Kataforez Kaplama Prosesleri için Su Arıtma Çözümleri
Kataforez kaplama en yaygın olarak otomotiv sektöründe, araç gövdelerinin ve parçalarının korozyona karşı korunması amacıyla uygulanır. Otomotivde genellikle ana boyama işlemlerinin ilk katmanı olarak, metal yüzeyde yüksek yapışma ve korozyon direnci sağlayan astar (primer) görevini görür. Bunun yanı sıra, yöntemin kompleks şekilli parçalarda dahi uniform ve tam kaplama yapabilme kabiliyeti sayesinde farklı sektörlerde de geniş kullanım alanı bulmuştur.
Örneğin tarım ve iş makinaları, kamyon ve otobüs şasi ve parçaları, beyaz eşya ve dayanıklı tüketim malları, elektrik panoları ve şalt ekipmanları, metal ofis mobilyaları, bahçe ekipmanları, denizcilik sektörü komponentleri, bağlantı elemanları (cıvata, somun vb.) ve benzeri birçok alanda kataforez kaplama kullanılmaktadır. Bu sektörlerde, parçaların atmosferik koşullara (nem, tuzlu su, vb.) karşı dayanımını artırmak ve uzun ömürlü korozyon koruması sağlamak için kataforez kaplama önemli bir işlem haline gelmiştir. .
Örneğin, kataforez kaplama ile kaplanmış çelik, alüminyum veya magnezyum parçalar tuz püskürtme testinde en az 1000 saat boyunca korozyona karşı direnç gösterebilmekte ve gerçek kullanımda 6-12 yıl ilave paslanmazlık ömrü sağlayabilmektedir. Bu üstün koruma nedeniyle kataforez, tek başına kullanıldığı gibi (özellikle şasi, alt gövde gibi bölgelerde uygulanan “siyah kataforez” astarı çoğunlukla üzeri yaş boya veya toz boya son katlarla desteklenerek komple bir boyama sisteminin parçası haline gelir
Kataforez Kaplama Proseslerinde Kullanılan Su Arıtma Sistemleri
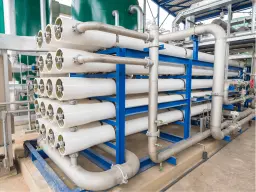
Ters Ozmoz
Çözücü kirleticileri ortadan kaldırmak için yarı geçirgen membranlar kullanır, kataforez prosesleri için yüksek saflıkta su sağlar.
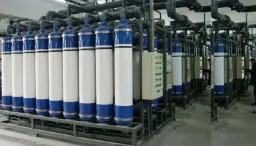
Ultrafiltrasyon
Asılı katı maddeleri ve kolloidləri bir ön işlem adımı olarak giderir, gerikazanım ve yeniden kullanım performansını artırır.
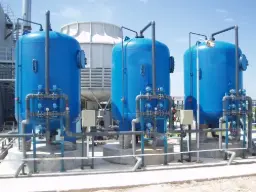
Su Yumuşatma
Kalsiyum ve magnezyumu sodyum ile değiştirir, tortu birikimini önemli ölçüde azaltır.
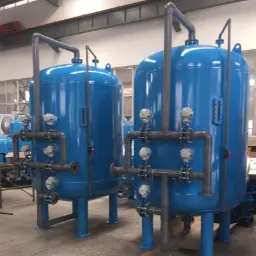
Deiyonizasyon
İyon değişim reçineleri kullanarak neredeyse saf su üretir, zararlı kirleticileri en aza indirir.
Kataforez Kaplama Nedir?
Kataforez kaplama, elektroforetik kaplama olarak da bilinen, elektrik akımı yardımıyla boya parçacıklarının iletken bir yüzeye çökertilmesi esasına dayanan bir yüzey koruma yöntemidir (). Bu yöntem, sıvı bir boya banyosunda askıda duran reçine ve pigment parçacıklarının, uygulanan doğru akım etkisiyle metal yüzeye üniform bir film halinde birikmesini sağlar. İlk elektroforetik boyama patenti 1917 yılında alınmış olsa da , endüstriyel uygulamalarına 20. yüzyıl ortalarında başlanmıştır. Özellikle 1960’larda anodik elektro-kaplama (anoforez) teknikleri küçük parçalarda uygulanmaya başlamış, ancak anodun parça olması nedeniyle metal yüzeyde çözünme ve korozyon sorunları görülmüştür. Bu sorunları gidermek için geliştirilen katodik elektro-kaplama teknolojisi (kataforez), ilk kez 1970 yılında PPG Industries (ABD) tarafından ticari bir tesis olarak tanıtılmış ve otomotiv endüstrisinde ilk defa 1975’te kullanılmıştır (). 1978’de Avrupa’da ilk otomobil karoserisi kataforez astar ile boyanmış (Fransa’da Chrysler fabrikası) ve o tarihten sonra süreç hızlı bir gelişim göstermiştir. Günümüzde kataforez boyama işlemi çevresel açıdan temiz (ağır metal içermeyen), ekonomik ve üstün korozyon koruması sağlayan bir teknoloji haline gelmiştir. Modern kataforez boyalar, önceki nesillere göre daha çevre dostu (ör. kurşunsuz) ve düşük uçucu organik bileşen (VOC) içerikli olacak şekilde geliştirilmiştir. Ayrıca kaplama işleminin verimi ve performansı yıllar içinde sürekli artmış; örneğin 1980’lerde 6 yıl civarı olan otomotiv gövde paslanmazlık garantileri günümüzde 10-12 yıla çıkmıştır
Kataforez Kaplama Prosesi Adımları
Kataforez kaplama prosesi, genellikle üç ana aşamada ele alınır: (1) Yüzey hazırlığı, (2) Elektro-kaplama (kataforez) uygulaması, (3) Kürleme (fırınlama). Bu aşamaların detayları ve alt adımları aşağıda açıklanmaktadır.
Yüzey Hazırlama (Temizleme ve Fosfatlama)
Kataforez kaplama işlemine başlamadan önce parçaların yüzeyi uygun şekilde hazırlanmalıdır. Yüzey hazırlığı, parçanın üzerinde bulunabilecek yağ, kir, toz, pas ve oksit tabakası gibi kalıntıların giderilmesini ve yüzeyin kaplamaya elverişli hale getirilmesini amaçlar. Tipik bir yüzey hazırlama prosesi çok kademeli kimyasal banyolar içerir:
Yağ alma (alkali temizleme): Parçalar ilk adımda bir veya birden fazla kademede deterjan/alkali kimyasallarla temizlenerek üzerlerindeki yağ ve kir tabakası uzaklaştırılır. Bu işlem sprey ve/veya daldırma yöntemiyle yapılabilir. Örneğin, bir otomotiv kataforez hattında hem sprey hem daldırma yağ alma banyoları ardışık kullanılabilir.
Durulama: Yağ alma sonrası parçalar su ile durulanarak temizleyici kimyasal ve çözünen kirlerin uzaklaştırılması sağlanır. Genellikle birinci durulama şehir suyu ile, ardından ikinci bir durulama deiyonize (DI) su ile yapılır.
Aktivasyon: Fosfat kaplamadan önce, metal yüzeyde homojen ve ince kristalli bir fosfat tabakası oluşmasını teşvik etmek amacıyla aktivasyon banyosu uygulanır. Aktivasyon çoğunlukla titan veya nikel içeren düşük konsantrasyonlu bir çözelti ile gerçekleştirilir ve fosfatlama reaksiyonunun çekirdeklenmesini iyileştirir.
