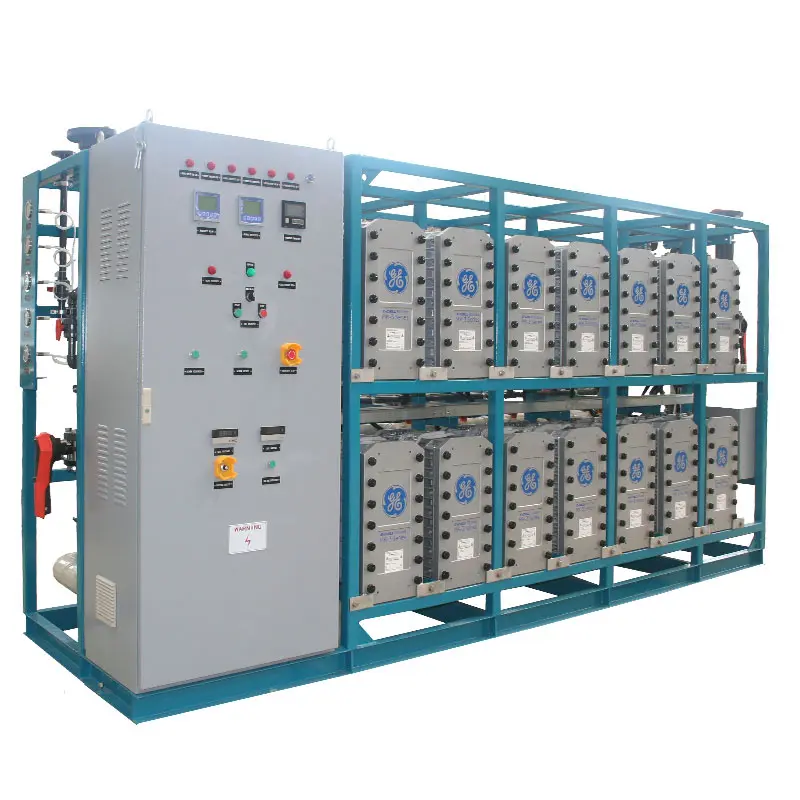
Elektrodeiyonizasyon (EDI)
Elektrodeiyonizasyon (EDI), kimyasal yenileme olmadan çözünmüş iyonları kaldırarak ultra saf su üreten ileri bir su arıtma teknolojisidir. İyon değişim reçineleri, seçici membranlar ve elektrik akımı kullanarak, EDI sistemleri etkili bir şekilde safsızlıkları ortadan kaldırır ve kritik uygulamalar için yüksek kaliteli su sağlar.
EDI teknolojisi, elektrik alanı tarafından yönlendirilen iyon değişim reçineleri ve membranlar kullanarak sudan çözünmüş tuzları uzaklaştırır. Bu süreç, kimyasal yenileyicilere olan ihtiyacı ortadan kaldırarak çevre dostu ve maliyet etkin bir seçenek sunar. Sürekli çalışması ve düşük bakım gereksinimleri ile EDI sistemleri güvenilir performans sağlar ve kesinti süresini en aza indirir.
EDI sistemleri, özellikle kazan beslemesi ve ultra saf durulama gibi yüksek saflıkta su gerektiren uygulamalar için, ilaç ve elektronik gibi endüstrilerde kritik bir rol oynamaktadır. Sıkı kalite standartlarını karşılama konusundaki güvenilirlikleri, modern su arıtımında tercih edilen bir seçenek olmalarını sağlamaktadır.
Elektrodeiyonizasyon (EDI) Ürün Serisi
İhtiyaçlarınıza yönelik tasarlanmış ürün gruplarımızı inceleyin
Laboratuvar Tipi Sistemler
Araştırma laboratuvarı uygulamaları için tasarlanmış elektrodiyonizasyon sistemleri.
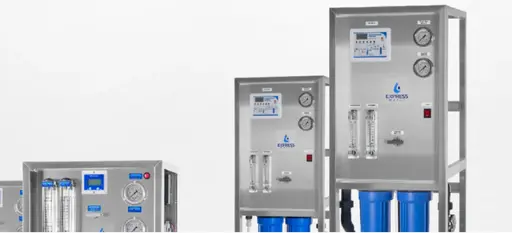
Özel Tasarım EDI Sistemleri
Endüstriyel uygulamalar için özel tasarlanmış elektrodiyonizasyon sistemleri.

Laboratuvar Tipi Elektrodeiyonizasyon Sistemleri
Mini Laboratuvar Tipi EDI Sistemleri
Elektrodeiyonizasyon (EDI) sistemleri, 1 l/saat ile 8 l/saat arasında bir kapasite yelpazesi sunarak, laboratuvar ortamlarının katı gereksinimlerini karşılayan olağanüstü saflıkta su üretmek için titizlikle tasarlanmıştır.
Maxi Laboratuvar Tipi EDI Sistemleri
Bu deiyonizasyon sistemleri, 10 l/saat ile 50 l/saat arasında değişen akış kapasitesi ile, laboratuvar faaliyetleri için yüksek saflıkta su sağlamak üzere olağanüstü verimlilik ve güvenilirlik ile tasarlanmıştır.
Endüstriyel Elektrodiyonizasyon (EDI) Sistemleri
Endüstriyel Elektrodeiyonizasyon (EDI) Serisi
Elektrodeiyonizasyon (EDI) sistemlerimiz, 0.25 m³/saat ile 50 m³/saat arasında değişen kapasiteleriyle, 20 MΩ'a kadar dirençte ultra saf su üretmek üzere tasarlanmıştır. Kompakt ve verimli olan bu sistemler, kesintisiz çalışma için tak-çalıştır çözümleri olarak özelleştirilebilir.
İhtiyaçlarınıza Özel Sistem Çözümleri
Özel gereksinimlerinizi karşılamak için geliştirilmiş çözümlerimizi keşfedin. İhtiyacınıza özel tasarlanmış sistem seçeneklerimizle su kalitesini ve sistem performansını artırın!
E-posta
Telefon
Adres
Akçaburgaz, 3026. Sk No:28, 34522 Esenyurt/İstanbul TURKEY
Su Arıtma için Elektrodeiyonizasyon (EDI)
Elektrodeiyonizasyon (EDI), iyon değişim reçineleri, iyon seçici membranlar ve bir DC elektrik alanının bir kombinasyonunu kullanarak yüksek saflıkta deiyonize su üreten gelişmiş bir su arıtma yöntemidir. Genellikle ters ozmozdan (RO) sonra bir parlatma adımı olarak kullanılır ve 15–18 MΩ·cm'ye kadar dirençler elde etmek için kalan iyonik kirleticileri temizler (ultra saf su kalitesi) . Asitler ve bazlarla periyodik kimyasal rejenerasyon gerektiren geleneksel karma yataklı iyon değiştiricilerin aksine, EDI sürekli olarak ve kimyasal reaktifler olmadan çalışır , çünkü elektrik alanı reçineleri yerinde sürekli olarak rejenerasyon yapar. Bu, EDI'yi "yeşil" bir teknoloji haline getirir , tehlikeli rejenerant kimyasalları ve atıkları ortadan kaldırır ve reçine rejenerasyonuyla ilişkili işletme maliyetlerini ve duruş süresini azaltır. EDI modülleri, sürekli çalışmaları nedeniyle genellikle CEDI (sürekli elektrodeiyonizasyon) sistemleri olarak adlandırılır. 1980'lerde geliştirilen ve 1980'lerin sonuna doğru ticarileştirilen EDI, yüksek saflıkta su gerektiren endüstrilerde yaygın olarak benimsenen kanıtlanmış bir teknoloji haline gelmiştir.
Elektrodeiyonizasyon (EDI) Nasıl Çalışır?
EDI, geleneksel elektrodiyaliz ve iyon değişimi prensiplerini tek bir işlemde birleştirir. Bir EDI cihazında, su, katyon ve anyon değişim membranları arasında sıkıştırılmış karışık yataklı iyon değişim reçinesiyle dolu bölmelerden akar. Yığın boyunca uygulanan bir DC voltajı, katyonların katoda, anyonların ise anoda doğru göç etmesine neden olur. İyon seçici membranlar, bu iyonları bitişik konsantre (reddetme) kanallarına yönlendirirken, reçine sürekli olarak iyonları değiştirir ve elektriksel olarak yenilenir. Esasen, EDI üç eş zamanlı olayı içerir:
İyon Değişimi: Seyreltik (ürün) bölmesinde iyon değişim reçineleri ile sudan iyonların uzaklaştırılması.
Elektro-göç (Elektrodiyaliz): İyonların elektrik alanı altında membranlardan ayrılarak, uzaklaştırılan iyonların konsantre bölmelerine taşınmasıdır.
Elektrokimyasal Rejenerasyon: Suyun ayrıştırılması yoluyla reçinenin yerinde rejenerasyonu – elektrik alanı suyun H⁺ ve OH⁻'ye ayrışmasına neden olur ve bu da reçinenin değişim kapasitesini sürekli olarak yeniden yükler.
EDI, bu aşamaları birleştirerek sürekli olarak saflaştırılmış deiyonize su üretir. Aşağıdaki bölümler, EDI sürecinin her aşamasının ayrıntılı bir açıklamasını, izlenecek çalışma parametrelerini, tipik olarak çıkarılan kirleticileri, uygulamaları ve EDI sistemleri için önemli tasarım, operasyonel ve bakım hususlarını sağlar.
Elektrodeiyonizasyon/EDI Süreci ve Aşamaları
İyon seçici membranlar (CEM = katyon değişim membranı, AEM = anyon değişim membranı) arasında iyon değişim reçine boncukları (karışık katyon ve anyon reçineleri) bulunan bir elektrodeiyonizasyon hücre çiftinin şeması. Uygulanan bir DC elektrik alanı (solda pozitif anot, sağda negatif katot) katyonları (+) katyon-geçirgen seçici membranlar aracılığıyla katoda doğru ve anyonları (–) anyon seçici membranlar aracılığıyla anoda doğru konsantre ("reddetme") odalarına doğru iter. Bu sürekli iyon giderimi, merkezi (seyreltme) odada deiyonize ürün suyu verir.
EDI modülleri tipik olarak birçok "hücre çifti"nden oluşan yığınlar olarak inşa edilir, her çift bir seyreltme bölmesinden (seyreltilmiş veya ürün odası olarak da adlandırılır) ve iyon seçici membranlarla ayrılmış bir yoğunlaştırma bölmesinden (yoğunlaştırma veya reddetme odası) oluşur. Her seyreltme bölmesi katyon ve anyon değişim reçinesinin karışık bir yatağıyla doldurulur. Elektrik alanını oluşturmak için yığının her iki ucuna bir anot ve katot yerleştirilir. Besleme suyu (genellikle RO permeatı) seyreltme odalarına verildiğinde ve bir DC voltajı uygulandığında, EDI işlemi aşağıdaki aşamaları içerir:
İyon Değişimi (Deiyonizasyon Aşaması)
Birinci aşamada, besleme suyundaki iyonlar seyreltme haznesindeki iyon değişim reçineleri tarafından yakalanır. Karma yataklı reçine başlangıçta rejenerasyon formundadır (hidrojen formunda katyon reçinesi ve hidroksit formunda anyon reçinesi, taze bir karma yataklı DI reçinesine benzer). Su reçine yatağından aktıkça, iyonik kirleticiler reçine bölgelerine değiştirilir: sudaki katyonik türler (örn. Ca²⁺, Mg²⁺, Na⁺, K⁺, NH₄⁺) katyon reçinesinden H⁺ iyonlarını yerinden oynatır ve anyonik türler (örn. Cl⁻, SO₄²⁻, NO₃⁻, HCO₃⁻, CO₃²⁻, F⁻, silika (SiO₂⁻), borat) anyon reçinesinden OH⁻ iyonlarını yerinden oynatır . Salınan H⁺ ve OH⁻ hemen saf H₂O oluşturmak üzere yeniden birleşir. Bu iyon değişim mekanizması sayesinde, besleme reçine yatağından geçerken deiyonize edilir - reçine çözünmüş iyonları etkili bir şekilde toplar ve suyu arıtır. Reçine tarafından yapılan bu deiyonize etme, geleneksel karma yataklı bir iyon değiştiriciye benzer, ancak toplu olarak değil EDI'da sürekli olarak gerçekleşir. Su seyreltme bölmesinin çıkışına ulaştığında, güçlü iyonik kirleticilerin çoğu reçineye giderilmiş olur. Seyreltme bölmesindeki suyun direnci böylece iyonlar giderildikçe artar.
