak bir güvenlik paydası oluşturur: Hangi yöntemle üretilirse üretilsin, WFI belirlenen kimyasal ve mikrobiyolojik kriterleri karşılamalı ve üretildiği koşullar GMP ilkelerine uygun olmalıdır. Bu standartlar, dünya genelinde hasta güvenliğini korumayı hedefleyen asgari gerekliliklerdir. Endüstri profesyonelleri için görev, bu gereklilikleri kendi operasyonlarına en etkin biçimde uygulamak ve sürekliliğini sağlamaktır. WFI sisteminin tasarımından günlük işletimine kadar her adım, bu regülasyonlar çerçevesinde şekillenmeli ve "uygunluk" (compliance) kültürü ekip tarafından benimsenmelidir. Böylece, WFI kullanan nihai ürünlerin kalitesi ve güvenliği garanti altına alınmış olur.