Fosfatlama (Konversiyon kaplama): Yüzey hazırlığın kritik adımı olup, parçalar genellikle çinko fosfat veya demir fosfat banyosuna daldırılarak metal yüzeyinde çözünmeyen bir fosfat konversiyon tabakası oluşturulur. Çinko fosfatlama, otomotiv gibi yüksek korozyon direnci istenen uygulamalarda yaygın olarak kullanılır ve yüzeyde ince kristalli bir çinko-fosfat tabakası bırakır. Bu tabaka, kataforez boyanın yapışmasını ve korozyona karşı direncini önemli ölçüde artıran pürüzlü ve reaktif bir yüzey sağlar.
Pasivasyon (Duraklatma) ve Durulamalar: Fosfatlama sonrasında parçalar tekrar su ile durulanır ve yüzeyde kalan çözünür tuzları gidermek için bir pasivasyon adımı uygulanabilir. Pasivasyon, fosfat kaplama üzerini silikat veya organik bazlı bir kaplama ile işlemden geçirerek korozyona karşı ek bir koruma sağlar ve fosfat tabakasının kararlılığını artırır. Geleneksel olarak kromat bazlı pasivasyonlar kullanılmış olsa da çevre ve sağlık nedenleriyle artık genellikle krom içermeyen pasivasyon kimyasalları tercih edilir. Son olarak, parçalar kataforez banyosuna girmeden hemen önce deiyonize su ile son kez durulanarak yüzeyde hiçbir iletken kalıntı veya kir kalmaması sağlanır.
İyi bir yüzey hazırlığı, kataforez kaplamanın başarısı için şarttır. Temiz ve aktif bir yüzey, kaplamanın alt tabakaya güçlü yapışmasını ve homojen bir film oluşumunu sağlar. Uygun yapılmamış bir ön işlem, kaplama sonrasında kaplama altından korozyon ilerlemesi, boya kabarması veya yapışma zayıflığı gibi sorunlara yol açabilir.
Kataforez Kaplama Banyosu ve Elektrokimyasal Birikim
Ön işlemden geçen temiz ve fosfatlanmış parçalar, katodik kataforez boya banyosuna daldırılır. Bu banyoda parçalar negatif yüke (katot) bağlanır; tanka daldırılmış çözünür anotlar ise pozitif potansiyele bağlanır. Kataforez banyosu büyük oranda saf su ve içinde dağıtılmış boya katılarından oluşur: tipik olarak yaklaşık %80-90 deiyonize su ve %10-20 katı boya (reçine + pigment) içerir. Deiyonize su, boya katılarını taşıyıcı ortam olarak görev yapar; boya katıları ise kaplama filmini oluşturan reçine (bağlayıcı polimer) ve pigmentlerden oluşur. Reçine, nihai filmde korozyon direnci, mekanik dayanım ve kimyasal direnç gibi özellikleri sağlayan temel bileşendir; pigmentler ise filme renk, opaklık ve UV dayanımı gibi nitelikler kazandırır. Kataforez boyaların formülasyonunda ayrıca çok düşük oranda organik çözücüler ve katkı maddeleri (%5 civarı) bulunur ki bunlar viskoziteyi ayarlamak, film özelliklerini iyileştirmek ve banyoyu stabilize etmek için kullanılır.
Parçalar boya banyosuna daldırıldığında, doğru akım uygulanmasıyla birlikte elektrokimyasal bir reaksiyon başlar. Katot konumundaki parçanın yüzeyine yönelen pozitif yüklü reçine-pigment parçacıkları, parçaya doğru hareket eder (elektroforez) ve yüzeyde yük boşalmasıyla birlikte çökelir. Uygulanan gerilim seviyesi, oluşacak boya film kalınlığını belirleyen ana parametredir. Yeterli voltaj uygulanması, boyanın en girintili köşelere dek nüfuz ederek birikmesini sağlar; bu sayede karmaşık şekilli parçaların iç yüzeyleri, kaynak dikişleri, köşe ve kenarları dahil her bölgesi kaplanabilir. Tipik katodik kataforez uygulamalarında banyo voltajı yaklaşık 100-300 V aralığında olabilir; büyük otomotiv karoseri için ~250 V uygulama yaygındır. Parçalar banyoda birkaç dakika (örneğin 2-4 dakika) süreyle akım altında tutulur. Başlangıçta çıplak metal yüzey ile iletken boya dispersiyonu arasında güçlü bir elektriksel çekim olduğundan akım yoğunluğu yüksektir ve hızlı bir kaplama oluşur. Kaplama filmi kalınlaştıkça, film dielektrik bir bariyer oluşturmaya başlar ve parça yüzeyinin iletkenliği düşer. Hedef kalınlığa ulaşıldığında film tabakası parçayı elektriksel olarak yalıtır ve akım akışı doğal olarak azalarak kaplama birikimi dengelenir. Bu öz-durdurucu mekanizma sayesinde, her noktada yaklaşık eş kalınlıkta bir kaplama elde edilir ve aşırı kaplama oluşumu engellenir.
Boya parçacıklarının katot üzerinde çökmesi, aynı zamanda suyun elektroliziyle yakından ilişkilidir. Katotta suyun ayrışması sonucunda hidroksil (OH^–) iyonları oluşur ve bu yerel pH artışı, önceden asit ile nötralize edilerek suda dağılmış halde bulunan reçineyi çözünmez hale getirir. Reçine ve pigmentler bu noktada katot yüzeyine yapışarak bir film oluşturur. Anotta ise ters reaksiyonla asitlik artışı olur; sistemde biriken bu asidik yan ürünler, genellikle anotları çevreleyen membranlı hücreler (anolit devresi) aracılığıyla banyodan uzaklaştırılır. Anot dairesinde toplanan asidik permeat çözelti, periyodik olarak dışarı atılır ya da nötralize edilir; böylece banyo kimyası dengede kalır ve pH yükselmesi sınırlandırılır. Bu dengeleme, sürekli proses koşullarında pH’ı yaklaşık 5,7–6,0 aralığında tutarak emülsiyonun kararlılığını sürdürmek için kritiktir.
Kataforez banyosunda boya parçacıklarının çökelmesiyle birlikte su ve diğer bileşenler de serbest bırakılır. Bu nedenle çalışma banyosunda iletkenlik ve iyon yoğunluğu zamanla artma eğilimindedir. Banyo iletkenliği genellikle ~1000-2000 µS/cm aralığında kontrol edilir; Eğer iletkenlik çok fazla artarsa, kaplama kalınlığının kontrolü zorlaşabilir veya yan reaksiyonlar artabilir. Bu nedenle, ultrafiltrasyon (UF) üniteleri kullanılarak banyodan belirli bir miktar permeat çözeltisi çekilerek sistem dışında saflaştırılır ve iletkenliğin istenilen aralıkta tutulması için temiz saf su veya deiyonize su eklenir. DI su arıtımında ters ozmoz veya elektrodeiyonizasyon sistemleri kullanılabilir. Ayrıca boya banyosuna belirli aralıklarla konsantre boya (reçine-pigment pastası) ve nötralize edici madde eklenerek banyonun kimyasal bileşiminin (katı madde yüzdesi, nötralizasyon derecesi vb.) sabit tutulması sağlanır.