Parametreler ve Hususlar – İyon Değişim Aşaması: Bu aşamanın performansı besleme suyu kalitesine ve reçine durumuna bağlıdır. İzlenmesi gereken önemli parametreler şunlardır:
Besleme İletkenliği (TDS): EDI beslemesi (genellikle RO permeatı) düşük toplam çözünmüş katılara sahip olmalıdır (örneğin < 40 µS/cm, genellikle çok daha düşük) böylece reçinenin başlangıçta çoğu iyonu yakalayabilmesi ve EDI'nin optimum aralığında çalışması sağlanır. Daha yüksek besleme iletkenliği daha yüksek iyonik yük anlamına gelir ve iyonları gidermek için daha fazla elektrik akımı gerekir; aşırıysa, EDI reçinesi suyu yüksek saflığa parlatmakta zorlanabilir.
Besleme Sertliği: Eser sertlik (Ca²⁺, Mg²⁺) bile reçine değişim bölgelerini tüketebilir ve konsantrede kireçlenmeye neden olabilir. Tipik olarak, besleme sertliği CaCO₃ olarak ~1 mg/L ile sınırlıdır (ultra saf uygulamalar için genellikle <0,1 mg/L). Sertlik genellikle yukarı akış yumuşatma veya RO ile giderilir. Sertlik tasarım sınırlarını aşarsa, konsantrede CaCO₃ olarak çökelebilir veya hatta reçineyi kirleterek iyon değişim verimliliğini azaltabilir.
Besleme CO₂ (Karbondioksit) ve Zayıf İyonize Türler: Sudaki CO₂, anyon reçinesinin yakalayacağı ve OH⁻ tüketeceği bikarbonat/karbonat oluşturur. EDI beslemesi, CO₂ yüksekse genellikle RO'dan sonra CO₂ gazının alınmasını gerektirir, çünkü CO₂ iletken değildir ancak reçineyi yükleyecek ve daha sonra bikarbonat olarak serbest kalacak ve direnci etkileyecektir. Silika (zayıf iyonize H₄SiO₄) başka bir türdür - EDI beslemesinde genellikle <1–2 mg/L olmalıdır . Bu zayıf asitler/bazlar RO tarafından tamamen giderilmez ancak EDI'nin sürekli rejenerasyonuyla (daha sonra tartışılacaktır) işlenebilir.
Reçineden Akış Hızı (Temas Süresi): Etkili iyon değişimi için reçine yatağında yeterli akış temas süresi gerekir. Akış çok yüksekse, iyon giderimi eksik olabilir; çok düşükse konsantrede ölçeklenme riski artar. Üreticiler bir aralık belirtir - örneğin, bir modül 1,5–2,2 m³/saat ürün akışını idare edebilir. Tasarım akışı içinde çalışmak, iyon değişimi adımının verimli bir şekilde gerçekleşmesini sağlar.
Sıcaklık: Reçine değişim kinetiği ve iletkenliği sıcaklıkla (sınırlar dahilinde) iyileşir. EDI modülleri genellikle 10 °C ile 38 °C arasında çalışır. ~10 °C'nin altında, reçine iyon hareketliliği azalır ve deiyonizasyon daha az verimlidir; maksimumun üzerinde, reçine veya membran malzemeleri bozulabilir. Besleme sıcaklığının aralıkta tutulması, iyon değişim aşamasını etkili tutar.
Normal çalışma sırasında, iyon değişim aşaması iyonların büyük kısmını ortadan kaldırmalı ve ürün su iletkenliği reçine yatağı boyunca önemli ölçüde düşmelidir . Sensörler işlemin erken aşamalarında anormal iletkenlik gösteriyorsa (örneğin, mevcutsa hücre ortası ölçümleri veya ürünün özdirencinde beklenmeyen düşüş), bu aşamada reçine tükenmesi veya kirlenmesi belirtisi olabilir. Uygulamada, reçine daha sonraki aşamada sürekli olarak yenilendiğinden, iyon değişim kapasitesi devam eder - performanstaki herhangi bir düşüş genellikle statik karışık yataklı bir sistemde olduğu gibi basit bir tükenmeden ziyade reçinenin organik kirlenmesi veya yetersiz rejenerasyon akımı gibi sorunlara işaret eder.
İyon Göçü (Elektrokimyasal Ayırma Aşaması)
EDI'nin ikinci aşaması, uygulanan DC elektrik alanı altında iyon göçü yoluyla iyonların elektrokimyasal olarak ayrılmasıdır. Seyreltme odasındaki reçineler iyonları yakaladığında, bu iyonlar kalıcı olarak tutulmaz - elektrik alanı onları reçine boncuklarından çeker ve seyreltme bölmesinden dışarı atar. Katyon reçinesinden desorbe edilen katyonlar negatif yüklü katoda doğru göç eder ve anyon reçinesinden gelen anyonlar pozitif yüklü anoda doğru göç eder. Seyreltme bölmesinin her iki tarafında, iyon seçici membranlar katyonların veya anyonların bitişik konsantre edici bölmelere geçmesine izin verir:
Katyon değişim membranları (CEM), seyreltik haznenin katoda bakan tarafını sınırlar. Bu membranlar katyonların konsantre haznesine geçmesine izin verir, ancak anyonları reddeder.
Anyon değişim membranları (AEM), anot tarafına bakan tarafta bulunur ve anyonların dışarı çıkmasına izin verirken katyonların dışarı çıkmasını engeller.
İyonlar seyreltme hücresinden uygun membrandan çekildikçe konsantre bölmelerine girerler. Önemlisi, her konsantre bölmesinin uzak tarafındaki ikinci bir membran iyonların bir sonraki seyreltme hücresine daha fazla göç etmesini önler. Örneğin, bir CEM'den konsantre bölmesine geçen bir katyon, geçemediği o bölmenin karşı tarafındaki bir anyon membranıyla karşılaşacak ve katyonu konsantre bölmesinde etkili bir şekilde hapsedecektir. Benzer şekilde, seyreltik bir hücreden çıkan anyonlar konsantrenin uzak tarafındaki bir katyon membranı tarafından sınırlandırılır. Bu şekilde, uzaklaştırılan iyonlar konsantre kanallarında (yavaş akan bir tuzlu su akışı taşıyan) toplanarak ürün su akışından izole edilir. Net sonuç, sürekli bir iyon giderimi ve transferidir : seyreltme akışı iyonlardan arındırılır ve deiyonize ürün haline gelirken, konsantre akışı uzaklaştırılan iyonları taşır.
Bu aşama esasen reçine ile geliştirilmiş bir elektrodiyaliz işlemidir . Seyreltme bölmelerinde iyon değişim reçinesinin varlığı iletkenliği büyük ölçüde artırır ve iyon taşınmasını kolaylaştırır, EDI'nin tek başına elektrodiyalizden çok daha düşük kalıntı iyon seviyelerine ulaşmasını sağlar. Reçine, yüklü fonksiyonel grupların yüksek yoğunluklu bir yolunu sağlar, böylece su çok saf hale geldiğinde (ve doğrudan iletkenliği düştüğünde) bile elektrik akımı hala reçine üzerinden ilerleyerek iyonları çekebilir. Reçine olmadan, suyun iyonik içeriği düştüğünde, direnç artar ve daha fazla iyon giderimini sınırlar; reçine ile, sabit bir iletken ortam kalır ve iyonların eser seviyelere kadar giderilmesini sağlar .
Parametreler ve Hususlar – Ayırma Aşaması: Bu aşamadaki temel faktörler, iyon göçünü yönlendiren elektriksel ve hidrolik koşulları içerir:
DC Akımı / Voltajı: İyon göçünün itici gücü uygulanan elektrik akımıdır. EDI sistemleri, istenen giderimi sağlamak için genellikle sabit akım (veya akım sınırlı) modunda çalıştırılır. Seyreltikten tüm iyonları uzaklaştırmak için yeterli akım sağlanmalıdır. Akım çok düşükse, bazı iyonlar reçine üzerinde kalacak ve ürüne sızacaktır; çok yüksekse aşırı elektrokimyasal reaksiyonlar (su parçalanması, gaz evrimi) meydana gelebilir (tasarım sınırlarına kadar). Üreticiler, modül başına optimum akım aralığını belirtir (örneğin, bir modül ~4–9 A kullanabilir). Örneğin, bir DuPont EDI modülü modül başına 9,0 A ve ~160 V DC'ye izin verir. Sistemin DC güç kaynağı (doğrultucu) buna göre boyutlandırılmalı ve sabit tutulmalıdır (çıkış akımı %±5'in ötesinde dalgalanmamalıdır) . Tipik olarak, voltaj besleme suyu iletkenliğine ve istenen akıma göre ayarlanır; besleme suyu çalışma sırasında daha saf hale geldikçe direnç artar ve gereken voltaj yükselebilir. Belirli bir akımdaki yığın voltajının izlenmesi, hücrelerin kirlenip kirlenmediğini veya ölçeklenip ölçeklenmediğini gösterebilir (aynı akımda zamanla artan bir voltaj, muhtemelen membran ölçeklenmesi veya reçine kirlenmesi nedeniyle daha yüksek direnci gösterir).
Akış Hızları (Seyreltme ve Konsantre Etme): Seyreltik (ürün) akış hızı, belirtildiği gibi kalma süresini etkiler, ancak aynı zamanda iyonların değişimden sonra ne kadar çabuk süpürüldüğünü de etkiler. Konsantre akış hızı da aynı derecede önemlidir; uzaklaştırılan iyonları konsantre odalarından dışarı atmaya ve çökelmeyi önlemeye yetecek kadar yüksek olmalı, ancak iyonik içeriği aşırı seyreltmeyecek veya gereksiz basınç düşüşüne neden olmayacak kadar yüksek olmalıdır. Birçok EDI sistemi, konsantre akışını ürün akışının yaklaşık %5-10'una ayarlar ve bu da besleme suyunun yaklaşık %5-10'unun konsantreden reddedilmesiyle sonuçlanır (örn. %90-95 su geri kazanımı) . Konsantreyi RO beslemesine geri dönüştürerek daha yüksek geri kazanımlar mümkündür, ancak yalnızca dikkatli bir şekilde tasarlanırsa (geri dönüşüm CO₂ yükünü artırabilir ve safsızlıkların yeniden tanıtılması riskini taşıyabilir). Konsantre çıkış iletkenliğini izlemek önemlidir - yükselen bir konsantre iletkenliği iyonları taşıdığını gösterir (normal), ancak çok doymuş hale gelirse (ölçekleme sınırlarına yaklaşır) veya çok düşük hale gelirse (belki düşük iyonik yük veya ürün suyunun membran sızıntısını gösterir), sorunlara işaret edebilir. Tipik olarak, konsantre iletkenliği, iyonları topladığı için besleme iletkenliğinden daha yüksek olacaktır.
Pressure and Leak Control: The diluting and concentrating streams are at slightly different pressures – concentrate outlet is usually maintained at a lower pressure than the dilute/product outlet to prevent any back-leakage of concentrate into product. Operators monitor pressure differential: the concentrate outlet pressure should be a few psi lower (e.g. 0.5–0.7 bar lower) than the product outlet. If pressure differential in the wrong direction occurs, product water could be contaminated by concentrate. Also, measuring pressure drop across the diluate compartments helps detect fouling (an increasing pressure drop means flow channels in resin might be plugging with debris or scale).
Membran Sağlığı: Doğrudan bir "parametre" olmasa da, iyon seçici membranların bütünlüğü hayati önem taşır. Bir membran hasar görürse (yırtılma veya sızıntı), akışların çapraz kontaminasyonuna neden olabilir. Akışların iletkenliği veya iyonik analizi bazen bunu tespit edebilir (örneğin, üründe beklenmedik şekilde yüksek iyonlar veya garip pH değişimleri). Ürün direncinin düzenli olarak izlenmesi ve konsantrenin çökeltiler açısından görsel olarak incelenmesi, membran sorunlarını yakalamaya yardımcı olabilir.
