Condensate Polishing: Ensuring High-Purity Water for Power and Industrial Applications
Condensate polishing is a critical water treatment process designed to maintain the quality and purity of condensate water in power plants and industrial systems. By removing impurities such as dissolved solids, corrosion products, and organic contaminants, this process safeguards equipment, improves efficiency, and minimizes maintenance requirements. Condensate polishing is particularly vital in high-pressure steam systems, where even trace impurities can lead to scaling, corrosion, and operational inefficiencies.
The Importance of Condensate Water Quality
High-quality condensate water is essential for efficient operation, reduced energy consumption, and prolonged equipment life. Impurities like dissolved gases, hardness minerals, and suspended solids can cause significant issues, including corrosion and scale buildup. These problems lead to increased energy consumption, operational disruptions, and higher maintenance costs.
Key Parameters to Monitor in Condensate Polishing
- Conductivity and Total Dissolved Solids (TDS): High conductivity indicates elevated levels of dissolved salts, which can cause scaling and efficiency losses. TDS levels must be controlled to maintain optimal system performance.
- pH Levels: Imbalanced pH can accelerate corrosion or scaling. Monitoring and maintaining an optimal pH range is critical for system integrity.
- Dissolved Gases: Oxygen and carbon dioxide are common corrosive agents in condensate systems. Effective removal through degasification or chemical treatment is crucial to prevent damage.
Applications of Condensate Polishing
- Power Generation: Used extensively in nuclear and thermal power plants to ensure the purity of return condensate, thereby protecting turbines, boilers, and heat exchangers.
- Industrial Processes: Found in industries such as petrochemicals, refineries, and pulp and paper, where condensate reuse is essential for operational efficiency and sustainability.
- Desalination and Water Reuse Systems: Supports water recovery by ensuring high-quality recycled water.
Related Products for Condensate Polishing
Reverse Osmosis (RO)
Removes dissolved salts, organic contaminants, and fine particulates, ensuring ultra-pure water.
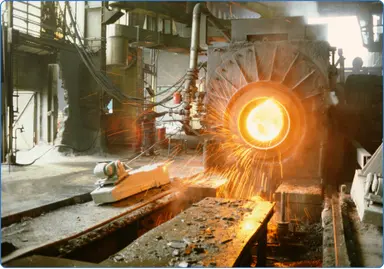
Ultrafiltration (UF)
Acts as a pre-treatment step to eliminate suspended solids and larger contaminants, protecting downstream equipment.
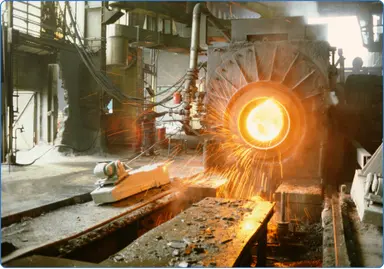
Deionization
Utilized for demineralization by removing cations and anions, reducing conductivity.
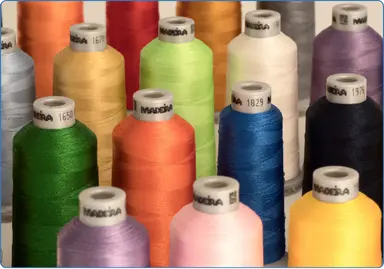
Mechanical Filtration
Captures particulates and corrosion products to enhance water clarity and prevent equipment fouling.
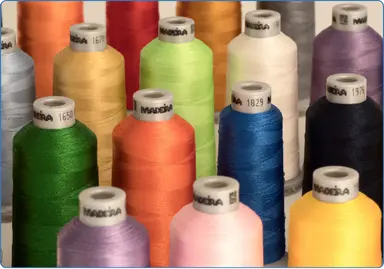
Degasification Systems
Removes dissolved gases like oxygen and carbon dioxide to prevent corrosion in the system.
Corrosion and Scale Prevention
- Corrosion Control: Corrosion erodes internal surfaces, reducing the lifespan of boilers and turbines. Treatment systems effectively remove corrosive agents, ensuring longevity.
- Scale Control: Scale acts as an insulator, reducing heat transfer and increasing energy demand. Advanced filtration and chemical treatments help prevent scaling.
Ensuring Long-Term Efficiency
Adopting advanced treatment technologies—such as reverse osmosis, ultrafiltration, and chemical dosing—keeps critical water parameters in check. Boilers and steam systems run more efficiently, experience fewer shutdowns, and comply with industry standards. By investing in high-quality condensate water management, facilities can maintain consistent operations, enhance safety, and reduce costs.
Real-Life Applications
- In a thermal power plant, implementing condensate polishing reduced annual fuel consumption by 15%, significantly lowering operational expenses.
- A petrochemical facility extended the lifespan of its boilers by 50% through consistent removal of dissolved solids and gases.
Challenges and Solutions in Condensate Polishing
While condensate polishing systems are highly effective, challenges such as resin fouling, scaling, and system downtime can occur. Solutions include:
- Automated Monitoring: Real-time sensors provide immediate feedback, allowing for quick adjustments.
- High-Performance Resins: Durable resins resist fouling and maintain efficiency over longer periods.
- Routine Maintenance: Regular inspections, resin regeneration, and filter replacements ensure system reliability.
Economic and Environmental Gains
- Energy Savings: Clean, impurity-free water improves heat transfer efficiency, reducing fuel consumption and energy costs.
- Reduced Maintenance Costs: Minimized corrosion and scaling lead to fewer repairs and longer equipment life.
- Regulatory Compliance: Adhering to strict environmental standards avoids legal penalties and demonstrates a commitment to sustainability.
- Sustainability Impact: By enabling water reuse and minimizing wastewater discharge, condensate polishing systems contribute to responsible resource management.
Supporting Technologies and Trends
- AI-Driven Monitoring: Advanced AI systems can predict potential issues and optimize treatment processes in real-time.
- Enhanced Resins: New resin technologies offer improved durability and contaminant removal efficiency.
- Modular Systems: Compact and scalable designs enable easy installation and adaptation to varying operational needs.
Recommended Parameter Ranges
- TDS: Maintain below 50 ppm for high-pressure boilers.
- pH: Maintain between 8.5-9.5 to minimize corrosion risks.
- Oxygen Content: Less than 5 ppb to prevent pitting corrosion.
Frequently Asked Questions (FAQ)
Routine maintenance, including resin regeneration and filter replacement, is typically required every 6-12 months depending on usage.
Power generation, petrochemicals, and pulp and paper industries are the primary beneficiaries due to their high reliance on steam systems.
Yes, modular and scalable designs can accommodate high flow rates and large industrial setups.
By reducing water waste and enabling reuse, these systems help minimize environmental impact and support sustainability.
Most systems achieve a return on investment within 2-3 years through energy savings and reduced maintenance costs.