Durulama ve Kaplama Sonrası İşlemler
Parçalar, kataforez banyosundaki kaplama işlemi tamamlandıktan sonra yavaşça banyodan çıkarılır ve hemen kaplama sonrası durulama istasyonlarına girer. Bu aşamanın amacı, parça üzerinde banyo dışına taşan fazla boyayı (henüz yüzeye yapışmadan kalan “krem kaplama” tabakasını) geri kazanmak ve kaplamanın düzgünlüğünü artırmaktır. İlk durulama genellikle kataforez banyosundan alınan ultrafiltre edilmiş permeat solüsyonu ile gerçekleştirilir. Parçadan süzülen fazla boya parçacıkları bu durulama sayesinde tekrar sisteme döndürülür; durulama tanklarında biriken boya, filtrasyon ile yoğunlaştırılıp ana boya tankına geri beslenir. Bu geri kazanım prensibi sayesinde süreçte boya malzemesi verimliliği %95’in üzerine çıkabilir. Yani, banyodan çıkan parçanın yüzeyindeki hemen hemen tüm boya ya film olarak parçada kalır ya da durulamalarla tekrar tanka kazandırılır, atığa giden boya miktarı çok düşüktür.
İlk kaba durulamadan sonra bir veya iki kademeli deiyonize su durulaması yapılır. Bu aşamada parçaların üzerinde artık hiçbir boya kalıntısı veya iletken madde kalmaması hedeflenir. Özellikle son durulama, tamamen saf su ile yapılır ve parçalar fırınlanmadan önce kısa süre bekletilmeden doğrudan fırına gönderilir. Parçaların yüzeyinde ıslak film halinde bulunan kaplama, fırınlama öncesi durulamalarda bozulmadan korunmalıdır; bu nedenle durulamadan fırına geçiş hızlı olmalı ve ortamda toz, kir gibi kontaminantlardan uzak tutulmalıdır.
Bazı sistemlerde, durulama aşamasından sonra parçalar fırına gitmeden önce kısa bir süre düşük sıcaklıklı bir “flash-off” (uçurma) bölmesine alınabilir. Bu, üzerlerindeki suyun bir kısmının buharlaşmasını sağlayarak fırında ani buharlaşmayla oluşabilecek kusurları (örneğin kaynama kabarcıkları) önlemeye yardımcı olur. Ancak çoğu modern kataforez hattında, doğrudan durulamadan çıkan ıslak parçalar kontrollü hızda fırına girer ve ısınma sırasında suyun büyük bölümü zaten buharlaşır.
Fırınlama ve Kürleme
Kataforez ile kaplanan ve durulanan parçalar, boyanın kimyasal olarak kürlenip sağlam bir film haline gelmesi için fırınlanır. Bu aşamada parçalar bir konveyör sistemiyle kurutma/kürleme fırınına girer. Fırın sıcaklığı ve süre, kullanılan boya malzemesinin kürlenme özelliklerine göre belirlenir. Tipik katodik epoksi kataforez boyaları, yaklaşık 160-200°C aralığında parça sıcaklığına çıkarılarak 20-30 dakika tutulmak suretiyle tamamen polimerleşir (çapraz bağlanır). Örneğin, yaygın uygulamalarda 190°C parça sıcaklığında en az 20 dakika kürleme gerekli görülür. Bu genellikle fırın hava sıcaklığının ~180-200°C’ye ayarlanması ve parçanın ısı kapasitesine göre yeterli konveyör hızı ile sağlanır. İnce sac malzemeler daha hızlı ısınırken, kalın döküm parçaların çekirdek sıcaklığına ulaşması için daha uzun süre gerekebilir. Boya üreticilerinin teknik föylerinde, kürleme için gerekli minimum zaman-sıcaklık kombinasyonu belirtilir (örn. 20 dk/180°C veya 30 dk/160°C gibi eşdeğer kürleme koşulları).
Kürleme sırasında kataforez boyanın içeriğindeki reçine (genellikle epoksi reçine) kimyasal reaksiyonla sertleşir. Isının etkisiyle reçine içerisindeki reaktif gruplar (örn. epoksi halkaları) açılarak çapraz bağlar oluşturur ve termal olarak dayanıklı, sert bir polimer ağ yapısı meydana gelir. Bu sayede kaplama filmi, alt tabakaya kuvvetle yapışan, darbe ve çizilmeye dayanıklı, yoğun bir koruyucu tabaka haline gelir. Fırınlama sürecinde ayrıca boya filmindeki uçucu bileşenler (suyun kalıntıları ve organik çözücüler) buharlaşarak uzaklaşır. Modern kataforez boyalar düşük uçucu içerikli olduğundan fırında çıkan gaz atıkları nispeten azdır ve genellikle termal oksidasyonla arıtılır. Kürleme sonunda parçalar fırından çıkar çıkmaz soğumaya bırakılır; soğuma genelde ortam havasında gerçekleşir ancak bazı hatlarda zorlanmış fanlarla soğutma da uygulanabilir. Kaplanan parçalar, dokunulabilecek kadar soğuduktan sonra bir sonraki üretim adımına (örneğin otomotivde zımparalama ve sonkat boyamaya veya doğrudan montaj hattına) sevk edilir.
Son Kalite Kontrol
Kataforez kaplama işleminin son aşaması, kaplanmış parçaların kalite kontrolüdür. Bu adımda, kaplamanın istenen özellikleri sağlayıp sağlamadığı çeşitli test ve ölçümlerle doğrulanır:
Görsel Muayene: Parçalar üzerinde herhangi bir kaplanmamış bölge (çıplak metal), renk veya ton farklılığı, yüzeyde çökelti veya tane, akıntı, kabarcık gibi kusurlar olup olmadığı gözle ve standartlara göre kontrol edilir. Kataforez kaplama genellikle yarı mat düz renk (siyah veya gri) bir astar tabakası oluşturur; dolayısıyla kaplamanın homojen görünmesi beklenir. Özellikle karmaşık geometrili parçalarda iç kısımlara boya ulaşmaması (throwpower eksikliği) riskine karşı, kritik bölgeler kontrol edilir. Gerekirse kesit alarak iç yüzey kaplamasına bakılabilir. Kenar köşe örtünmesi de değerlendirilir; bu amaçla bazı standart test parçaları (örneğin keskin kenarlı numuneler) proseste kaplanarak kenarlardaki film kalınlığı incelenir.
Kalınlık Ölçümü: Kaplama film kalınlığı, performans için kritik bir parametredir ve her partide ölçülür. Ölçüm genellikle tahribatsız manyetik indüksiyon veya girdap akımı (eddy current) esaslı kalınlık ölçüm cihazlarıyla yapılır (örn. çelik üzerindeki boya kalınlığını ölçen el tipi cihazlar, ISO 2178/ASTM D7091 uygun). Tipik kataforez astarı kalınlığı 15-35 µm civarındadır; otomotiv uygulamalarında ~20 µm hedeflenir. Ölçülen değerler, istenen tolerans aralığında olmalıdır (ör. \pm2-3 µm). Kalınlığın düşük çıkması, yetersiz korumaya yol açabileceği için proses ayarları gözden geçirilir; yüksek çıkması ise ekonomik kayıp ve boyanın çatlama riski demektir. Bu yüzden kalınlık değerleri sürekli kontrol altında tutulur.