Ayırma aşamasında genellikle sabit bir akım ve akış mevcuttur. Operatörler sabit akış ve akım altında ürün su direncini sürekli olarak izleyeceklerdir - bu, tüm sürecin iyonları ne kadar iyi giderdiğinin toplu bir ölçüsüdür. Sürekli olarak yüksek direnç (düşük iletkenlik), göç aşamasının iyonları etkili bir şekilde temizlediği anlamına gelir. Ürün direnci hedefin altına düşmeye başlarsa (örneğin 1 MΩ·cm'nin altına veya kazan beslemesi için 5 MΩ·cm veya yarı iletken sınıfı için 15 MΩ·cm gibi spesifikasyonun altına), göç yoluyla iyon gideriminin yetersiz olduğunu, muhtemelen yetersiz akım, iyon taşınmasını engelleyen kirleticiler veya tükenmiş reçine (yenileme devam etmiyorsa) nedeniyle olduğunu gösterir. Bu gibi durumlarda, operatörler akımı artırabilir (kapasite izin veriyorsa), bakım/temizlik yapabilir veya performansı geri yüklemek için besleme kalitesini kontrol edebilir.
Yerinde Rejenerasyon (Elektrokimyasal Rejenerasyon Aşaması)
EDI'nin benzersiz ve kritik bir yönü reçine yatağının sürekli elektrokimyasal rejenerasyonudur. Bu üçüncü aşama reçine iyonları uzaklaştırıp taşıdığında aynı anda gerçekleşir. Seyreltilen su reçine yatağının çıkışına doğru iyonik içerikte çok düşük hale geldikçe, elektrik akımını taşımak için mevcut iyonlar tükenir. Ancak, akımın durması yerine, güçlü elektrik alanı suyun bir kısmının hidrojen (H⁺) ve hidroksit (OH⁻) iyonlarına ayrışmasına (bölünmesine) neden olur. Esasen suyun lokalize bir elektrolizi olan bu olgu, EDI'de sıklıkla "suyun bölünmesi" olarak adlandırılır . Bu durum, esas olarak reçinelerin ve membranların arayüzlerinde veya yerel potansiyel bir eşiği aştığında reçine-reçine bağlantılarında meydana gelir (bir reçine boncuk-membran arayüzü boyunca yaklaşık 0,8 V, su moleküllerini bölmek için yeterlidir) . Yeni oluşturulan H⁺ ve OH⁻ iyonları derhal iyon değişim reçinesine bağlanarak katyon reçinesini H⁺ formuna ve anyon reçinesini OH⁻ formuna yerinde yeniden oluşturur . Bu, reçineyi sürekli olarak asit ve bazla şarj etmeye eşdeğerdir, ancak elektriksel olarak ve sürekli bir temelde gerçekleştirilir.
Suyun parçalanması ve rejenerasyonu, EDI'nin kimyasal kesinti olmadan sürekli olarak ultra saf su üretmesini sağlar. Aslında, seyreltme haznesinin son kısmındaki reçine, yakalanan safsızlık iyonlarını yerinden oynatan üretilen H⁺/OH⁻ tarafından sürekli olarak rejenerasyona tabi tutulur. Yerinden oynamış bu safsızlık iyonları (örneğin, reçine bölgesindeki Na⁺, H⁺ tarafından tekmelenir) daha sonra göçe katılır ve konsantreye sürüklenir. Reçine üzerinde yerlerini alan H⁺ ve OH⁻, reçine bölgesi yeni bir bölüme geçtiğinde sonunda su oluşturmak üzere yeniden birleşir veya sudaki zayıf asitleri/bazları nötralize eder. Bu kendi kendini rejenerasyon döngüsü, reçine yatağının geleneksel bir sistemde olduğu gibi asla tükenmediği anlamına gelir; sürekli olarak dahili olarak rejenerasyon yapılır. Sonuç olarak, EDI, tek başına bir iyon değiştiricinin tipik tükenme eğrisinden ziyade, zaman içinde sürekli olarak yüksek bir ürün suyu saflığını koruyabilir .
Rejenerasyonun en önemli faydası, karbondioksit (H₂CO₃ formunda) ve diğer zayıf iyonize kirleticilerin uzaklaştırılmasıdır. Karma yataklı bir iyon değiştiricide, güçlü iyonlar tükendiğinde CO₂ ve SiO₂'nin uzaklaştırılması zordur, ancak EDI'da, rejenere edilen H⁺ ve OH⁻ bu türleri etkili bir şekilde nötralize eder: CO₂ bikarbonat/karbonata dönüştürülür ve anyon reçinesi tarafından uzaklaştırılır ve silika (zayıf bir asit) OH⁻ tarafından deprotone edilerek daha sonra uzaklaştırılan silikat oluşturulur. Böylece, EDI güçlü iyonlar gittikten sonra bu zayıf kirleticilerin daha fazla uzaklaştırılmasını sağlayabilir. Bu nedenle, EDI genellikle RO suyunu "cilalamak" için kullanılır, çünkü RO çözünmüş CO₂ veya silikayı tam olarak uzaklaştıramayabilir, ancak EDI yüksek dirençlilik rejimi ve sürekli rejenerasyon sayesinde bunları parlatabilir.
Parametreler ve Hususlar – Rejenerasyon Aşaması: Rejenerasyon için birincil itici güç, seyreltik bölmelerin “sınırlayıcı akımını” aşan uygun bir elektrik akımı (veya akım yoğunluğu) sağlamaktır. Sınırlayıcı akım, seyreltikteki mevcut iyonların tamamen taşındığı eşiktir; bunun ötesinde, ek akım suyun parçalanmasına neden olur. Operatörler, sürekli rejenerasyonu sürdürmek için EDI sisteminin hafifçe aşırı sınırlayıcı akım rejiminde çalıştırılmasını sağlar. Önemli noktalar şunlardır:
Rejenerasyon için Mevcut Ayar Noktası: EDI üniteleri genellikle hem iyonik yükü kaldıran hem de suyu bölmek için yeterli fazlalık sağlayan bir hedef akımla tasarlanır. Örneğin, bir besleme belirli bir toplam iyonik yüke sahipse (genellikle eşdeğerlerde toplam değiştirilebilir anyonlar/katyonlar olarak ölçülür), sistem tasarımı bu iyonları taşımak için minimum bir akım belirleyecektir. Bunun üzerindeki herhangi bir akım, reçineyi su bölerek rejenerasyona sokar. Akım çok düşük ayarlanırsa (gerekli değerin altında), hücrenin sonraki kısmındaki reçine doyabilir ve rejenerasyon yapmayabilir, bu da iyonların sızmasına yol açar. Akım çok yüksekse, su bölünmesi aşırı olur, bu da ürün pH'ını veya konsantre pH'ını aşırı yükseltebilir ve potansiyel olarak kireçlenmeye veya hızlandırılmış membran bozulmasına neden olabilir ve enerji israfına yol açar. Bu nedenle, akımı optimum bant içinde kontrol etmek çok önemlidir. Uygulamada, birçok EDI sistemi sabit bir akımda çalışır ve besleme kalitesinin spesifikasyonlar dahilinde olmasına güvenir. Besleme iyonik yükü artarsa (örneğin daha yüksek CO₂ veya sertlik sızıntısı), operatörün rejenerasyonu sürdürmek için akımı artırması gerekebilir.
Voltaj İzleme: Belirtildiği gibi, belirli bir akım için artan voltaj, kireçlenme veya kirlenme belirtisi olabilir. Su bölünmesinin belirli bir yönü, konsantre içindeki yerel pH'ı (OH⁻'nin biriktiği yer) artırabilmesi ve anot yakınındaki bölgelerde (H⁺'nin biriktiği yer) pH'ı azaltabilmesidir. Bu nedenle aşırı yüksek akım, silika veya kalsiyum karbonatı çökeltebilecek konsantre içinde yüksek pH'a yol açabilir. Konsantre pH'ını izlemek veya Langelier doygunluk indeksini hesaplamak, rejenerasyon sırasında kireçlenmeyi kontrol etmenin bir parçası olabilir. Bazı sistemler, konsantre pH'ını belirli değerlerin altında tutmak için akımı veya geri kazanımı sınırlar (örneğin, fazla OH⁻ nedeniyle konsantre pH'ı >10 olursa, silika polimerleşebilir).
Reçine Durumu: Zamanla reçineler kirlenme veya oksidatif hasar nedeniyle kapasitelerini kaybedebilirler. Rejenerasyon süreci onları aktif tutar, ancak reçine hasar görürse (örneğin klor saldırısı veya organik kirlenme nedeniyle), su parçalanması bile değişim noktalarını tam olarak geri yüklemez. Operatörler normal veya maksimum akımda bile ürün direncinin aylar/yıllar boyunca aşağı doğru eğilim gösterdiğini fark ederse, bu reçine aşınması ve azalmış rejenerasyon etkinliğinin göstergesi olabilir. Bu, modülün değiştirilmesini gerektirebilir.
Temperature Effects: Water splitting is endothermic and also limited by kinetics; warmer water can facilitate easier dissociation. Operating at too low temperature might slightly hinder the efficiency of regeneration (in addition to ion exchange). However, this is typically a minor factor compared to current control.
Özetle, EDI iyonik yüke göre yeterli akımla beslendiği sürece, elektro-rejenerasyon otomatik olarak gerçekleşecek ve reçineyi H⁺/OH⁻ formunda tutacaktır. Bu aşama, normal çalışma sırasında operatör için büyük ölçüde "görünmez"dir - başarısı, ürün suyunun kararlı yüksek özdirencine ve reçinenin uzun ömrüne yansır. Harici kimyasal rejenerasyon adımlarına olan ihtiyacı ortadan kaldırır. Bu aşama başarısız olursa (yetersiz akım veya zehirli reçine nedeniyle), ürün suyu kalitesindeki düşüşle belirginleşir. Bu gibi durumlarda, manuel rejenerasyon yardımı yapılabilir (örneğin, bazı operatörler reçineyi yeniden şartlandırmak için seyreltik bir asit/bazı geçici olarak dolaştırır veya bir devridaim modunda akımı artırır). Ancak, ideal koşullar altında, sürekli elektriksel rejenerasyon modülün ömrü boyunca yeterlidir.
Elektrodeiyonizasyon (EDI) ile Giderilebilen Tipik Safsızlıklar
EDI, sudan neredeyse tüm iyonize veya iyonize edilebilir türlerin uzaklaştırılmasında etkilidir. Uzaklaştırılan tipik safsızlıklar ve iyonlar şunlardır:
Katyonik safsızlıklar: Kalsiyum (Ca²⁺), Magnezyum (Mg²⁺), Sodyum (Na⁺), Potasyum (K⁺), Amonyum (NH₄⁺), Demir (Fe²⁺/Fe³⁺), Manganez ve diğer metal katyonları EDI'daki katyon değişim reçinesi tarafından kolayca uzaklaştırılır. Bunlara genellikle beslemede veya belirli atık akışlarında bulunan eser ağır metaller (Cu²⁺, Ni²⁺, Zn²⁺, vb.) dahildir.
Anyonik kirleticiler: Klorür (Cl⁻), Sülfat (SO₄²⁻), Nitrat (NO₃⁻), Bikarbonat/Karbonat (HCO₃⁻/CO₃²⁻), Florür (F⁻), Silikat/Silika (tipik olarak H₂SiO₃ veya SiO₂·nH₂O olarak bulunur), Bor (borat anyonu olarak) ve diğerleri anyon reçinesi tarafından uzaklaştırılır. Karbonik asit (CO₂'den H₂CO₃) ve silisik asit (H₄SiO₄) gibi zayıf ayrışmış asitler bile etkili bir şekilde ortadan kaldırılır çünkü reçine OH⁻'nin yüksek pH ortamı bunların uzaklaştırılması için iyonlaşmasına yardımcı olur .
İyonize edilebilir organik bileşikler: EDI, organik asitler (örneğin asetik asit, formik asit ayrışmış formlarında) ve düşük molekül ağırlıklı iyonize edilebilir organikler gibi yüklü organik türleri giderebilir. Bunlar yük taşıyorlarsa reçineler tarafından yakalanırlar. Ancak, nötr organikler (iyonize olmayan) iyon değişim mekanizmasıyla, tesadüfen adsorpsiyonla hariç giderilmezler, bu nedenle EDI, iyonik organik madde ötesinde organik giderim için tasarlanmamıştır. İyonik olmayan Toplam Organik Karbon (TOC), kirlenmeyi önlemek için beslemede en aza indirilmelidir (örneğin RO ve aktif karbon yoluyla) .
