Vaccine Production Water Applications
Vaccine production is one of the most critical and tightly regulated areas in the pharmaceutical and biotechnology sectors. These life-saving biological products require stringent controls to ensure both safety and efficacy. Among the numerous components that go into vaccine formulation, water stands out as a key ingredient. In many cases, vaccines are composed primarily of water combined with active immunological ingredients, stabilizers, and other excipients. The purity, sterility, and precise chemical composition of water are vital to maintaining the product’s integrity and therapeutic potential.
Contaminated or substandard water not only risks the stability of the vaccine but can also introduce harmful microorganisms or particulate matter. Regulatory bodies such as the FDA, EMA, and the World Health Organization (WHO) impose strict guidelines on the type and quality of water used for vaccine manufacture. Deionized (DI) and Water for Injection (WFI)-grade water are often required to meet these high standards. Achieving these specifications typically involves advanced treatment processes such as Reverse Osmosis (RO), Deionization, and Ultraviolet (UV) or other sterilization methods to ensure the final water is both chemically pure and microbiologically safe.
Filtox specializes in providing comprehensive water treatment solutions tailored to vaccine production and other high-stakes pharmaceutical applications. By integrating multiple purification steps—such as RO, DI, and automated control systems—we help manufacturers consistently produce sterile and deionized water that meets or exceeds international pharmacopeial requirements. This approach guarantees reliable vaccine formulation while minimizing compliance risks, ensuring that patients receive safe and potent vaccines.
Related Products for Vaccine Production Water Treatment
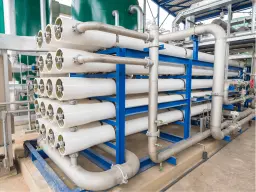
Reverse Osmosis (RO)
Reverse Osmosis is often the backbone of pharmaceutical water purification. By forcing water through a semi-permeable membrane under high pressure, RO removes a broad spectrum of contaminants, including dissolved solids, bacteria, and pyrogens. This step significantly lowers Total Dissolved Solids (TDS) and prepares water for subsequent polishing.
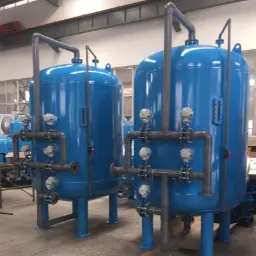
Deionization (DI)
Deionization systems remove ionic contaminants such as sodium, calcium, chloride, and sulfate, producing water with extremely low conductivity. For vaccine production, DI often follows RO to achieve ultra-pure water that meets stringent pharmacopeial standards, including Water for Injection specifications in certain processes.
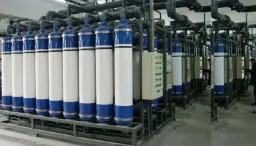
Ultrafiltration (UF)
Depending on the process requirements, ultrafiltration membranes can be used to remove particles, endotoxins, and even certain viruses. This extra layer of filtration is particularly relevant when vaccine formulations demand extremely low endotoxin levels, as specified in global pharmacopeias.
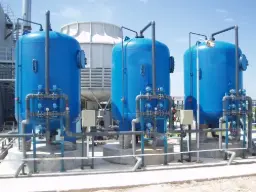
UV Sterilization
Ultraviolet (UV) systems expose water to specific UV wavelengths that effectively inactivate bacteria, viruses, and other microbes. UV sterilization is chemical-free and does not alter the water’s mineral composition. This method can be used in conjunction with other disinfection steps to maintain microbiological purity.
Advantages of Vaccine Water Treatment Systems
- Consistent Purity and Sterility
Multi-stage purification processes ensure that the water is free from contaminants, microorganisms, and unwanted ions, supporting the safety profile of the vaccine. - Compliance with Regulations
International guidelines—such as USP, Ph. Eur., and JP—mandate specific water quality requirements for pharmaceutical applications. Advanced systems help manufacturers meet these benchmarks to avoid costly compliance issues. - Enhanced Process Reliability
High-purity water reduces the risk of product recall or batch rejections due to contamination. Consistency in water quality is essential for reproducible vaccine formulations. - Scalability and Flexibility
Properly designed water systems can be scaled to meet production expansions. Whether manufacturing seasonal influenza vaccines or newly developed biologicals, flexible water treatment solutions can adapt to evolving demand. - Reduced Operational Costs
While high-end water treatment systems require an upfront investment, the long-term savings in reduced product losses, minimized downtime, and fewer quality deviations can be substantial.
Challenges and Solutions
- Challenge: Endotoxin and Pyrogen Control
Solution: High-temperature sanitization, ultrafiltration, and advanced RO/DI systems are effective in significantly reducing endotoxin levels. Regular monitoring ensures compliance with pharmacopeial limits. - Challenge: Microbial Contamination
Solution: UV sterilization, combined with proper piping design and routine sanitization, helps maintain low microbial counts. Ozonation can also be used for periodic system disinfection. - Challenge: Real-Time Quality Monitoring
Solution: Automated control systems equipped with sensors for conductivity, TOC (Total Organic Carbon), and microbial monitoring provide immediate feedback. Alarms and corrective actions can be triggered if parameters exceed set thresholds. - Challenge: High Capital and Maintenance Costs
Solution: Although pharmaceutical-grade water systems can be expensive, modular designs and integrated maintenance plans help control total cost of ownership. Energy-efficient pumps and water recovery strategies also reduce operating expenses. - Challenge: Upgrading Existing Facilities
Solution: Retrofitting older plants with modern water treatment technologies can be complex. Filtox offers customized solutions that incorporate space-saving designs, mobile skids, and phased installation to minimize disruption.
Frequently Asked Questions (FAQs)
- What is the difference between Purified Water (PW) and Water for Injection (WFI)?
Purified Water meets general standards for microbial and chemical purity. WFI, however, has stricter endotoxin limits and often requires distillation or equivalent technologies to ensure ultra-high purity suitable for injectable products, including many vaccines. - Does RO alone suffice for vaccine production water?
Typically, no. While RO significantly improves water quality, most vaccine processes also require final polishing steps like DI, UV, or ultrafiltration to meet stringent microbial and chemical purity standards. - How often should the system be sanitized?
The frequency depends on production demands, quality policies, and regulatory guidance. Many facilities perform routine sanitization (hot water, steam, or chemical) weekly, monthly, or whenever microbial monitoring indicates a rise in colony counts. - Can I recycle RO reject water?
Yes. Some facilities recycle RO concentrate for non-potable uses or treat it further for partial reuse. This approach can cut water consumption and lower operational costs, but must be designed carefully to avoid cross-contamination. - Is UV enough to guarantee sterility?
UV is highly effective against a broad range of microorganisms, but it’s generally paired with other methods. For vaccine applications, multi-barrier strategies (e.g., RO, ultrafiltration, UV) offer the highest level of assurance.