Yapışma (Adhesion) Testi: Kaplamanın alt zemine yapışma direnci, standart çizik-kazıma veya çapraz kesme testleriyle değerlendirilir. Yaygın bir yöntem çapraz kesme yapışma testidir (cross-cut); bu testte kaplama yüzeyine kontrollü şekilde keskin bir bıçakla kare desen çizilir ve yapışkan bir bant yapıştırılıp çekilir. Kalan boya yüzdesine göre ISO 2409 standardına göre 0'dan 5'e sınıflandırılır. Kataforez kaplamalarda Gt0 veya Gt1 (%0–5 boya kalkması) sonucu beklenir ki bu en iyi sınıf sayılır. Örneğin, iyi bir kataforez kaplama sonucunda çapraz kesme testinde kesik kenarlarının tamamı düzgün kalmalı ve hiçbir kare tamamen soyulmamalıdır.
Sertlik ve Dayanım Testleri: Kaplama filmine gerektiğinde sertlik (kalem sertlik testi, pendül sarkaç testi), darbe dayanımı (falling weight test) gibi mekanik testler uygulanabilir. Kataforez astarlar genellikle sert bir film oluşturur (pencil hardness genellikle H-2H civarı). Ayrıca taşa darbeye dayanım (çakıl testi) özellikle otomotiv parçalarında kontrol edilen bir özelliktir; kaplamanın çakıl darbesiyle çatlamaması veya minimum zarar görmesi istenir.
Korozyon Direnci Testleri: Kaplamanın korozyon direnci, belirli aralıklarla veya numune bazında hızlandırılmış yaşlandırma testleri ile doğrulanır. En yaygın test tuz püskürtme testidir (tuz sisi testi, %5 NaCl püskürtme, 35°C ortam, ISO 9227 / ASTM B117 standardı). Kataforez astarları genellikle 500 saatin üzerinde tuz sisi testine dayanacak şekilde formüle edilir; Otomotiv gereksinimleri genellikle >1000 saatlik paslanmazlık gerektirir. Test sonunda kaplamanın altında kabarma veya pas ilerlemesinin varlığı ASTM veya ISO değerlendirici standartlarına göre ölçülür (örneğin pas ilerleme mesafesi mm olarak). Örneğin, bir sistem 504 saatlik tuz testinde <1 mm ve 1008 saatte <1,5 mm'yi hedefleyebilir. Ayrıca nem/yoğuşma testleri (ISO 6270-2, sürekli %95 nem, 40°C gibi koşullarda 240-480 saat) uygulanarak yapışma kontrolü yapılabilir. Müşteri istekleri doğrultusunda iklim çevrimi testleri (VDA 621-415 gibi değişken sıcaklık-nem-tuz çevrimleri) ve termal şok testleri de yapılabilmektedir. Tüm bu hızlandırılmış testler, katodik elektrokaplamanın gerçek hayatta uzun yıllar korozyon direnci sağlayacağının göstergesi olarak kullanılmaktadır.
Diğer Kontroller: Kaplamanın elektriksel yalıtkanlığı, kalınlığıyla orantılı olarak zaten yüksektir; ancak özel uygulamalarda dielektrik dayanım ölçümleri yapılabilir. Kimyasal direnç testleri (örneğin akaryakıt, motor yağı, fren hidroliği, antifriz temasına dayanım) otomotiv parçaları için önemli olabilir ve standartlara göre test edilir. Renk veya parlaklık genelde astar için kritik değildir (zira üzerine sonkat gelir), fakat dekoratif amaçla kullanılan kataforez uygulamalarında (örneğin tek kat siyah kaplama yapılan şasi parçaları) renk bütünlüğü ve UV dayanımı kontrol edilebilir. Epoksi kataforez boyalar UV ışığında tebeşirlenme yapabildiğinden, direkt güneş altında kullanılacak parçalarda poliüretan bazlı üst kaplama gerekliliği de kalite planlamasında dikkate alınır.
Ölçülecek ve Kontrol Edilecek Parametreler
Kataforez kaplama prosesinde kaliteyi ve sürekliliği sağlamak için hem banyo koşullarına ait kimyasal parametreler hem de uygulamaya ait elektriksel/füziksel parametreler düzenli olarak izlenir. Ayrıca elde edilen kaplamanın belirli kalite kriterlerini karşılaması için çıkışta bazı ölçümler yapılır. Bu bölümde, kritik parametreler ve bunların tipik değer aralıkları ele alınmaktadır:
Kimyasal Banyo Parametreleri: Kataforez boya banyosunun kimyasal dengesi, kaplama kalitesini doğrudan etkiler. Öncelikle pH değeri kritik bir parametredir. Katodik sistemlerde boya banyosu pH’sı tipik olarak hafif asidik bölgede, yaklaşık 5.7 – 6.0 aralığında tutulur. Bu aralık, reçinenin suda çözünür (emülsifiye) kalması için yeterli nötralizasyonu sağlar, ancak çok yükselmediği için reçine henüz çökelmez. pH değeri bu optimum aralığın dışına çıkarsa istenmeyen sonuçlar doğurur: Örneğin pH yükselirse reçinenin çözünürlüğü azalır, emülsiyon kararlılığı bozulur ve boya tankında pıhtılaşmalar başlayabilir. Bu da filtrelerin, membranların tıkanmasına yol açar ve banyo çamurlaşabilir. Tersine, pH çok düşerse (aşırı asidik), bu sefer tesisat içinde asidik korozyon artar, demir gibi metal iyonları çözünebileceğinden boya rengine kirlenmeler ve membran tıkanmaları görülebilir. Dolayısıyla pH, günlük olarak ölçülür ve gerektiğinde kimyasal eklemelerle ayarlanır.
Bir diğer önemli parametre iletkenlik (İletkenlik = elektriksel iletkenlik, genelde µS/cm cinsinden) değeridir. Banyo iletkenliği, boyanın iletimle akım taşıma kabiliyetini gösterir ve kaplama esnasında geçen akım yoğunluğunu etkiler. Çalışan bir kataforez banyosunda, kaplama sırasında oluşan yan ürünler (çözünür tuzlar), eklenen nötralizanlar (örneğin asit veya amin) ve konsantre boyadan gelen iletkenlik katkıları nedeniyle iletkenlik zamanla artma eğilimindedir. İletkenliğin çok yükselmesi, banyoda istenmeyen iletken safsızlıkların biriktiğini gösterir ve kaplamanın düzgünlüğünü etkileyebilir. Tipik olarak kataforez banyosu iletkenliği 800 – 2500 µS/cm aralığında kontrol edilir (not: bazı kaynaklar bunu mS olarak ifade etse de pratikte ~1-2.5 mS/cm mertebesindedir). İletkenlik üst sınırı aşılırsa, genellikle ultrafiltrasyon ile bir miktar banyo solüsyonu dışarı alınarak saf su ilavesiyle düşürülür. Çoğu tesis, su iletkenliğini kontrol eden PLC sistemlerine sahiptir ve iletkenlik değeri eşik değeri aştığında ilgili saf su arıtma sistemini devreye sokacak şekilde tasarlanmıştır. Ayrıca iletkenliği ayarlamak için çözücü seviyesinin artırılması veya banyo sıcaklığının değiştirilmesi de yöntemler arasındadır.
Banyo sıcaklığı, kimyasal ve elektrokinetik parametreleri etkilediğinden kontrol altında tutulur. Yüksek sıcaklık boya dispersiyonunu kararsız hale getirebilir veya buharlaşmayı artırırken, düşük sıcaklık kaplama hızını ve akım verimini düşürebilir. Çoğu kataforez banyosu oda sıcaklığına yakın veya biraz üzeri bir değerde (örneğin 28-32°C) çalıştırılır. Sıcaklık aynı zamanda iletkenlikle ters orantılı olarak viskoziteyi de etkiler; sıcaklık artışı boyayı akışkan hale getirip iletkenliği bir miktar yükseltebilir. Bu yüzden tanklarda ısıtma/soğutma serpantinleri bulunur ve sıcaklık sabit tutulur.