Silika: Özellikle belirtilmeye değer, silika (genellikle yüksek saflıktaki suda ayrı olarak bildirilir) silikat iyonları olarak uzaklaştırılır. EDI ürün suyu genellikle çok düşük silikaya sahiptir ve güç ve yarı iletken gibi endüstriler için sıkı gereklilikleri (<0,1 mg/L) karşılar. İnce hücreli EDI tasarımları, eski tasarımlara göre biraz daha yüksek besleme silikasına (~2 mg/L'ye kadar) izin verir, ancak yine de ürün silikası büyük ölçüde azaltılır.
Gazlar ve Çözünmüş İyonize Edilebilir Gazlar: Bahsedildiği gibi çözünmüş CO₂, iyonik forma dönüştürülerek işlenir. Amonyak (NH₃/NH₄⁺) mevcutsa (kloramin parçalanmasından veya başka bir kaynaktan) katyon reçinesi üzerinde amonyum iyonu olarak yakalanır. Oksijen veya nitrojen gazları iyonize değildir ve geçer (genellikle saflık için bir endişe olmasa da, başka bir yerde işlenen korozyon için daha fazla). EDI, elektrotlarda H₂ ve O₂ gazları üretir (havalandırılır, ürün suyunda değil).
Özünde, herhangi bir iyonik safsızlık - ister tuz, mineral veya inorganik kirletici olsun - EDI ile giderilebilir. RO ön işleminden sonra, tipik kalan iyonlar birkaç mg/L veya daha az mertebesinde olabilir; EDI bunları µg/L seviyelerine kadar parlatacaktır. Örneğin, RO süzüntüsü 5–10 µS/cm iletkenliğe sahipse (~2–5 ppm TDS), EDI bunu <0,1 µS/cm'ye (ultra saf) düşürebilir. EDI'nin hedef aldığı yaygın kalan iyonlar arasında sodyum, klorür, sülfat, silika ve bikarbonat (CO₂'den) bulunur - bunlar genellikle RO'nun düşük miktarlarda bıraktığı iyonlardır ve EDI, ultra saflık özelliklerini karşılamak için bunları gidermek için kullanılır.
EDI'nin mikroorganizmaları veya parçacıkları (genellikle yukarı akışta filtrelenmiş/UV ile işlenmiş) ortadan kaldırmadığı unutulmamalıdır. Ayrıca, EDI'nin tamamen iyonik olmayan kirleticileri (örneğin benzen gibi çözünmüş organikler veya iyonize olmamış çok zayıf asitler/bazlar) ortadan kaldırmak için özel bir mekanizması yoktur; bu tür kirleticiler gerekirse diğer saflaştırma adımlarıyla ele alınmalıdır. Ancak iyonik kirlenme için EDI, genellikle tespit sınırlarına kadar iyon gidermeyi başararak son derece etkili bir parlatma sağlar.
Endüstrilerde EDI Uygulamaları
EDI sistemleri, yüksek saflıkta veya deiyonize suyun gerekli olduğu çok sayıda endüstride kullanılır. Temel uygulama alanları şunlardır:
Yarı iletken ve Mikroelektronik: Elektronik endüstrisi, yarı iletken yongaları ve bileşenlerini durulamak ve temizlemek için ultra saf suya (UPW) ihtiyaç duyar. İz iyonik kirleticiler bile mikro devrelerde elektriksel kısa devrelere veya kusurlara neden olabilir. EDI, yarı iletken fabrikalarında çok adımlı su arıtmanın bir parçası olarak (genellikle RO ve ultrafiltrasyondan sonra) ~18 MΩ·cm özdirenç elde etmek için yaygın olarak kullanılır. EDI, iyonları sürekli olarak gidererek, durulama suyunun yongalarda iletken kalıntı bırakmamasını sağlayarak yoğun şekilde paketlenmiş devrelerde kısa devreleri önler . Bu uygulama genellikle en yüksek su kalitesini gerektirir; EDI, yarı iletken su özelliklerinde kritik olan son derece düşük silika ve bor seviyelerine ulaşılmasına yardımcı olur.
İlaç ve Biyoteknoloji: İlaç üretimi ve biyoteknoloji laboratuvarları, formülasyonları hazırlamak, ekipmanları temizlemek ve bileşen suyu olarak (örneğin parenteral solüsyonlar, ortam hazırlama) deiyonize su kullanır. İyonik safsızlıklar istenmeyen reaksiyonları katalize edebilir veya ilaç solüsyonlarında çökeltilere neden olabilir. EDI, RO ve UV ile birlikte, genellikle USP Saflaştırılmış Su üretmek ve hatta Enjeksiyonluk Su (WFI) üretmenin bir parçası olarak kullanılır (ancak WFI son adım olarak damıtma veya ultrafiltrasyon gerektirebilir). EDI'nin kimyasal rejenerantı olmadığından, herhangi bir kimyasal katkı maddesinin eklenmesini önler ve ilaç endüstrisinde doğrulama için önemli olan tutarlı su kalitesini korur. Sürekli çalışma ayrıca rejenerasyon için kesinti süresi olmaması anlamına gelir ve kritik süreçler için yüksek saflıkta suyun güvenilir bir şekilde tedarik edilmesini sağlar . İlaç tesisleri, EDI modüllerinin mikrobiyal büyümeyi kolayca teşvik etmemesi gerçeğini takdir eder - yüksek saflık, yüksek dirençli ortam ve sabit elektrik alanı, mikroorganizmaları engelleyen biyostatik bir durum yaratır.
Güç Üretimi (Kazan Besleme Suyu): Güç endüstrisi, kazanlarda buhar üretimi ve yüksek basınçlı buhar türbinlerinde makyaj suyu için demineralize suya ihtiyaç duyar. Kazan beslemesindeki herhangi bir iyonik safsızlık, türbin kanatlarında veya kazan borularında kireç birikintilerine yol açabilir ve korozyona ve verimlilik kaybına neden olabilir. EDI sistemleri, son derece düşük iletkenliğe ve silikaya sahip demineralize su sağlamak için RO permeatını parlatır, kazanları kireçlenmeye karşı korur ve sıcak noktalara veya korozyona neden olabilecek iletken birikintilerin birikmesini önler. Güç sektöründe, EDI genellikle geleneksel iyon değişim demineralizatörlerinin yerini alır veya onları güçlendirir ve sahada asit/kostik işlemeyi ortadan kaldırır. Güvenilir sürekli üretim, enerji santrallerinin istikrarlı çalışmasını sürdürmesine yardımcı olur - buhar döngüsündeki safsızlıklar en aza indirildiğinden, türbinler ve ısı eşanjörleri temizlikler arasında daha uzun süre çalışır. Enerji santralleri için EDI üniteleri genellikle büyük akış hızları için tasarlanmıştır ve genellikle ön filtreler, RO ve EDI dahil olmak üzere kızak monteli demineralizasyon trenlerine entegre edilir.
Gıda ve İçecek: Birçok gıda ve içecek işletmesi, ürün seyreltme, bileşen suyu veya yardımcı amaçlar (ürünlerle doğrudan temas halindeki buhar için kazan beslemesi gibi) için deiyonize su kullanır. Örneğin, şişelenmiş içecek üretimi, tat nötrlüğünü ve kararlılığını sağlamak için EDI ile cilalanmış su kullanabilir (kalsiyum veya sülfat gibi iyonlar, lezzeti etkileyebilir veya ürün formülleriyle etkileşime girebilir). Bira fabrikaları ve mandıralar, istenen mineral içeriğini elde etmek için demineralize su kullanabilir. EDI, reçine rejenerant kontaminasyonu riski olmadan tutarlı bir su kalitesi sağlar. Tatlandırıcı veya bileşen üretiminde, EDI tarafından üretilen deiyonize su, ürün saflığını artırabilir. Ek olarak, rejenerasyon kimyasallarının olmaması, gıda sınıfı uygulamalarda kimyasal kalıntı olasılığını ortadan kaldırdığı için bir avantajdır. (Not: Gıda/içecekteki EDI ürün suyu genellikle tat veya besin için bir dereceye kadar remineralize edilir veya harmanlanır, ancak EDI bilinen bir başlangıç saflığı sağlar).
Laboratuvar ve Analitik Su: Laboratuvarlar (kimyasal, biyolojik, analitik laboratuvarlar) genellikle deneyler ve cihaz beslemesi (örneğin HPLC, GC, hücre kültürü vb.) için Tip I ve Tip II reaktif sınıfı suya ihtiyaç duyar. EDI modülleri, kritik analitik uygulamalar için sürekli olarak 18 MΩ·cm ultra saf su üretmek amacıyla sıklıkla laboratuvar suyu arıtma sistemlerine (RO'dan sonra) dahil edilir. EDI sürekli çalışabildiğinden, laboratuvar sistemleri bir depolama döngüsünde saflığı korumak için suyu EDI aracılığıyla yeniden dolaştırabilir. Ayrıca kartuş değiştirme ihtiyacını da azaltır - EDI esasen çabuk tükenmeyen sürekli bir karışık yataklı parlatıcı gibi davranarak laboratuvar su sistemlerinin maliyetini ve bakımını azaltır. Birçok ticari laboratuvar su ünitesi (örneğin, Millipore veya Thermo'nunkiler) hassas analizler için gereken saflığı elde etmek amacıyla diğer parlatma adımlarıyla (UV, 0,2 µm filtre) birlikte küçük ölçekli EDI modülleri kullanır.
Çevre Uygulamaları ve Atık Su Arıtımı: Saf su üretiminin ötesinde, EDI özellikle ağır metallerin veya diğer iyonik kirleticilerin giderilmesi ve geri kazanılması için belirli atık suların arıtılmasında uygulanmıştır. Örneğin, elektrokaplama veya metal kaplama atık suyunda, EDI krom (Cr³⁺/Cr⁶⁺), bakır (Cu²⁺), kobalt, nikel vb. gibi metalleri giderebilir ve bunları geri kazanım veya uygun şekilde bertaraf için reddedilen bir akımda yoğunlaştırabilir. Nükleer atık su yönetiminde, EDI sezyum (Cs⁺) gibi radyonüklidlerin giderilmesi için incelenmiştir. Bu uygulamalarda EDI yüksek iyon giderme verimliliği sağlayabilir; ancak, besleme koşulları daha zordur (daha yüksek TDS, rekabet eden iyonların varlığı). Bu tür amaçlar için genellikle özel EDI kurulumları veya çok aşamalı EDI kullanılır. Avantajı, EDI'nin büyük miktarda kullanılmış kimyasal rejenerant üretmemesidir; Bunun yerine, kirleticilerle daha küçük bir konsantre tuzlu su üretir ve bu da tehlikeli atıkların akış aşağısında işlenmesini basitleştirebilir. Çevresel uygulamalarda, EDI sürekli çalışabilme yeteneği ve belirli iyonlar için seçici uzaklaştırma (membran/reçine tiplerini ayarlayarak) potansiyeli nedeniyle değerlidir.
Yukarıdakiler başlıca kullanımlardır, ancak başka niş uygulamalar da vardır (örneğin, deiyonize suyun seyreltme ve temizleme için kullanıldığı kimya endüstrisinde veya otomotivde akü suyu üretimi vb.). Özetle, çözünmüş tuzlardan arındırılmış, güvenilir bir yüksek saflıkta veya ultra saf su tedariki gerektiren herhangi bir işlem, EDI teknolojisi için bir adaydır. Elektronik, ilaç ve enerji sektörlerindeki yaygın benimseme, tutarlı su kalitesine duyulan kritik ihtiyaç ve kimyasal rejenerasyonu ortadan kaldırmanın ekonomik/çevresel avantajları tarafından yönlendirilmektedir.
