Beverage Production Applications
Producing high-quality beverages requires more than just the right blend of ingredients—it hinges on a reliable and consistent water supply. In the food and beverage industry, water is a critical component not only as an ingredient but also for cleaning, rinsing, and cooling processes. Ensuring that this water meets stringent standards is essential for maintaining product quality, preventing contamination, and adhering to regulatory guidelines. Even slight deviations in water quality can impact the taste, aroma, and stability of the final product, making proper water treatment a cornerstone of successful beverage production.
To meet these demands, companies typically invest in advanced water treatment technologies designed to remove impurities, minimize microbial risks, and optimize resource consumption. From filtration and reverse osmosis to disinfection systems, each step in water treatment plays a vital role in delivering safe, consistent, and flavorful beverages. In doing so, producers also enhance their operational efficiency, reduce downtime, and maintain compliance with industry regulations. By understanding the intricacies of water treatment systems and how they integrate into various stages of beverage production, companies can significantly elevate the quality of their products, reduce operating costs, and protect brand integrity.
Common Water Treatment Systems Used in Beverage Production
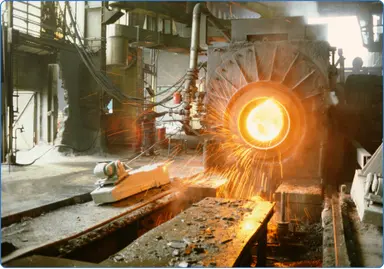
Multimedia Filtration
Filtration removes suspended solids, sediments, and other large particles. It ensures that the water entering the production process is free from any visible contaminants that could affect taste or safety.
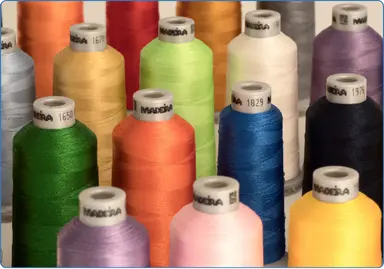
Activated Carbon Filters
These filters target chlorine, organic compounds, and unpleasant odors or tastes. They help improve flavor and aroma, which is particularly important in beverage production.
Reverse Osmosis (RO)
Reverse osmosis membranes remove dissolved salts, heavy metals, and other dissolved impurities. This stage ensures a highly purified water profile that can be tailored for different beverage formulations.
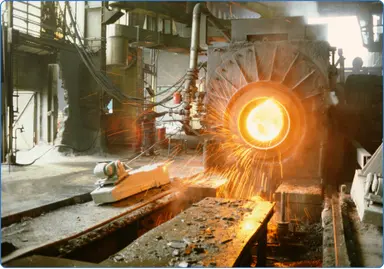
Water Softener
Ion exchange resins help soften water by removing calcium and magnesium ions. This system is often used to reduce scale formation and improve equipment efficiency.
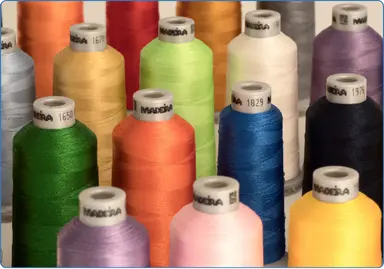
UV Disinfection
UV systems kill or inactivate microbes by exposing them to ultraviolet light. This step is crucial for preventing bacterial growth and ensuring microbiological safety.
Stages of the Beverage Production Process & Role of Water Treatment
- Ingredient Mixing and Formulation: At the formulation stage, reverse osmosis and activated carbon filters are typically used to produce high-purity water that does not interfere with the flavor profile of the beverage.
- Equipment Cleaning and Sanitation: Filtration and UV disinfection are widely used to supply clean water for rinsing and cleaning production lines, helping to prevent cross-contamination.
- Cooling and Heating Applications: Softened water (via ion exchange) or reverse osmosis-treated water is often required in boilers and cooling towers to prevent scale buildup and improve thermal efficiency.
- Final Product Adjustments: Ozonation and additional filtration ensure a microbiologically safe and stable product, essential for maintaining consistency in taste and quality.
Benefits of Using Water Treatment in Beverage Production
Implementing advanced water treatment solutions offers significant advantages. First, it helps maintain a consistent flavor profile, which is vital for brand reputation and consumer satisfaction. Second, high-quality water reduces the likelihood of contamination, extending product shelf life and reducing the need for preservatives or additives. Third, properly treated water minimizes equipment wear and tear by preventing scaling and corrosion, thereby cutting maintenance costs and reducing downtime. Lastly, compliance with health and safety standards becomes more straightforward, helping producers avoid regulatory penalties and potential product recalls.
By addressing the complete water treatment lifecycle—from initial filtration to final disinfection—beverage producers can craft products that meet consumer expectations and regulatory demands. Investing in the right mix of treatment technologies not only preserves the desired taste and aroma of beverages but also extends equipment life and bolsters operational efficiency.
This comprehensive approach to water treatment ultimately safeguards brand reputation and boosts profitability, positioning businesses for sustainable growth in a competitive market.
Water Quality Challenges & Solutions
The beverage industry often faces fluctuating water source quality due to seasonal changes, industrial pollution, and varying municipal supply conditions. These fluctuations can introduce unexpected contaminants or alter mineral compositions, jeopardizing the consistency of the final product. To address these issues, continuous monitoring of water quality is essential. Real-time sensors, automated controls, and periodic laboratory testing can detect any deviations early, allowing for prompt adjustments to treatment processes. In cases where extremely high purity is needed, multi-step treatment—such as combining reverse osmosis with UV disinfection or ozonation—provides a reliable defense against both chemical and biological contaminants.
Frequently Asked Questions
Q1: Why is water treatment so important for beverage production?
A1: Water treatment ensures the removal of contaminants that can affect taste, safety, and consistency. By producing clean, high-quality water, manufacturers maintain flavor integrity and comply with strict health standards.
Q2: Which treatment method is best for removing chlorine and improving taste?
A2: Activated carbon filtration is the most effective method for removing chlorine and improving the overall flavor of water, making it ideal for beverage production.
Q3: Do all beverage plants need reverse osmosis systems?
A3: While not mandatory for every operation, reverse osmosis is especially beneficial for products requiring very low mineral content or highly consistent flavor profiles. The decision depends on the specific water source and beverage formulation.
Q4: How often should these treatment systems be maintained?
A4: Maintenance frequency varies based on system load and water quality. Generally, filters should be replaced or cleaned regularly, and membrane systems like RO should be monitored to ensure optimal performance.