Katı madde oranı (boya konsantrasyonu): Banyo içerisindeki katı boya yüzdesi (% solid) genellikle belirli bir aralıkta olmalıdır. Tipik bir katodik astar banyosunda %12-15 katı madde bulunması öngörülür (örneğin formülasyona göre %14-18 istenir). Bu değer, kaplama kalınlığı ve verimini etkiler; çok düşükse istenen film kalınlığına ulaşmak güçleşir, çok yüksekse banyo viskozitesi artar ve stabilitesi bozulabilir. Katı madde miktarı, belirli aralıklarla alınan banyo örneklerinin gravimetrik analiz ile kurutulup tartılması yöntemiyle ölçülür. Örneğin 1-2 g banyo numunesi 110°C’de etüvde kurutularak kalıntı yüzde hesabı yapılır.
Asit değeri (Toplam/Nötrleme Asidi): Kataforez boyalar, reçineyi suda çözünür kılmak için genelde organik asitlerle nötralize edilir (katodik sistemlerde organik asit nötrleştirici ile pozitif yüklü amino-reçine oluşur). Banyo yaşlandıkça serbest ve bağlı asit miktarları değişebilir. Bu nedenle toplam asit sayısı ve serbest asit değerleri titrasyon analizleri ile takip edilir. Örneğin belirli bir hacim banyo numunesine uygun çözücüler eklenip 0.1 N NaOH ile pH metre eşliğinde titre edilerek asidite sayısı hesaplanır. Boya üreticileri genellikle “asit oranı” için bir hedef aralık verir (ör. acid ratio), bu da reçinenin nötralizasyon derecesini ve dolayısıyla parçaya yüklenme kabiliyetini gösterir. Bu parametre kontrol edilerek banyoya gerektiğinde nötralizan (amin) veya asit ilavesi yapılır.
Yukarıdakilere ek olarak banyonun yoğunluğu, viskozitesi, içinde dağılmış pigmentlerin tane boyutu dağılımı, çamur/çökelti miktarı gibi diğer kimyasal parametreler de izlenebilir. Ancak rutin olarak en kritik olanlar pH, iletkenlik, katı yüzdesi ve asitliktir denilebilir. Bu parametrelerin istenen aralıklarda tutulması, her gün/hafta düzenli analizlerle sağlanır ve trendler takip edilerek proaktif önlem alınır.
Elektrokimyasal Parametreler: Kataforez prosesi bir elektro-kaplama olduğu için elektriksel kontrol parametreleri de çok önemlidir. Uygulanan gerilim (voltaj) en temel parametredir; tipik olarak doğru akım güç ünitesi (redresör) istenen voltaj değerine ayarlanır ve kaplama süresince bu voltaj korunur. Ürün tipine göre 50-400 V arası değerler kullanılabilir. Daha yüksek voltaj, daha fazla boya parçacığının hızla çekilerek daha kalın film oluşmasını sağlar; ancak çok yüksek voltaj istenmeyen elektroliz yan etkilerini (örneğin metal yüzeyde hidrojen gazı kabarcıkları, “pin-hole” denen iğne deliği kusurları) tetikleyebilir. Bu yüzden her ürün ve boya için deneysel olarak belirlenmiş optimum bir voltaj profili vardır. Örneğin, otomotiv gövde kataforezinde kaplama süresinin ilk kısmında hızlı bir yükselişle 250 V’a çıkılır ve bir süre sabit tutulup sonra akım düşümüne göre azaltılır. Akım yoğunluğu ise parçaların geometrisine ve yüzey alanına bağlı olarak değişir; genellikle kaplama başlangıcında yüksek bir akım (örn. birkaç amper/dm²) görülür ve film oluştukça düşer. Proseste toplam geçirilen yük (amper-dakika) kaplama kalınlığı ile ilişkilidir. Bu nedenle gelişmiş sistemlerde ampere-dakika kontrolü de yapılır: Parça yüzey alanı ve istenen kaplama kalınlığına uygun olarak her tank için hedef bir A·dk değeri hesaplanır, bu değere ulaşıldığında kaplama sonlandırılır. Elektriksel parametrelerin takibi, genellikle otomasyon sistemi (PLC) üzerinden sürekli yapılır; anlık voltaj, akım ve süre değerleri kaydedilir. Eğer istenen aralıktan sapma olursa (örneğin akım çok düşükse parça askıda elektriksel temas sorunu olabilir, çok yüksekse banyo iletkenliği/pH sorunu olabilir) hemen operatöre alarm verilir ve düzeltilir.
Kaplama Kalitesi ve Homojenliği: Proses parametrelerinin doğru olması, sonuçta kaplamanın her noktada düzgün bir film oluşturması içindir. Kalite kontrolde belirtildiği gibi, kaplamanın homojen dağılımı önemlidir. Bunu sağlamak için atım mesafesi (throwpower) ve kenar-köşe kaplama performansı proses sırasında dikkate alınır. Örneğin daldırma süresi ve voltaj, derin ceplerde de yeterli kaplama oluşacak şekilde optimize edilir. Bazı üretimler, bu performansı ölçmek için standart test panelleri kullanır. Ford oto sanayinin throwpower testinde, belirli geometrik bir panelin iç yüzeyine ne oranda kaplama ulaştığı yüzde olarak ölçülür (ör. %60-65 atım mesafesi gibi). Kenar koruma için ise keskin kenarlı numunelerde kaplama kalınlığı değerlendirilebilir. Süreçte karıştırma/dolaşım sistemleri de homojenliği etkiler; banyo içerisinde sürekli düşük hızlı karıştırıcılar veya devridaim pompaları boya partiküllerinin sürekli askıda kalmasını ve her bölgede eşit konsantrasyonda bulunmasını sağlar. Eğer karıştırma yetersizse, tank içinde bölgesel konsantrasyon farkları kaplamada dalgalanmalara yol açabilir. Bu nedenle hem banyo koşulları hem de elektriksel dağılımın homojenliğini sağlamak için tesis tasarımında doğru pompaj, anot dizilimi ve askı (askı aparatları) tasarımı yapılır. Parçaların askıya asılış şekli de önemlidir: Parça üzerindeki cep bölgelerinden hava çıkışı ve banyo drenajı iyi olmalıdır ki her yere boya girebilsin ve çıkışta göllenme yapmasın.
Film Kalınlığı ve Korozyon Dayanımı: Bu iki özellik nihai üründe sağlanmak istenen en kritik performans göstergeleridir. Film kalınlığı üretim esnasında ölçülüp kontrol edilse de (bkz. kalite kontrol bölümü), proses parametreleriyle de ilişkilidir. Örneğin voltaj veya süre artırılarak daha yüksek kalınlık elde edilebilir. Ancak kataforez için belli bir ekonomik ve teknik optimum vardır (genelde ~20 µm); daha kalın filmler genellikle tavsiye edilmez çünkü boya malzemesi israfı olur ve üst kat boyalarda sorun yaratabilir. Korozyon dayanımı ise doğru uygulanan bir kataforez kaplamanın başlıca başarım kriteridir. Yukarıda belirtildiği gibi, standart testlerle ölçülür ve belli bir eşiğin üstünde olmalıdır. Korozyon dayanımını etkileyen süreç parametreleri arasında yüzey hazırlığı (fosfatın kalitesi), film kalınlığı, kürleme derecesi, boya formülasyonu sayılabilir. Dolayısıyla bu parametreler proses boyunca kontrol edilerek, her partide hedeflenen korozyon direnci seviyesine (örneğin otomotiv parçası için 500 saat tuz testinde belirlenen max pas ilerlemesi kriterine) ulaşılacağı güvence altına alınır.