Performans ve Uzun Ömürlülük için İşletme Önerileri
Bir elektrodeiyonizasyon (EDI) sistemini çalıştırmak, optimum performansı garantilemek ve modüllerin ömrünü uzatmak için belirli su kalitesi parametrelerine ve sistem koşullarına dikkat etmeyi gerektirir. Aşağıdakiler, EDI çalışması sırasında izlenmesi gereken temel operasyonel hususlar ve hususlardır:
Besleme Suyu Kalitesi İzleme: Vurgulandığı gibi, EDI'ye giden besleme, belirli kalite kriterlerini karşılamak için önceden işlenmelidir (genellikle RO ve muhtemelen gaz giderme/yumuşatma ile). Operatörler besleme iletkenliğini, sertliğini, silikayı ve CO₂ seviyelerini ve oksidanların varlığını sürekli veya düzenli olarak izlemelidir . İletkenlik, toplam iyonik yük hakkında hızlı bir gösterge sağlar, ancak zayıf iyonize türleri (CO₂, SiO₂) ortaya çıkarmayabilir; bu nedenle Toplam Değiştirilebilir Anyonları (TEA) ölçmek veya alkalinite/pH'a göre CO₂'yi hesaplamak yararlıdır. Sertlik ölçülmelidir - bir yumuşatıcıda veya RO baypasında hafif bozulmalar bile sertliği artırabilir ve ölçeklenme riski oluşturabilir. Sertlik, spesifikasyonların üzerine çıkarsa (>0,1–0,2 ppm CaCO₃ olarak), operatörlerin EDI geri kazanımını azaltması veya önleyici bir kireç temizliği yapması gerekebilir. Beslemedeki silika, yukarı akış RO çift geçişli değilse izlenmelidir (bazı tesisler, RO reddi yetersizse silika için bir iyon değişimi veya adsorban adımı da içerir). CO₂, besleme alkalinitesi veya bir CO₂ sensörü aracılığıyla izlenir; yüksek CO₂, anyon reçinesindeki yükü azaltmak için EDI'dan önce bir gaz giderme membranı veya zorlamalı çekişli gaz giderici ile giderilebilir . Oksitleyici maddeler (klor, kloramin, ozon) beslemede tespit edilemez olmalıdır -genellikle <0,02 ppm serbest klor- çünkü bunlar iyon değişim reçinelerine ve membranlara saldırarak geri döndürülemez şekilde hasar verir. Çevrimiçi ORP veya klor monitörleri, oksidan geçişi olmadığından emin olmak için genellikle aktif karbon veya sodyum bisülfit dozajlamasından (beslemeyi klordan arındırmak için yaygın yöntemler) sonra kullanılır. Besleme suyu SDI (silt yoğunluk indeksi) veya bulanıklık da dikkate alınır; RO partikülleri işlemesi gerekse de, EDI'ya kaçan herhangi bir kolloidal kirlenme reçine yatağını tıkayabilir. EDI besleme bulanıklığı genellikle <0,1 NTU'da tutulur.
Ürün Su Kalitesi İzleme: Birincil ürün parametresi özdirençtir (veya iletkenlik) . Yüksek direnç (MΩ·cm cinsinden) hedeftir; dirençteki herhangi bir düşüş bir performans sorunu olduğunu gösterir. EDI çıkışlarında çevrimiçi iletkenlik ve direnç ölçerler (25 °C'ye kadar sıcaklık telafili) kullanılır - örneğin, bir işlem için sürekli >15 MΩ·cm'lik bir okuma gerekebilir ve bunun altına düşerse alarmlar verilir. Özdirençteki ani düşüşler, besleme kirleticilerinde artış, reçinenin tükenmesi (akım yetersizse) veya sızıntıya neden olan yırtık bir membran gibi bir arıza anlamına gelebilir. Operatörler özdirenç eğilimlerini izleyerek kademeli kirlenmeyi veya kademeli değişiklikleri tespit edebilir. Kritik uygulamalarda, silika seviyeleri de ölçülür (örneğin, elektrik santrallerindeki çevrimiçi silika analizörleri tarafından), çünkü silika atılımı genel iletkenlik yükselmeden önce meydana gelebilir (silika zayıf iletkendir). Ek olarak, bazen ürün pH'ı izlenir; EDI ürün suyu, eser miktarda OH⁻ sızıntısı nedeniyle genellikle pH'ta (7–9) hafifçe yükselir, ancak ani bir pH değişimi katyon/anyon gideriminde dengesizliğe işaret edebilir (örneğin, anyon reçinesi tükenirse, CO₂ geçebilir ve pH'ı düşürebilir).
Konsantre Akış İzleme: Konsantre (reddedilen) akışı safsızlıkları taşır ve durumu EDI ömrünü etkileyebilir. Operatörler konsantre akış hızının tasarım dahilinde olduğundan emin olur ve genellikle konsantre iletkenliğini ve pH'ını izler. Çok yüksek bir konsantre iletkenliği aşırı iyon yükü veya yetersiz yıkama (konsantre odalarında tuzların çökelmesi riski) anlamına gelebilir. Konsantre pH'ının yüksek seyretmesi (suyun parçalanmasından kaynaklanan OH⁻ birikimi nedeniyle) kireçlenmeyi haber verebilir (bu iyonlar mevcutsa CaCO₃ veya Mg(OH)₂ veya SiO₂). Bazı sistemler gerekirse pH'ı kontrol etmek için konsantrenin küçük bir kısmını boşaltır veya asit dozlar. Ayrıca, belirtildiği gibi seyreltmeye göre hafif negatif farkı korumak için konsantre çıkış basıncı izlenir; bir konsantre akışı engellenirse veya vana yanlış ayarlanırsa yüksek basınç oluşursa, konsantre ürün tarafına geri zorlanabilir; kaçınılması gereken bir durumdur.
Akış Dengesi ve Geri Kazanım: Çalışma sırasında, seyreltik (ürün) akışının konsantre akışına oranı, spesifikasyona göre korunur. Ürün akışı artırılırsa, geri kazanımı aralıkta tutmak için konsantre akışı veya devridaim ayarlanması gerekebilir. Çoğu sistemde ürün, konsantre ve elektrot durulama akışlarında rotametreler veya akış sensörleri bulunur; bunlar düzenli olarak kontrol edilmelidir. Ürün suyunda düşük akış alarmı genellikle modülün yetersiz akışla çalışmasını önlemek için kurulur (bu, yerel ısınmaya ve reçine bozulmasına yol açabilir). Aslında, EDI modülleri genellikle kilitlemelerle korunur: akış çok düşükse DC akımını kapatmak için ürün (seyreltik) hattında minimum akış anahtarı ve aşırı basıncı önlemek için basınç tahliyeleri. Operatörler bu güvenlik kontrollerinin işlevsel olduğunu doğrulamalıdır. Önerilen akış dağılımını (örneğin ürün, konsantre veya elektrot yıkama) korumak önemlidir. Herhangi bir uzun süreli dengesizlik (elektrot durulamada akış olmaması gibi) modülün parçalarında kireçlenmeye veya kurumaya neden olabilir.
Elektriksel Parametreler: DC güç kaynağının çıkış akımı ve voltajı sürekli olarak izlenmelidir. Birçok EDI sisteminde amper göstergesi bulunur ve genellikle belirli bir akımda çalışır. Akım çekimi, ne kadar iyonik yükün işlendiğini yansıtır; besleme suyu kalitesi kötüleşirse, modül daha fazla akım talep edebilir (sabit voltaj modunda çalıştırılırsa) veya ürün kalitesi düşebilir (akım sınırlıysa). Tipik olarak, sistemler sabit akım modunda çalıştırılır: akım, besleme TDS için teorik minimumun üzerindeki bir değerde sabitlenir. Voltaj daha sonra maksimum değere kadar ihtiyaç duyulan değere yükselir. Operatörler voltajı takip eder: güç kaynağı sınırına yaklaşırsa, bu hücrelerin daha az iletken hale geldiğini gösterebilir (potansiyel kirlenme). Gerekli voltajda ani bir düşüş, bir sızıntı veya kısayol (direnç yolunun kaybı) belirtisi olabilir. Bazı sistemler hem akım hem de voltaj alarmlarını içerir. Ayrıca, performansın bir tanısı olarak akım verimliliğini (geçirilen akıma eşdeğer iyonik giderim oranı) periyodik olarak kaydetmek de iyi bir uygulamadır. Zamanla, eğer kireçlenme meydana gelirse, faydalı iyon giderimine giden akımın oranı azalabilir (daha fazlası suyun parçalanmasına gider), bu da konsantre iletkenliğindeki akıma göre değişikliklerden çıkarılabilir.
Kirlenme ve Kireçlenmeyi Önleme: Uzun ömürlü olmasını sağlamak için operatörler EDI'yi temiz tutmaya çalışırlar. Önarıtma bakımı önemlidir - örneğin, RO membranlarının çalıştığından ve aşırı sertlik veya organik madde geçirmediğinden emin olmak. Partiküllerin reçineyi kirletmesini önlemek için akış yukarısı kartuş filtreleri programa göre değiştirilmelidir. Organik kirlenme riski varsa (örneğin, beslemede yüksek TOC veya biyolojik içerik varsa), EDI'den önce bir UV lambası eklemek (organik bileşikleri oksitlemek için) veya periyodik dezenfeksiyonlar yapmak yardımcı olabilir. Bazı tesisler, biyofilmi önlemek için EDI'den periyodik olarak soğuk bir dezenfeksiyon solüsyonu (seyreltik NaOH veya özel bir biyosit gibi) tekrar dolaştırır, ancak elektrik alanı ve yüksek saflık koşulları mikroplar için uygun olmadığından ihtiyaç azalır.
Sürekli Kayıt: Modern EDI üniteleri basınçları, akışları, özdirenci, sıcaklıkları vb. kaydetmek için enstrümantasyona sahiptir. Bu kayıtların düzenli olarak incelenmesi, ince eğilimleri ortaya çıkarabilir; örneğin, haftalar boyunca yavaşça azalan bir ürün özdirenci, operatörün alarm seviyelerine ulaşmadan önce ele alabileceği kirlenmeye işaret edebilir. Kayıt ayrıca, bir sapma meydana gelirse sorun gidermede yardımcı olur.
Özetle, operatör bir EDI'yi bir RO veya diğer kritik su ünitesi gibi ele almalıdır - istikrarlı çalışma koşullarını koruyun, beslemeyi spesifikasyon dahilinde tutun ve parametrelerdeki herhangi bir alarma veya kaymaya derhal yanıt verin. Bunu yaparak, EDI sürekli olarak yüksek kaliteli su üretecek ve modüller beklenen kullanım ömürlerini koruyacaktır. Birçok sistem, özellikle ön işlem sağlamsa, rutin izleme dışında asgari müdahaleyle yıllarca çalışabilir.
EDI Sistemleri için Tasarım ve Kurulum Önerileri
Bir EDI sistemi kurmayı planlarken, başarılı bir entegrasyon ve işletim sağlamak için çeşitli teknik faktörlerin dikkate alınması gerekir:
Ön Arıtma Gereksinimleri: EDI tek başına bir arıtma adımı değildir; yükü azaltmak için akış yukarısı arıtmaya güvenir. Ters ozmoz, TDS'yi %90-99 oranında düşürerek uygun bir besleme sağladığı için EDI'dan önce hemen hemen her zaman gereklidir. Ek olarak, RO'yu (ve dolayısıyla EDI'yı) sertlikten korumak için akış yukarısı yumuşatma (iyon değişimi veya kireç önleyici dozajlama) gerekebilir. RO permeatından CO₂'yi ayırmak için bir gaz giderme ünitesi (membran gaz giderici veya karbon giderici) genellikle EDI üzerindeki iyonik yükü azaltmak için dahil edilir (bikarbonat oluşumunu önleyerek). Klor/oksidanları RO öncesinde gidermek için aktif karbon filtreleri veya kimyasal klor giderme zorunludur, böylece hiçbiri EDI'ya ulaşmaz . Esasen, beslemenin her zaman EDI üreticisi tarafından önerilen tüm kalite özelliklerini (iletkenlik, SDI, sertlik, silika, TOC, klor vb.) karşıladığından emin olun. Kaynak su kalitesi değişken ise, sağlam ön arıtma sistemleri ve muhtemelen yedeklilik sağlanmalıdır; EDI, tasarım zarfının ötesindeki sapmalara karşı hassastır.