Kalite ve Süreç Standartları: Kataforez kaplama prosesi ve sonuçları, uluslararası standartlarla da tanımlanmıştır. Örneğin boya kaplamaları için genel test yöntemlerini veren ISO ve ASTM standartları kataforez için de geçerlidir. ISO 9001 ve özellikle otomotiv için IATF 16949 gibi kalite yönetim standartları kapsamında kataforez hatlarının proses kontrol planları oluşturulur ve kayıt altına alınır. Teknik olarak, ISO 2409 (çapraz kesme yapışma testi) ile yapışma kontrolü yapılır ve genelde Gt0 veya Gt1 beklenir. ISO 2808 boya kuru film kalınlığı ölçüm yöntemlerini tanımlar ve kataforez kaplamaların kalınlık ölçümleri bu standarda göre yapılabilir. ISO 6270-2 nem dolabı testi standardı olup kataforez kaplı numunelerin ıslak sıcak ortamda dayanımını ölçer (ör. 240 veya 480 saat sonra yapışmada bozulma olmamalı) (). ISO 9227 (eşdeğeri eski DIN 50021 veya EN ISO 7253) tuzlu sprey test standardı olup kataforez astarın paslanma direncini değerlendirmede kullanılır. Ayrıca otomotiv üreticilerinin kendilerine özgü kataforez kaplama şartnameleri vardır (örneğin birçok OEM firmasının malzeme spesifikasyon numaraları [BMW, Ford, VW, etc.] Ege Eloksal firmasının listesindeki gibi). Prosesin çevresel boyutu için, atık sular ve uçucu emisyonlar açısından EPA standartları veya yerel çevre mevzuatı gereği değerler kontrol edilir; örneğin Avrupa’da ELV yönergesi gereği kataforez boyalarda ağır metal (kurşun, cıva, kadmiyum, Cr6+) kullanılmaz. Özetle, kataforez kaplama prosesi, ulusal ve uluslararası standartlara uygun şekilde yürütülür ve ürünler de ilgili test standartlarına göre doğrulanır.
Ölçüm ve Kontrol Yöntemleri
Kataforez kaplama sürecinde yukarıda bahsedilen parametrelerin kontrolü, çeşitli ölçüm yöntemleri ve cihazlarla gerçekleştirilir. Düzenli ölçümler, prosesin stabil kalmasını sağlar ve olası sapmalar erken tespit edilip düzeltilebilir. Ayrıca kalite kontrol testleri de belirlenmiş yöntemlerle yapılır. Bu bölümde, önemli parametrelerin ölçüm teknikleri, sonuçların nasıl yorumlandığı ve proses iyileştirme yaklaşımları anlatılmaktadır:
Banyo Kimyasal Analizleri: Kataforez banyosundan günlük veya haftalık alınan örnekler üzerinde bir dizi kimyasal analiz yapılır. pH ölçümü dijital pH metre ile gerçekleştirilir. Numune sıcaklığı standart değere getirilir (genellikle 25°C) ve kalibre edilmiş bir cam elektrotlu pH metre ile ölçüm yapılarak kayıt altına alınır. Örneğin çoğu tesis, pH’ı günde en az bir kez ölçer ve ideal aralık olan ~5.7-6.0 değerinin korunup korunmadığını denetler. pH sapması görüldüğünde operatör, boya tedarikçisinin talimatına göre düzeltici kimyasal ekler (pH yükselmişse sisteme kontrollü asit dozu, pH düşmüşse nötralizan amin eklemesi gibi).
İletkenlik ölçümü ise kalibre edilmiş bir kondüktivimetre cihazıyla yapılır. Banyo örneği belirli bir hücre konstantlı prob ile ölçülerek µS/cm cinsinden iletkenlik değeri okunur. Bu değerin genellikle ılımlı bir aralıkta kalması istenir (örn. 1000-1500 µS/cm). Tesisler iletkenliği de günlük kaydeder ve trend takibi yapar. Eğer iletkenlik sürekli artma eğilimindeyse, bu banyo birikimlerinin göstergesidir; çözüm olarak küçük bir oranda banyo deşarjı yapılıp saf su eklenebilir veya UF atık çıkışı artırılabilir. Örneğin, bazı işletmelerde iletkenlik belli bir eşik değeri (~2000 µS) aşarsa alarm verir ve otomatik olarak ultrafiltrasyon devreye girip fazla iletken iyonları uzaklaştırır. Ayrıca saf su arıtma sistemleri de devreye girerek banyoya yeni af su takviyesi yapar.
Katı madde (katı içerik) tayini, basit ama kritik bir testtir. Bu amaçla küçük bir alüminyum kap tartılarak içine belirli miktar (1-2 g) banyo örneği konur ve 105-110°C’de etüvde sabit ağırlığa gelene kadar kurutulur. Kurutma sonrası kalan kuru film miktarı tartılarak yüzde hesaplanır. Sonucun örneğin %15 civarında olması beklenir (hedef aralık üreticiye göre tanımlıdır). Bu test en az haftada bir yapılır. Eğer katı madde düşük çıkarsa, boyanın konsantrasyonu azalmış demektir; genelde boya besleme sisteminden bir miktar taze boya (reçine/pigment konsantresi) eklenir. Katı madde fazla ise, sistemde fazla boya birikimi vardır; saf su ilavesi veya boya beslemesinin azaltılması gündeme gelir.
Toplam asit ve serbest asit analizi titrasyon yöntemiyle yapılır. Laboratuvar teknisyeni, belirli hacimde banyo örneğini deiyonize su ve uygun organik çözücü (ör. izopropanol veya THF gibi) ile seyreltip, manyetik karıştırma altında fenolftalein indikatör eşliğinde 0.1 N NaOH çözeltisiyle titre eder. Dönüm noktasında (pH ~8.5 civarı) harcanan NaOH hacminden asidite sayısı (mg KOH/g veya benzeri birimle) hesaplanır. Bu değer, boyadaki nötralizan miktarının dolaylı ölçüsüdür. Örneğin “toplam asit değeri = 40 mg KOH/g” gibi bir hedef olabilir. Ayrıca ikinci bir titrasyon ile serbest asit (bağlanmamış asit) belirlenip ikisinin oranı (serbest/total) değerlendirilir. Titrasyon sonuçları spesifikasyona uymuyorsa, banyoya amin veya asit eklenerek nötralizasyon dengesi ayarlanır.
Banyo sıcaklığı ve diğer çevresel parametreler de ölçülür ancak bunlar genelde otomasyon sistemindeki sensörlerle sürekli takiptedir. Yine de, operatörler çapraz kontrol için tank termometrelerini okur veya veri kayıtlarını inceler. Sıcaklık istenenden farklıysa ısıtıcılar veya soğutucular ayarlanır. Banyodaki çamur/sementasyon miktarı da gözlemlenir; gerekiyorsa belirli aralıklarla banyonun durultulması veya filtrasyon sistemlerinin bakımı yapılır.