Sistem Boyutlandırma ve Modül Yapılandırması: Gerekli ürün akış hızını belirleyin ve buna göre EDI modüllerinin sayısını ve boyutunu seçin. EDI modülleri çeşitli kapasitelerde gelir; örneğin, bazı modüller her biri ~2 m³/h üretir , bu nedenle daha büyük akış sistemleri paralel olarak birden fazla modül kullanır. Modüller ayrıca ekstra yüksek saflık için seri olarak da düzenlenebilir (daha az yaygın, çünkü RO'dan sonra genellikle bir modül yeterlidir). Sistem tasarımı, DC güç kaynağı (doğrultucu) ve kontrol paneli dahil olmak üzere EDI kızağı için yer ayırmalıdır. DC doğrultucu, gerekli voltajda tüm modüller için toplam akımı sağlayacak şekilde boyutlandırılmalıdır. Her biri 9 A'ya kadar 4 modül kullanılırsa, güç kaynağı beklenen voltajda ~36 A'yı kaldırabilmelidir (modül tasarımına bağlı olarak 100–300 VDC olabilir). Güç kaynağı kapasitesinde bir miktar genel gider olması akıllıca olacaktır. Topraklama dahil olmak üzere uygun elektrik tasarımı kritik öneme sahiptir; çalışma sırasında su ve ekipman toprağa göre yüksek voltajda olduğundan tüm borular ve modüller topraklanmalıdır . Operatör güvenliği için emniyet kilitleri (elektrik panolarındaki kapı anahtarları vb.) ve elektrik yönetmeliklerine uyulması zorunludur.
Hidrolik Entegrasyon: EDI modülleri genellikle besleme, ürün ve konsantre için manifoldlarla kızak üzerine monte edilir. EDI için besleme pompası (genellikle RO yüksek basınç pompası bir gaz kelebeği ile kullanılır veya bir destek pompası eklenir) gerekli akışı ve basıncı sağlamalıdır. Besleme pompasının EDI modüllerinin akış direncini aşmak için gereken akışı yaklaşık 40–80 psi'de (tipik çalışma basıncı) koruyabildiğinden emin olun. Ürün akışını ayarlamak için ürün hattında bir akış kontrol vanası veya akış ölçer kullanılır. Konsantre hattında genellikle oranı ayarlamak için bir akış veya sınırlayıcı bulunur. Konsantre akışını bertaraf etmek veya yeniden kullanmak için bir yol planlayın - örneğin hava boşluğu olan bir tahliye (konsantre az miktarda hidrojen gazı ve safsızlık içerebileceğinden) veya geri dönüşüm için RO besleme tankına göndermek için boru hattı (uygun kontrollerle). Konsantreyi geri dönüştürüyorsanız, içerdiği CO₂ veya silikayı RO beslemesine geri getireceğini ve muhtemelen RO geri kazanımında ayarlamalar veya geri dönüşüm döngüsünde bir gaz giderici gerektireceğini düşünün . Ek olarak, konsantre ve elektrot akımlarının elektrotlarda üretilen gazların (H₂, O₂) havalandırılması gerekebilir. Kurulum sırasında, hidrojen gazını güvenli bir şekilde havalandırmak ve birikmeyi önlemek için konsantre dönüş hattına genellikle havalandırma delikleri veya gaz giderme ayırıcıları takılır (güvenlik yönergelerine göre, H₂ herhangi bir kapalı alanda alt patlayıcı sınırının %25'inin altında kalmalıdır).
Malzeme Uyumluluğu: EDI döngüsünde suyla temas eden tüm malzemelerin uyumlu olduğundan ve iyon sızdırmayacağından emin olun. Genellikle, borular UPVC, polipropilen veya paslanmaz çeliktir. Pirinç, bakır veya iyon ekleyebilecek herhangi bir malzemeden kaçının. Ayrıca organik madde döken malzemelerden de kaçının. EDI modül malzemeleri (reçine, membranlar, muhafaza) üretici tarafından saflık açısından seçilir; sadece contaların, sistemin geri kalanındaki yapıştırıcıların da benzer şekilde temiz olduğundan emin olun. Uygulama farmasötikse, malzemelerin FDA uyumlu olması veya iz sızdırılabilir maddeler için doğrulanması gerekebilir.
Çevre ve Kurulum Yeri: EDI üniteleri, aşırı sıcaklıklardan ve güneş ışığından korunan iç mekanlara yerleştirilmelidir . Ortam sıcaklığı, modülün çalışma aralığında (10–38 °C) ve ideal olarak su sıcaklığını sabit tutmak için kontrollü bir odada kalmalıdır. Donma koşulları modülü tahrip edecektir (su genleşmesi), bu nedenle herhangi bir risk varsa, ısı izleme veya iç mekan kurulumu şarttır. Aynı şekilde, elektrikli ekipmanı korumak için yüksek nemli ortamlardan kaçınılmalıdır (bazı özelliklere göre maksimum %90 nem) . Titreşim en aza indirilmelidir; aşırı titreşim bağlantıları gevşetebileceği veya reçine paketlemesine zarar verebileceği için kızak sabit bir zeminde olmalıdır. Bakım erişimi için alan ayrılmalıdır - örneğin, gerektiğinde modülleri ayırmak ve değiştirmek için ve kimyasal temizlik ekipmanı bağlantıları için alan.
Enstrümantasyon ve Kontroller: İyi tasarlanmış bir EDI sistemi, tüm kritik parametreler için enstrümantasyon içerecektir. En azından şunlar için sensörler takın: besleme iletkenliği, ürün direnci, ürün akışı, konsantre akışı, besleme ve çıkış basınçları ve sıcaklık. Genellikle, işlem sıkı kontrol gerektiriyorsa, besleme pH'ı, ürün silikası vb. için isteğe bağlı sensörler dahil edilir. Kilitlemeler, EDI'yi yukarı akış RO'ya bağlamalıdır - tipik olarak EDI yalnızca RO permeatı spesifikasyona uygun ve akarken çalışır; RO kapalıysa veya su kalitesi kötüyse (örneğin yüksek iletkenlik), EDI kızağı onu korumak için baypas edilebilir veya kapatılabilir. Başlatma veya bakım sırasında suyu EDI etrafından yönlendirmek için bir baypas hattı ekleyin, böylece gerektiğinde kullanıcılara (daha düşük saflıkta olsa da) su sağlamaya devam edebilirsiniz. Kontrol sistemleri (PLC/HMI), EDI izleme ve alarmlarını genel su tesisi kontrolüne entegre edebilir. Yüksek ürün iletkenliği, düşük akış, yüksek basınç vb. için alarmlar, hasar meydana gelmeden önce operatörleri uyarmak veya modül gücünü kapatmak için ayarlanmalıdır. Enerji santrallerinde veya sürekli üretimde bu alarmlar tesis DCS'sine bağlanabilir.
Devreye Alma ve İlk Başlatma: Kurulumdan sonra, ilk devreye alma, sistemin RO süzüntüsüyle yıkanmasını, sızıntı olup olmadığının kontrol edilmesini ve ardından EDI modüllerine güç verilmesini içerir. Genellikle, yeni bir EDI modülünün en yüksek saflık çıkışına ulaşması biraz zaman alabilir (birkaç saatten bir güne kadar), çünkü reçinenin elektriksel rejenerasyon tarafından tamamen H⁺/OH⁻ formuna dönüştürülmesi gerekebilir. İlk başlatma sırasında, üreticiler bir döngüde su dolaştırılmasını ve ürün suyunu kullanmaya başlamadan önce birkaç saat boyunca yüksek akım uygulanmasını (elektro-rejenerasyon süresi) önerebilir. Örneğin, yeni bir modülün 16+ MΩ·cm kalitesine ulaşması için 8-24 saatlik bir ilk rejenerasyon gerekebilir . Bu devreye alma adımını planlamak, üretim programlarının bunu hesaba katması için önemlidir. Bundan sonra, su gönderilebilir (genellikle laboratuvar testleriyle kalite doğrulandıktan sonra).
Tasarım/kurulum aşamasında tüm bu faktörleri göz önünde bulundurmak güvenilir EDI çalışması için ortamı hazırlayacaktır. Besleme suyu sınırları, tesisat ve elektrik bağlantısı konusunda tedarikçinin yönergelerini takip etmek kritik öneme sahiptir. Her EDI modül modeli, bu gereklilikleri belirten ayrıntılı bir kılavuza sahip olacak ve bunlara uyulması (örneğin ön filtre derecelendirmeleri, pompa boyutlandırma, elektrik kablolama uygulamaları) sistemin amaçlandığı gibi çalışmasını ve garantilerin geçerli kalmasını sağlayacaktır.
Bakım, Sorun Giderme ve Modül Ömrü
EDI'nin avantajlarından biri, kimyasal olarak yenilenen iyon değiştiricilere kıyasla rutin bakımın azalmasıdır. Ancak, EDI sistemleri yine de yıllarca süren operasyonlarda performansı sürdürmek için dikkatli bakım ve ara sıra müdahale gerektirir. Aşağıda bakım prosedürleri, sorun giderme ipuçları ve modül ömrü beklentileri verilmiştir:
Rutin İzleme ve Önleyici Bakım
Operasyonel değerlendirmelerde tartışıldığı gibi, kalite ve sistem parametrelerini sürekli olarak izleyin. Kayıt tutun ve eğilimleri arayın. Günlük/Vardiya kontrolleri , ürün özdirencini, besleme iletkenliğini, akışları, basınçları ve akım/voltajı kaydetmeyi içerebilir. Alarm veya sapma olmadığından emin olun. Aletlerin işlevini düzenli olarak doğrulayın (iletkenlik/özdirenç ölçerleri vb. programa göre kalibre edin). Ayrıca, konsantre reddini görsel olarak inceleyin - herhangi bir çökelme belirtisi arayın (reddetme akışında veya reddetme nozulunda bulanıklık veya kireç) ve konsantre borularını veya deliklerini tıkanıklık açısından kontrol edin. Ayrı bir elektrot durulama akışı kullanılıyorsa, akışını ve çıkışının tıkalı olmadığını kontrol edin (elektrot durulama genellikle tahliye veya besleme tankına geri gider; tıkalıysa gaz birikmesi meydana gelebilir). Normal çalışmada, EDI modülleri küçük kirlilikleri kendi kendine temizler (sürekli iyon yıkaması nedeniyle), ancak önleyici bakım beslemeyi spesifikasyonda tutmaya odaklanır - örneğin, ön filtreleri (5 mikron veya 1 mikron filtreler) düzenli olarak değiştirin, akış aşağı EDI'yi korumak için gerektiğinde RO'ya servis verin (temizlikler, membran değişimi).
Temizlik Prosedürleri
Zamanla, ürün direncinde kademeli bir düşüş veya basınç düşüşünde bir artış gibi performans sorunları, EDI modüllerinin temizlenmesini gerektiren kirlenme veya kireçlenme belirtisi olabilir. EDI sistemleri, seyreltik ve konsantre bölmelerde uygun temizleme kimyasallarının dolaştırılmasıyla temizlenebilir (CIP - Yerinde Temizleme'ye benzer). Temizleme solüsyonunun seçimi, kirletici türüne bağlıdır:
Kireçlenme (kalsiyum karbonat veya metal hidroksitler gibi mineral birikintileri)
Önerilen temizlik genellikle seyreltik bir asittir. Örneğin, ~%2 hidroklorik asit (HCl) veya sitrik asit Ca/Mg ölçeğini çözebilir. Asitle temizlik reçineyi geçici olarak tuz formlarına dönüştürecektir, ancak bu yeniden çalışma sırasında geri yüklenir.
Organik veya Biyolojik kirlenme, Silika birikintileri
Bu durumda yüksek pH'lı bir temizlik kullanılır. Yaklaşık %1 oranında seyreltik bir kostik soda (NaOH) çözeltisi genellikle organik maddeyi veya biyofilmi çıkarmak ve silika birikintilerini çözmeye yardımcı olmak için etkilidir. Kostik reçineden organik asitleri elüe eder ve biyofilmleri hidrolize eder. Bazen karışık kirleticilerden şüpheleniliyorsa bir kombinasyon temizliği yapılır (kostik ardından asit), ancak reaksiyonu önlemek için kimyasallar arasında iyice durulama yapılmalıdır (örneğin asit + baz karışımı).
Fiziksel yıkama
Kimyasallara ek olarak, deiyonize suyla yüksek akışlı bir yıkama, gevşek bir şekilde sıkışmış partiküllerin veya reçine ince parçalarının (varsa) yerinden oynatılmasına yardımcı olabilir. Hızların reçine yatağına zarar vermediğinden emin olun, ancak temizlik sırasında döküntüleri çıkarmak için akışta geçici bir artış kullanılabilir.
Temizlik işlemi genellikle, temizlik kimyasallarıyla herhangi bir elektrokimyasal reaksiyona girmemesi için DC güç kapalıyken (akım yokken) gerçekleştirilir. Prosedür, temizleme solüsyonunu modüller arasında (genellikle hem seyreltik hem de konsantre tarafları aynı anda) belirli bir süre (örn. 30-60 dakika) dolaştırmak ve ardından yüksek saflıkta suyla iyice yıkamaktır. Güç açıldığında kalan asit veya kostik reçineye veya membranlara zarar verebileceğinden, tüm temizlik maddelerini durulamak kritik öneme sahiptir . Durulamadan sonra, modüllerin genellikle tekrar elektriksel olarak "yenilenmesi" gerekir - yani, ürün kalitesi spesifikasyonlara dönene kadar EDI'yi bir döngüde taze RO suyuyla normal veya hafif yükseltilmiş akımda çalıştırın. Operatörler, ürün direncinin ve diğer parametrelerin temizleme öncesi değerlerle eşleştiğini veya bunları iyileştirdiğini kontrol ederek temizleme sonrası performansı doğrular. Tüm temizleme olayları, nedeni (örn. basınç düşüşü artışı, iletkenlik artışı) ve sonuçları belirterek bakım günlüklerine belgelenmelidir, çünkü bu gelecekteki bakım planlamasını optimize etmeye yardımcı olur.
Yaygın Sorunların Giderilmesi
Azalmış Ürün Kalitesi (Düşük Direnç)
Bu, sorun gidermeyi tetikleyen en yaygın sorundur. Direnç düşerse, önce besleme suyunu kontrol edin - iletkenlik veya CO₂ aniden arttı mı? Öyleyse, beslemeyi ele alın (RO sorunları, vb.). DC akımının ayar noktasında olduğundan emin olun; bir güç kaynağı arızası veya operatör hatası akımı çok düşük yapabilir. Ayrıca konsantre akışını inceleyin - konsantre veya elektrot durulama akışları durduysa (örneğin bir pompa veya valf sorunu nedeniyle), modülde iyonlar birikmiş olabilir. Çözüm, akışları geri yüklemek ve muhtemelen kurtarmak için bir süre yeniden dolaştırmak olacaktır. Besleme ve akışlar iyiyse, sorun kirlenme olabilir: örneğin, reçine üzerindeki organik kirlenme değişim verimliliğini azaltacaktır. Bu durumda, bir temizlik planlayın (genellikle organikler için kostik bir temizlik). Temizledikten sonra kaliteyi yeniden test edin. Kalite hala düzelmiyorsa, geri döndürülemez bir hasara (reçine oksidasyonu veya zehirlenmesi gibi) işaret ediyor olabilir. Bu noktada, modülün değiştirilmesi gerekebilir.
Artan Basınç Düşüşü
EDI modülündeki basınç önemli ölçüde artarsa, akış kanallarında (reçine veya ara parçalar) tıkanıklık olduğunu gösterir. Muhtemel suçlular: partikül kirlenmesi veya kireçlenme. Besleme SDI/filtre durumunu kontrol edin. Kireçlenmeden (örn. CaCO₃) şüpheleniliyorsa, asit temizliği yapılmalıdır. Partikül varsa, bazen basit bir yüksek akışlı yıkama döküntüyü dışarı itebilir. Hiçbir vananın kısmen kapalı olmadığından emin olun. Sürekli yüksek diferansiyel basınç reçine yatağını sıkıştırabilir ve performansı daha da düşürebilir, bu nedenle derhal çözülmelidir. Aşırı durumlarda, bir kanal kalıcı olarak tıkalıysa modülün sökülmesi (mümkünse) veya değiştirilmesi gerekebilir. Üreticinin EDI reçine aralıklarının partiküllere maruz kaldığında hızla tıkanıp performansı düşürebileceği uyarılarında da belirtildiği gibi, uygun ön filtreleme yoluyla önleme önemlidir.
Elektriksel Anomaliler (Yüksek Voltaj veya Devreler)
Sistemin voltajı ayarlanan akımda aniden normalin üzerine çıkarsa, bu, yığın direncinin arttığını gösterir - muhtemelen membranlardaki kireçlenme veya reçinenin susuz kalması nedeniyle. Bir membrandaki kireç tabakası iyon akışını engeller ve direnci yükseltir; çözüm kimyasal temizliktir (kirece bağlı olarak uygun asit veya baz). Reçine kurutma (örneğin, bir EDI yanlışlıkla bir süre su akışı olmadan çalıştırılırsa veya uygunsuz şekilde saklanırsa) temas kaybına neden olabilir; kurumuş reçine için tek çözüm genellikle çatlaklar ve hava cepleri oluştuğu için değiştirmedir. Güç kaynağı devreden çıkıyorsa, herhangi bir topraklama sorunu veya kısa devre olup olmadığını kontrol edin - yaygın bir neden, elektrik konektörlerine su sızması veya doğrudan elektrot kısa devresine neden olan kırık bir membrandır. Bunun için fiziksel inceleme ve muhtemelen modül onarımı veya değişimi gerekir.
Reçine Sızıntısı
Normal çalışmada nadir görülse de, modüldeki bir conta arızalanırsa, borularda veya aşağı akıştaki filtrelerde reçine boncukları görebilirsiniz. Bu, dahili bileşen arızası meydana geldiğinden modülün çevrimdışı hale getirilmesini ve onarılmasını veya değiştirilmesini gerektirir.
Ürün Suyu pH'ı Normal Sınırların Dışında
Ürün pH'ı alışılmadık bir şekilde nötrden uzaklaşırsa, bu bir dengesizliğe işaret ediyor olabilir (örneğin yalnızca katyon giderimi gerçekleşirken anyon giderimi gerçekleşmez veya tam tersi). Bu, bir membran türü hasar gördüğünde veya bir reçine türü kirlendiğinde meydana gelebilir. Örneğin, anyon reçinesi kirlendiğinde, silika veya CO₂ geçebilir ve pH'ı düşürebilir. Çözünürlük, bu belirli kirlenmeyi hedef alır (sık sık anyon reçinesini kirleten organikler için kostik temizleme).
Sorun gidermede sistematik bir yaklaşım en iyisidir: besleme kalitesini doğrulayın, sonra modül çalışma koşullarını (akışlar, akım, vb.) kontrol edin, sonra bir temizlik yapmayı düşünün ve bu başarısız olursa, modülleri tek tek test ederek sorunu belirli bir modüle (çok modüllü sistemlerde) izole edin. Birçok EDI sisteminde birden fazla modül bulunur; her birinin performansını karşılaştırarak (tek tek ölçümler mevcutsa), tek bir modülün sorunlu olup olmadığını belirleyebilir ve belki de son çare olarak onu değiştirebilirsiniz.
Beklenen Modül Ömrü
Uygun bakımla, EDI modülleri uzun bir hizmet ömrüne sahiptir. Aynı modülleri değiştirmeden 5-10 yıl veya daha fazla çalıştıran kurulumlar vardır. Besleme suyunun sürekli olarak özellikler dahilinde olduğu ve düzenli bakım yapıldığı varsayılarak, tipik beklenen ömür genellikle 5 yıldan fazla sürekli çalışma olarak belirtilir. Bazı durumlarda, reçine veya membran bozulması değiştirilmesini gerektirene kadar modüller bundan çok daha uzun süre dayanabilir ("uzun yıllar") . Bir EDI modülünün ömrünü genellikle sonlandıran faktörler şunlardır: geri döndürülemez kirlenme (organiklerden, silikadan, vb.), reçine oksidasyonu (bir klor olayı veya yıllarca eser miktarda maruz kalma sonucu kapasite kaybına neden olması) veya fiziksel bozulma (membran yaşlanması, conta sızıntıları). Ürün suyunun kalitesi, kapsamlı temizlik ve yenilemeden sonra bile artık korunamıyorsa, bu modülün değiştirilmesi gerektiğinin bir işaretidir. Ömrünü en üst düzeye çıkarmak için: mükemmel ön işlem uygulayın (oksidan yok, düşük TOC, vb.), modülü ani akış veya güç değişiklikleriyle şoklamayın, gereksiz kapatmalardan kaçının (sık sık durdurmak yerine mümkünse düşük yükte çalıştırın) ve modülü her zaman ıslak tutun. Bir EDI modülünün depolama veya kapatma sırasında kurumasına asla izin vermeyin, çünkü bu reçineye ve membranlara kalıcı olarak zarar verebilir. Bir EDI uzun süre çevrimdışı kalması gerekiyorsa, üretici talimatlarına göre saklanmalıdır - genellikle suyla (veya koruyucu bir solüsyonla) dolu tutulmalı ve kapatılmalıdır. Bazıları reçineyi yenilenmiş formda tutmak için periyodik olarak yeniden sirkülasyon yapılmasını veya uzun süre kullanılmadığında modüle kısa bir süre güç verilmesini önerir. Üreticiler genellikle modüllerin ıslak halde aylarca saklanabileceğini belirtir; örneğin, DuPont modüllerin uygun önlemlerle orijinal ambalajında altı aya kadar saklanabileceğini belirtir.
Bir modül kullanım ömrünün sonuna ulaştığında, değiştirme işlemi modülün basıncını düşürmeyi ve izole etmeyi, elektrik ve tesisat bağlantılarını kesmeyi ve yeni bir modül takmayı içerir. Yeni modül normal başlatma prosedürünü (yıkama ve ilk rejenerasyon periyodu) gerektirecektir. Kesinti süresinin kritik olacağı sistemler için yedek bir modülü (veya en azından yedek güç kaynağı, ekstra contalar gibi kritik yedekleri) elinizde bulundurmak iyi bir uygulamadır. Ancak, iyi bir çalışmayla, gerçek modül değiştirmeleri seyrek olmalıdır.
Özetle EDI bakımı, tutarlı çalışma ve önarıtma yoluyla sorunları önlemeye ve ortaya çıkarsa kirlenmeyi erken ele almaya odaklanır. Sık sık kimyasal rejenerasyon veya reçine değişimi gerektiren iyon değişim tanklarıyla karşılaştırıldığında, EDI daha müdahalesiz bir çalışma sunar. Ancak hiçbir şekilde bakım gerektirmez - su arıtma profesyonelleri buna dikkat etmeli ve periyodik temizlik ve kontroller yapmalıdır. Uygun şekilde bakımı yapıldığında, EDI modülleri güvenilir bir şekilde çalışır ve sistem minimum müdahaleyle sürekli olarak çalışabilir ve yüksek saflıkta suyun sabit bir akışını üretebilir.
EDI Modül Tasarım ve Teknik Özellikleri
Çeşitli üreticilerin EDI modülleri yapı detaylarında farklılık gösterebilir, ancak ortak tasarım öğelerini paylaşırlar. Genel tasarımı ve tipik özellikleri anlamak, EDI sistemlerini değerlendirmeye ve karşılaştırmaya yardımcı olur:
Yapı ve Malzemeler
Çoğu elektrodeiyonizasyon veya edi modülü, ürün suyu ve atık suyun ayrı bölümlerde bulunduğu, plaka ve çerçeve veya yığın yapılandırmasında tasarlanmıştır. Tipik malzemeler arasında PVC veya polipropilen çerçeveler, immobilize sülfonik (katyon) veya kuaterner amonyum (anyon) grupları içeren levha polimerlerinden yapılmış iyon değişim membranları ve karışık yataklı iyon değişim reçinesi (boncuk formunda güçlü asit katyonu, güçlü baz anyon reçineleri) bulunur. Uç plakalar yığını bir arada tutar ve elektrotlar (genellikle kaplanmış titanyum veya paslanmaz çelik gibi inert malzemelerden yapılır) uçlara yerleştirilir. Bazı tasarımlar, örneğin belirli silindirik EDI modülleri (örneğin DuPont'tan), bir silindir içindeki konsantre için spiral sarılı bir akış yolu kullanır, ancak yine de dahili olarak yığılmış membranlardan ve reçineyle doldurulmuş bölmelerden oluşur. Tüm ıslatılmış malzemeler yüksek saflık ve uyumluluk için seçilir; örneğin, reçineler yüksek oranda rejenerasyona tabi tutulup düşük TOC değerine sahip olacak şekilde durulanır, membranlar elektrodiyalizde kullanılanlara benzerdir (uzun ömürlüdür ve biyolojik kirlenmeye karşı dirençlidir).