Elektro-kaplama Süreç Kontrolleri: Kaplama sırasında kullanılan elektriksel parametreler, modern tesislerde dijital olarak izlenir ve kontrol edilir. Redresör ekranlarından veya SCADA yazılım arayüzünden voltaj, akım, süre gibi değerler anlık görülebilir. Operatörler, her parti başında doğru programın seçildiğini ve voltaj rampalarının uygun olduğunu teyit eder. Örneğin büyük parçalar için yavaş bir voltaj yükseltme profili gerekebilirken küçük parçalarda hızlı yükseltme kullanılabilir. Akım zaman eğrisi de izlenir; akım beklenenden çok önce sıfıra düşüyorsa film çabuk yalıtıyor olabilir (belki aşırı kalın veya banyo katı madde yüksek), ya da akım düşmüyorsa kaplama tamamlanmıyor olabilir (belki yüzey hazırlığı kötü veya iletkenlik düşük). Bu işaretlere göre operatör süreç hakkında fikir sahibi olur. Gerekirse test panelleri askıya eklenerek kaplama sırasında akım dağılımı değerlendirilir.
Ayrıca askı aparatlarının iletkenliği, anotların durumu, kaplama süresince gaz çıkışı gibi konular da atölye personelince takip edilir. Askılarda boya birikimi ile yalıtkanlaşma olmaması için düzenli temizleme yapılır. Anot membranları periyodik kontrol edilir, tıkananlar temizlenir veya yenilenir (anolit devresi sağlıklı çalışmazsa banyo pH’ı kontrol dışına çıkabilir). Bütün bu kontrol faaliyetleri, proses parametrelerinin tanımlı tolerans aralıklarında kalmasını sağlamaya yöneliktir.
Kalite Test Yöntemleri: Nihai kaplama üzerinde yapılan testler belli standart yöntemlerle uygulanır (yukarıda bunların ne olduğundan bahsedildi). Örneğin kalınlık ölçümü için manyetik kalınlık ölçer kullanılır dedik; bu cihazlar genelde ISO 2178 veya ASTM D1186’ya göre çalışır. Cihazın doğru sonuç vermesi için çeşitli kalibrasyon foilleri ile kalibre edilmesi gerekir. Operatör, ölçümden önce cihazı bilinen kalınlıklarda test plakalarda dener. Ölçüm sırasında her parçadan birkaç farklı noktadan değer alınır ve ortalama kaydedilir. Çapraz kesme yapışma testi ISO 2409’a göre gerçekleştiriliyorsa, standart boyutta keskin bıçak ve bandın kullanılması önemlidir; sonuçlar standartta tanımlanan sınıflara göre notlanır () (). Tuz testi için ISO 9227 yöntemine uygun bir tuz sprey kabini kullanılır; belirli periyotlarda (örn. her üretim lotundan boyalı numune alınarak) test yapılabilir veya ürün onayı için tipik olarak 240, 480, 720 saat gibi sürelerde numuneler teste tabi tutulur. Test sonunda ASTM D1654 veya ISO 4628’e göre paslanma derecesi değerlendirilir. Nem testleri ISO 6270-2 uyarınca sabit sıcaklık/nem kabininde yapılır; süre sonunda numunede kabarma olup olmadığı ve yapışma testi ile değişim kontrol edilir (). Darbe testi ASTM D2794’e göre cihazla yapılabilir. Sertlik ISO 1518 (kalem sertliği) veya ISO 1522 (sarkaç sertliği König/Persoz) ile ölçülebilir, vs. Tüm bu testlerin yöntemleri ve kabul kriterleri kalite planlarında belirtilir ve eğitimli personel tarafından uygulanır.
Sonuçların yorumlanması, ilgili standartlara ve müşteri gerekliliklerine göre yapılır. Eğer herhangi bir test sonucu spesifikasyon dışına çıkarsa, o partinin ürünlerinde düzeltici önlemler alınır (örneğin müşteriyle görüşülüp ikinci bir kataforez veya ek koruyucu işlem yapılması gibi) ya da üretim durdurulup süreç ayarları yeniden gözden geçirilir. Örneğin yapışma testinde zayıf sonuç çıkarsa hemen yüzey hazırlığı tankları ve boya banyosu kimyasal değerleri kontrol edilir; genelde sorun ya fosfat tabakasında ya da boya banyosundaki bir dengesizlikte yatar.
Proses İyileştirme Yöntemleri: Kataforez kaplama prosesini kontrol altında tutmak kadar, sürekli iyileştirme yaklaşımıyla geliştirmek de endüstride yaygındır. Bu kapsamda, elde edilen ölçüm verileri uzun vadede istatistiksel proses kontrol teknikleriyle analiz edilebilir. Örneğin SPC kartları ile pH, iletkenlik gibi kritik parametrelerin dalgalanmaları izlenerek süreç kapasitesi değerlendirilebilir; Cpk değerleri düşükse, iyileştirme için kimyasal besleme otomasyonunun artırılması veya daha sık analiz yapılması gerekebilir. Benzer şekilde, hata türü ve etkileri analizi (FMEA) yapılarak kaplama hatasında potansiyel nedenler ve önlemler belirlenir.
Proses iyileştirme adına yaygın uygulamalardan bazıları şunlardır: Boya malzemesinin optimize edilmesi (örneğin daha düşük sıcaklıkta kürlenebilen yeni nesil kataforez boyalar kullanarak enerji tasarrufu sağlama, enerji geri kazanımı (fırınlardan çıkan sıcak havanın eşanjörlerle ısı geri kazanımı), otomasyon artırımı (manuel kontrollerin otomatik sensör ve PID kontrollere devredilmesi), daha iyi askı tasarımı (parça üzerindeki boya birikimini ve akım yayılımını iyileştirecek jig dizaynları), düzenli bakım ve temizlik (anot, filtre, tank temizliği ile kontaminasyon önleme), eğitim (operatörlerin proses değişkenlerinin etkileri konusunda sürekli eğitimi) ve kimyasal optimizasyon (örneğin fosfat yerine nano-seramik ön işlem kullanarak çamur atığını azaltma).
Ayrıca, eğer bir tesiste farklı renklerde kataforez isteniyorsa (nadir de olsa), tek banyoda renk değişimi zor olduğu için iki ayrı hat kurulması gibi stratejik kararlar alınabilir – bu da prosesin esnekliğiyle ilgilidir. Sık renk değişimi gereken durumlar için kataforez uygun olmadığından, proses planlaması da iyileştirmenin bir parçasıdır (örn. tek tip astar rengi kullanıp üst katlarda renk verme yaklaşımı).
Özetle, ölçüm ve kontrol yöntemleri sadece anlık durumu izlemek için değil, trendleri görerek sürekli geliştirmeler yapmak için kullanılmalıdır. Kataforez prosesinde küçük iyileştirmeler dahi (örneğin banyo ömrünün 6 aydan 12 aya çıkarılması, enerji tüketiminin %5 düşürülmesi, hatalı parça oranının binde 1 azaltılması gibi) büyük ekonomik ve çevresel faydalar sağlayabilir. Bu yüzden sanayi ve akademi, bu prosesi daha verimli, daha çevreci ve daha yüksek performanslı hale getirmek için işbirliği içerisinde çeşitli çalışmalar yürütmektedir.