Karma Yatak Reçinesi
Her seyreltik bölmenin içinde, karışık iyon değişim reçinesi sıkıca doldurulur. Reçine tipik olarak iletkenlik ve su ayrışması için optimize edilmiş belirli bir katyon-anyon reçinesi oranına sahiptir (genellikle hacimce 40:60 veya 50:50). Reçine boncukları birincil deiyonizasyon eylemini ve ayrıca elektrik akımı için bir yol sağlar (su tek başına deiyonize edildiğinde çok dirençli olacağından. Reçine yatağı ayrıca hücrenin ön kısmında numune iyonik iletkenliği sağlayarak ve daha sonra yerelleştirilmiş yüksek alan bölgeleri oluşturarak ikinci kısımda su ayrışmasını kolaylaştırarak ihtiyaç duyulana kadar su ayrışmasını önlemeye yardımcı olur. Reçine boncuk boyutu ve türü performansı etkileyebilir (daha ince reçine daha fazla değişim noktası sağlayabilir ancak daha yüksek basınç düşüşüne neden olur; çoğu performans dengesi için düzgün ince gözenekli reçine kullanır).
İyon Değişim Membranları
Her hücre, katoda bakan tarafta bir katyon değişim membranı (CEM) ve anoda bakan tarafta bir anyon değişim membranı (AEM) ile sınırlanmıştır . Bu membranlar genellikle karşı iyonların seçici geçişine izin veren ince tabakalardır (0,1–0,5 mm kalınlığında). Membranlar eş iyon sızıntısını önleyerek seyreltikten uzaklaştırılan iyonların konsantrede kalmasını sağlar. Membranların kalitesi (seçicilik ve direnç) yığın verimliliğini etkiler – esasen hiçbir ürün suyu iyonunun geri yayılmaması için yüksek seçiciliğe ihtiyaç vardır. Membranlar genellikle fonksiyonel gruplara sahip polistiren-divinilbenzen gibi kararlı polimerlerdir (CEM için–SO₃⁻, AEM için –NR₃⁺). Genellikle mukavemet için kumaşla güçlendirilirler. Membran aralığı, akış kanallarını da tanımlayan contalar veya ara parçalar tarafından korunur.
Akış Dağıtımı
Her bölmede, türbülans yaratmak ve akış dağılımını sağlamak amacıyla ara parçalar veya ağ olabilir. Bazı tasarımlar boşluğu doldurmak için yalnızca reçine kullanır (reçine ara parça görevi görür), diğerleri reçineyi yerinde tutan ve akışı yönlendiren bir ağ veya elek içerir. "Tamamen dolu" tasarımlar, reçineyle doldurulmuş bölmelerin hem seyreltilmesini hem de konsantre edilmesini ifade eder. Konsantre bölmelerini reçineyle doldurmak (açık akış olarak bırakmak yerine) iletkenliği iyileştirebilir ve konsantredeki iyonları değiştirerek ölçeklenmeyi azaltabilir . Birçok modern EDI modülü, daha iyi verimlilik için tamamen dolu tasarımları benimser.
Elektriksel Yapı
Modüllerin iki elektrodu vardır: anot (pozitif, genellikle besleme giriş ucunda veya belirlenmiş bir uçta) ve katot (negatif, karşı uçta). Bir DC güç kaynağına bağlanırlar. Akım yolu anottan, konsantre/seyreltik bölmelerinden (iyonlar ve reçine yoluyla) katoda gider. Çoğu modül elektrot bölmelerini ana akıştan ayrı olarak ele alır: elektrot odaları, elektrot reaksiyonlarının ürünlerini (katotta H₂ gazı, O₂ ve muhtemelen klorür varsa anotta Cl₂ gazı) taşımak için aynı suyun küçük bir akışıyla (genellikle elektrot durulama veya elektrolit yıkama olarak adlandırılır) beslenebilir. Bu elektrot durulama akışı genellikle konsantrenin bir kısmı veya ayrı bir beslemedir; atık olarak çıkar. Kablolama açısından, birden fazla modül aynı güç kaynağına paralel olarak (her biri aynı voltajı görür) veya bazen daha yüksek voltaj dağılımı için seri olarak bağlanabilir - ancak düzgün performans için paralel daha yaygındır.
Tipik Performans Özellikleri
EDI modülleri akış kapasitesi, ürün kalitesi ve diğer operasyonel sınırlara göre derecelendirilir. Örneğin, tek bir modül şunlar için belirtilebilir: Ürün akışı 6–10 gpm (1,4–2,3 m³/h), tasarım besleme koşullarında ≥15 MΩ·cm özdirenç üretir. Geri kazanım (ürün/besleme), besleme sertliğine bağlı olarak %90–95'e kadar çıkabilir . Reddetme açısından, EDI genellikle besleme iyonlarının >%99'unu giderir; besleme <20 µS/cm olduğunda ürün iletkenliği <0,1 µS/cm olabilir. Birçok satıcı, EDI'larının örneğin 1–2 ppm TDS içeren RO süzüntüsünden 16–18 MΩ·cm su üretebileceğini belirtecektir. Besleme <1 ppm olduğunda üründeki silika genellikle <0,1 ppm'dir. Çalışma sıcaklığı aralığı genellikle 5–35 °C'dir (en iyi performans ortam ~20–25 °C yakınında). İzin verilen besleme basıncı ~6–7 bar'a (90–100 psi) kadar olabilir ve modül başına tipik basınç düşüşü yaklaşık 1–2 bar'dır (15–30 psi). Basınç düşüşü ~3 bar'ın ötesine çıkarsa temizlik belirtilir. Modüller ayrıca maksimum besleme sertliğini, silikayı, CO₂'yi ve kloru niceliksel olarak belirtir (örneğin sertlik <1 ppm CaCO₃ olarak, silika <1 ppm, serbest klor <0,05 ppm, TOC <0,5 ppm, vb.). Performans garantilerini elde etmek için bu özelliklere uyulması gerekir.
Güç Tüketimi
EDI, elde edilen saflık seviyesi için nispeten enerji verimlidir. Tipik güç kullanımı, besleme iletkenliğine bağlı olarak metreküp ürün başına 0,1-0,3 kWh mertebesinde olabilir. Örneğin, literatür 50 µS/cm'den 10 MΩ·cm'ye suyu deiyonize etmek için 1000 galon (3,8 m³) başına yaklaşık 1 kWh olduğunu göstermektedir . Bu, kabaca 0,26 kWh/m³'e karşılık gelir, ancak besleme TDS'si daha yüksekse veya ultra yüksek saflık (18 MΩ·cm) gerekiyorsa (suyun bölünmesi için daha fazla akım nedeniyle) enerji kullanımı artar. Modül başına akım 100-150 V'ta ~10 A'ya kadar çıkabilir, bu nedenle her modül 1 kW mertebesinde tüketebilir. Çok modüllü sistemlerde, güç modül sayısına göre ölçeklenir.
Modül Yerleşimi ve Bağlantılar
EDI modülleri boyut olarak değişebilir. Bazıları ~8-12 inç çapında ve birkaç fit yüksekliğinde silindirik ünitelerdir (bunlar genellikle içlerinde spiral bir yığın içerir), yaklaşık 50 kg ağırlığındadır. Diğerleri bir rafta birbirine cıvatalanan dikdörtgen kutulardır . Tipik olarak, her modülde besleme girişi, ürün çıkışı, konsantre çıkışı ve bazen konsantre girişi (eğer sirkülasyon dahili ise) ve elektrot besleme girişi/çıkışı için konektörler bulunur. Kızak tasarımları genellikle bunları çok sayıda ayrı modül bağlantısı yerine birkaç birleşik boru ile uğraşması için çeşitlileştirir. Modül değişimini kolaylaştırmak için genellikle hızlı bağlantı kesme kelepçeleri veya birleşimler sağlanır. Güç kaynağından gelen elektrik kabloları her modülün elektrotlarına (seri veya paralel) bağlanır. Bunlar yalıtılmalı ve genellikle ıslak yüzeylerle teması önlemek için suyla soğutulmalı veya dikkatlice yönlendirilmelidir.
Tasarım Çeşitleri
Temel prensip aynı olsa da bazı üreticilerin tescilli tasarımları vardır. Örneğin, bazıları seyreltik bölmelerin çok ince olduğu, iyonların yayılması gereken mesafeyi azaltan "ince hücre" teknolojisini kullanır, bu da verimliliği artırabilir ve biraz daha yüksek besleme kirliliğine (daha yüksek silika toleransı gibi) izin verebilir. Diğerleri , voltajı daha iyi kullanmak için bir modülün dahili olarak elektriksel olarak seri olarak segmentlere bölündüğü segmental tasarımlara sahiptir. Son yenilikler arasında, teması iyileştirmek ve basınç düşüşünü azaltmak için reçine gofretler veya katmanlı reçine-membran yapıları (reçinenin katı gözenekli bir disk veya tabakaya bağlandığı) yer alır. Ancak, bunlar gelişmiş varyasyonlardır ve henüz tüm endüstrilerde ana akım değildir. Standart modüller benzer performans zarflarına sahip olacaktır.
Yardımcı Ekipmanlar
Bir elektrodeiyonizasyon ünitesi, AC şebekesinden aldığı enerjiyi çevirerek, gerekli voltaj/akımda DC çıkışı veren bir DC güç doğrultucusu içerecektir. Modern üniteler katı haldir ve akımı ayarlamak için sistem PLC'si tarafından kontrol edilebilir. Ünitede ayrıca bir kontrol paneli ve muhtemelen işletim için HMI'lı bir PLC bulunacaktır. Ek olarak, yerinde temizleme (CIP) bağlantıları sıklıkla dahil edilir - temizleme solüsyonunun modüller arasında dolaşmak üzere sokulabileceği portlar. Konsantre hattındaki basınç tahliye vanaları (membranları aşırı basınçtan korumak için) ve gazlar için havalandırma delikleri gibi güvenlik özellikleri daha önce belirtilmişti.
Teknik veri sayfalarında şu gibi özellikler görebilirsiniz: "Ürün su kalitesi: ≥16 MΩ·cm; Silika sızıntısı: <0,020 mg/L; CO₂ giderimi: %90; Nominal geri kazanım: %90; Besleme gereksinimleri: <30 µS/cm, <0,5 ppm sertlik, SDI<1, 5–35 °C; Güç: hücre çifti başına 48 V, 5 A" vb. Bunlar, tasarım hedefleri ve sınırları hakkında bir fikir verir. Tam sayılar modele ve üreticiye göre değişir, ancak eğilimler benzerdir: çok yüksek ürün saflığı , sıkı besleme sınırları ve kireçlenmeyi en aza indirirken iyon giderimini en üst düzeye çıkaran bir tasarım.
Son olarak, EDI modüllerinin genellikle nispeten temiz ortamlarda yüksek saflıkta su için çalıştırıldığını belirtmekte fayda var; bu nedenle mekanik aşınma minimumdur. Zamanla en olası değiştirmeler iyon değişim reçineleri (bozulabilir) ve membranlardır. Bazı modül tasarımları yenilemeye (içindeki reçine veya membranları değiştirmeye) izin verir, ancak çoğu fabrikada kapatılmıştır ve performans tükendiğinde tüm modül değiştirilir. Bir EDI sistemi seçerken, destek ve yedek parçaların mevcudiyeti ve modül tasarımının itibarı (güvenilirlik ve bakım kolaylığı açısından) ilk performans özellikleri kadar önemlidir.
Mühendisler, EDI proses aşamalarını anlayarak ve çalışma parametrelerinin kontrolünü sürdürerek, bir elektrodeiyonizasyon sisteminin minimum kesinti süresiyle sürekli olarak ultra saf su üretmesini sağlayabilir. EDI, modern endüstride ihtiyaç duyulan en yüksek kalitelere kadar suyu parlatmak için ikna edici bir çözüm sunar; kimyasal içermeyen rejenerasyon, sürekli çalışma ve düzgün bir şekilde tasarlanıp yönetildiğinde kanıtlanmış güvenilirlik sunar.
Bizi tercih edenler
Su yumuşatıcılarımıza güvenen güvenilir markaları keşfedin ve tüm referanslarımıza tek bir tıklama ile ulaşın.
Tüm referanslarımıza göz atın