Kaynaklar ve Akademik Çalışmalar
Kataforez kaplama konusunda literatürde hem akademik araştırmalar hem de sektör odaklı teknik dokümanlar oldukça zengindir. Bu proses, özellikle otomotiv sanayiinde kritik bir rol oynadığı için, yıllar içinde birçok bilimsel çalışma ile geliştirilmiş ve belgelenmiştir. Aşağıda konu ile ilgili bazı önemli kaynaklar ve çalışmalar özetlenmiştir:
Akademik Araştırmalar: Üniversiteler ve araştırma kuruluşları, kataforez kaplamanın korozyon performansını, malzemelerle etkileşimini ve proses parametrelerini konu alan çalışmalar yayınlamışlardır. Örneğin Akafuah ve çalışma arkadaşları (2016) otomotiv gövde boyama prosesinin evrimini inceleyen kapsamlı bir derleme makalesi yayınlayarak, kataforez teknolojisinin tarihsel gelişimini ve modern iyileştirmelerini detaylandırmışlardır () (). Bu çalışmada, ilk nesil anodik sistemlerden günümüz yüksek performanslı katodik sistemlerine geçişte, korozyon dayanımı artışı, çevre dostu formülasyonlara (ör. kurşunsuz boyalar) yönelim ve enerji verimliliği gibi konular ele alınmıştır. Yine akademik düzeyde, Yargıç vd. (2021) tarafından yapılan bir çalışmada sıcak dövme döküm malzemelerin farklı kaplama koşulları altında performansı incelenmiş ve kataforez kaplamanın bu malzemelerin korozyon ve aşınma dayanımına katkısı değerlendirilmiştir. Kılınç ve Akyalçın (2022) ise kataforez kaplanmış çelik yüzeyler üzerine uygulanan dubleks kaplama (örneğin üzerine çinko lamelli kaplama ve son kat boyalar) ile korozyon performansının nasıl iyileştiğini araştırmışlardır. Bu tür çalışmalar, kataforez kaplamanın tek başına veya kombine sistemlerde optimum koruma sağlaması için yol gösterici olmaktadır. Nitekim Kılınç (2019) tarafından bildirilen bir istatistiğe göre, kataforez kaplama ile ilgili dünya genelinde binlerce patent alınmış durumdadır; bu da sürekli bir yenilik ve geliştirme faaliyetinin göstergesidir.
Yüksek Lisans ve Doktora Tezleri: Türkiye’de de konuya dair akademik tez çalışmaları bulunmaktadır. Örneğin Özçanak (2008) Yıldız Teknik Üniversitesi’ndeki yüksek lisans tezinde, “Kataforez Kaplama Öncesinde Yüzey Hazırlama, Kurutma ve Kaplama Proseslerinin İncelenmesi” başlıklı kapsamlı bir çalışma yapmıştır. Bu tezde, özellikle ön işlemlerin kataforez kalitesine etkisi deneysel olarak incelenmiş, farklı fosfatlama ve kurutma koşullarının sonuçları değerlendirilmiştir. Bu tür tez çalışmaları, sanayideki gerçek proseslerin laboratuvar ortamında analiz edilmesi ve iyileştirme önerileri getirilmesi açısından değer taşımaktadır. Yine benzer şekilde, çeşitli üniversitelerde kataforezle ilgili boya kimyası, kaplama aderansı, kaplama defolarının analizi gibi konularda tezler gerçekleştirilmiştir.
Sektör Raporları ve Teknik Dökümantasyon: Otomotiv ana sanayileri ve boya üreticileri, kataforez prosesine dair teknik raporlar ve kılavuzlar yayınlar. Örneğin, büyük boya şirketlerinden PPG, Axalta, BASF gibi firmalar kataforez kaplama teknik föyleri ve kılavuz dokümanları sunarlar. PPG’nin bir teknik dökümanında kataforez prosesinin adımları (ön işlem, kaplama, durulama, fırın) ayrıntılı şekilde anlatılmış; banyo bileşiminin %80-90 su, %10-20 katı olduğu, kaplama veriminin %95’i aştığı ve tipik kür koşullarının 20 dakika 190°C olduğu belirtilmiştir. Bu tip dokümanlar, proses mühendisi ve teknisyenler için birer başvuru kaynağıdır. Yine otomotiv firmalarının malzeme şartnameleri önemli sektör referanslarıdır; örneğin Ford, GM, Volkswagen, Toyota gibi üreticiler kataforez astarın karşılaması gereken testleri ve özellikleri detaylandıran standartlar geliştirmiştir. Bu şartnamelerde kaplama kalınlığı, tuz testinde dayanım saati, taş çarpma test sonucu, elektriksel yalıtkanlık gibi bir dizi kriter tanımlanır. Kataforez kaplama yapan tedarikçiler, bu kriterleri sağladıklarını bu OEM standartlarına uygun test raporlarıyla kanıtlarlar.
Enerji ve Çevre Çalışmaları: Kataforez tesislerinin işletimi sırasında enerji tüketimi ve çevresel etkiler de araştırmalara konu olmaktadır. Örneğin Akbaş vd. (2018) bir otomobil montaj fabrikasının enerji tüketim analizini yaparken kataforez hattını ayrı bir proses olarak ele almış ve fırınlama başta olmak üzere nerelerde enerji tasarrufu yapılabileceğini ortaya koymuştur. Bu çalışma, kataforez fırınlarının ısı optimizasyonu, geri kazanım sistemleri ve genel hat verimliliği hakkında sanayiye yol gösterici veriler içermektedir. Çevresel tarafta ise atık su arıtımı (fosfatlama ve boyama tanklarından çıkan atıklar) ve uçucu organik bileşik emisyonlarının azaltılması üzerine teknik raporlar mevcuttur. Örneğin Avrupa Birliği’nde yayınlanan BREF (Best Available Techniques Reference) dokümanlarında, yüzey kaplama tesisleri için kataforez dahil en iyi uygulamalar ve emisyon kontrol teknikleri tanımlanmıştır.
Standartlar ve Kılavuzlar: Uluslararası standart kuruluşları (ISO, ASTM, DIN, TS vb.) kataforez ile doğrudan ilişkili bazı standartlar yayınlamıştır. Örneğin ISO 10683 ve EN 13858, her ne kadar daha çok çinko-lamelli kaplamalarla ilgili olsa da, kataforez gibi elektro-kaplamaların bağlantı elemanlarında kullanımına dair gereklilikleri de kapsar (). Ayrıca ASTM’ın elektroforetik kaplamalara özel standart test metotları bulunmaktadır (ASTM B767 – elektro-kaplama kalınlık ölçümü gibi). Bu standartlar, akademik çalışmalarda da referans olarak kullanılır.
Sonuç olarak, kataforez kaplama prosesi hakkında hem teorik hem pratik bilgi birikimi oldukça geniştir. Bilimsel araştırmalar, prosesin anlaşılmasını derinleştirirken, sektörel dökümanlar uygulamaya yönelik kılavuzluk sağlar. Bu raporda anılan kaynaklar ve benzer diğer literatür, kataforez kaplamanın gelişimini, optimal uygulama şartlarını ve kalite kontrolünü ortaya koyan önemli referanslardır. Bundan sonraki çalışmalarda da özellikle çevre dostu malzeme geliştirme (örneğin yeni nesil krom içermeyen ön işlem, daha düşük sıcaklıkta kürlenebilen reçineler) ve proses optimizasyonu (örneğin yapay zeka destekli banyo kontrolü) konularının ön planda olacağı öngörülmektedir. Bu sürekli gelişim, kataforez kaplamanın çeşitli endüstrilerde kritik bir yer tutmaya devam etmesini sağlayacaktır.